Dyson V