Have you ever wondered if your vacuum gauge is giving you accurate readings? If you’re relying on it for important measurements, ensuring its calibration is key. A miscalibrated gauge can lead to costly mistakes and wasted time.
Imagine you’re in the middle of a project, and your equipment isn’t performing as expected. You might be left scratching your head, unsure of whether the gauge is the problem or something else entirely. This article will guide you through the simple steps to calibrate your vacuum gauge, helping you achieve accurate results every time. By the end, you’ll feel confident in your ability to keep your equipment in top shape.
Key Takeaways
- Understanding Types: Familiarize yourself with different types of vacuum gauges—mechanical, electronic, piezoresistive, and capacitance—to choose the right one for your needs.
- Importance of Calibration: Regular calibration is essential for maintaining the accuracy, consistency, and compliance of your vacuum gauge, preventing costly errors.
- Necessary Tools: Equip yourself with essential calibration tools, including a calibration standard, digital multimeter, vacuum pump, and appropriate connectors, to ensure efficient processes.
- Step-by-Step Process: Follow a methodical calibration process: inspect the gauge, set up your equipment, compare readings, and make adjustments as necessary for reliable measurements.
- Troubleshooting Issues: Be aware of common calibration problems like inconsistent readings and calibration drift, and implement solutions to maintain gauge accuracy.
- Documentation: Keep a detailed calibration log to track your gauge’s performance over time, helping identify patterns and ensuring ongoing accuracy.
Understanding Vacuum Gauges
You rely on vacuum gauges for accurate measurements in various applications. Understanding their types and the importance of calibration enhances your ability to work effectively.
Types of Vacuum Gauges
- Mechanical Gauges: Mechanical gauges, such as Bourdon gauges, use a coiled metal tube that responds to pressure changes. These gauges provide visible readings and are commonly used due to their reliability in moderate vacuum ranges.
- Electronic Gauges: Electronic gauges utilize sensors to measure pressure levels and offer digital readouts. These gauges often feature higher accuracy and can cover a broad vacuum range.
- Piezoresistive Gauges: Piezoresistive gauges measure pressure based on the change in electrical resistance in a material. These gauges provide precise readings and are ideal for research applications.
- Capacitance Gauges: Capacitance gauges determine pressure via changes in capacitance in a diaphragm. These gauges excel in high vacuum environments and deliver accurate measurements.
Importance of Calibration
Calibrating your vacuum gauge ensures accuracy in measurements, influencing the success of your projects. Regular calibration prevents errors, which can lead to inefficiencies and costly failures.
- Precision: Regular calibration maintains the precision of your gauge, ensuring that you trust the readings for critical applications.
- Consistency: Calibration ensures your gauge delivers consistent results over time, regardless of changes in environmental conditions.
- Compliance: Many industries require adherence to specific standards. Calibration helps you maintain compliance with regulations, enhancing your credibility in the field.
- Maximized Equipment Life: Regular calibration contributes to the longevity of your equipment by identifying any issues early, which avoids further damage.
Ensuring your gauge is correctly calibrated keeps processes running smoothly, saving time and resources in the long run.
Tools and Equipment Needed
Calibration of a vacuum gauge requires specific tools and equipment for accurate results. Gathering the right items ensures efficient calibration and reliable measurements.
Recommended Calibration Tools
- Calibration Standard: Use a known reference gauge for accuracy verification. Select a high-quality unit that matches your gauge’s range.
- Digital Multimeter: Utilize this to check electrical readings, if applicable. A reliable multimeter provides precise voltage and current measurements.
- Vacuum Pump: Employ a vacuum pump to create the necessary low-pressure environment. Opt for a pump suitable for the gauge type and application.
- Connectors and Tubing: Prepare appropriate connectors and tubing for secure attachment. Ensure compatibility with both the gauge and calibration standard.
- Torque Wrench: Use a torque wrench for proper fittings’ tightness, ensuring no leaks. Follow manufacturer specifications to maintain consistency.
- Wear Protective Gear: Always use safety goggles and gloves. Protect yourself from potential risks associated with vacuum systems.
- Check Equipment Functionality: Verify that all tools and equipment are in good working condition before starting. Look for visible damage or wear.
- Ventilate Work Area: Ensure proper ventilation when working with vacuum systems. Improved air circulation minimizes gas buildup risks.
- Avoid Sudden Changes: Slow and gradual pressure changes prevent equipment damage. Steer clear of abrupt adjustments during the calibration process.
- Follow Manufacturer Guidelines: Adhere to specific instructions provided by the gauge or vacuum pump manufacturers. This practice helps maintain safety and accuracy.
Step-by-Step Calibration Process
Calibrating a vacuum gauge ensures accurate measurements. Follow these steps for effective calibration.
Preparing the Vacuum Gauge
- Inspect the Gauge: Check for any visible damage or wear. Ensure it’s clean and free from debris.
- Gather Tools: Collect a calibration standard, digital multimeter, vacuum pump, connectors, tubing, and a torque wrench.
- Setup: Connect the gauge to the vacuum pump using suitable tubing. Ensure all connections are secure to avoid leakage.
Calibration Procedure
- Establish Starting Point: Turn on the vacuum pump and create a vacuum. Monitor the gauge reading.
- Compare Readings: Use the calibration standard to determine the expected pressure corresponding to the gauge.
- Adjust Calibration: If the gauge reading doesn’t match the standard, use the adjustment screws. Carefully turn them to align the reading with the standard.
- Repeat Process: Create different vacuum levels with the pump and check readings at various points. Ensure consistency across the range.
- Cross-Verify: After adjustments, compare the gauge readings against the calibration standard once more.
- Document Results: Record any discrepancies and adjustments made during calibration. This can help with future calibrations.
- Regular Checks: Regularly recheck calibration at set intervals or after significant equipment changes. Consistent verification maintains accuracy over time.
Troubleshooting Calibration Issues
Calibration issues can affect the accuracy of your vacuum gauge readings. Identifying and resolving these issues helps ensure reliable measurements.
Common Problems
- Inconsistent Readings: Fluctuating or varying gauge readings indicate a calibration issue. These inconsistencies may arise from a loose connection or a faulty gauge.
- Calibration Drift: Over time, a vacuum gauge can lose accuracy. Calibration drift occurs when outputs differ from expected standards, typically due to wear or environmental factors.
- Improper Setup: Setting up the vacuum gauge incorrectly causes inaccurate readings. Factors like poor seal integrity or wrong connection size can lead to errors.
- Temperature Fluctuations: Changes in temperature influence vacuum pressure readings. High or low temperatures can cause the gauge to display inaccurate figures.
- Check Connections: Make sure all connections are tight and secure. Inspect hoses and fittings for damage. Replacing worn parts enhances accuracy.
- Recalibrate Regularly: Schedule calibration checks at regular intervals. Performing recalibration every 6 to 12 months maintains the integrity of measurements.
- Use Quality Standards: When calibrating, utilize materials or standards that you know to be accurate. Cross-referencing your gauge with a high-precision calibration standard helps identify discrepancies.
- Manage Temperature: Keep your working environment at a consistent temperature. Use insulating materials to shield the gauge from heat sources or cooling drafts.
- Document Results: Maintain a calibration log detailing the results of each calibration session. Record dates, reference standards, and any anomalies. This practice aids in identifying patterns over time.
By addressing these common problems and employing effective solutions, you can ensure your vacuum gauge performs accurately and reliably.
Conclusion
Taking the time to calibrate your vacuum gauge can make a world of difference in your measurements. By following the right steps and troubleshooting any issues that arise, you’ll ensure your gauge remains accurate and reliable. Remember that regular maintenance and documentation are key to long-term performance.
With a little diligence and care, you can keep your vacuum gauge in top shape, helping you achieve the precision you need in your work. Your commitment to accuracy will pay off in the quality of your results. Happy calibrating!
Frequently Asked Questions
What is a vacuum gauge and why is its accuracy important?
A vacuum gauge is a device used to measure the pressure in a vacuum system. Its accuracy is crucial because precise readings are essential for process control, safety, and compliance with industry standards. Inaccurate measurements can lead to equipment failure and subpar results.
How often should vacuum gauges be calibrated?
Vacuum gauges should be calibrated regularly, typically every six months to a year, depending on usage and manufacturer recommendations. Regular calibration helps ensure accurate measurements and compliance with industry standards.
What are the common types of vacuum gauges?
Common types of vacuum gauges include mechanical gauges (like Bourdon tube), electrical gauges (like capacitance manometers), and thermocouple gauges. Each type has its application, ranging from low to ultra-high vacuum measurements.
What tools are needed for vacuum gauge calibration?
Essential tools for vacuum gauge calibration include a reference gauge, a vacuum pump, and adapters for proper connections. Additional tools may include temperature sensors and data logging devices to monitor and record pressure readings.
What are some typical calibration issues with vacuum gauges?
Typical calibration issues may include inconsistent readings, calibration drift, improper setup, and temperature fluctuations. Addressing these problems is essential to ensure accurate and reliable gauge performance.
How can I troubleshoot calibration problems?
To troubleshoot calibration problems, check gauge connections, re-calibrate regularly, use quality reference standards, manage temperature variations, and document all results. These steps can help maintain gauge accuracy over time.
Why is documentation important in the calibration process?
Documentation is vital in the calibration process because it provides a record of measurements, calibration intervals, and any issues encountered. This information is necessary for compliance audits and ensuring the ongoing reliability of the vacuum gauge.
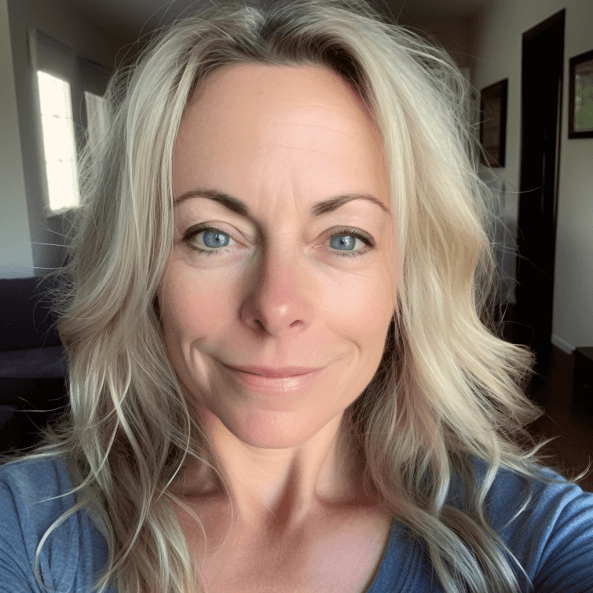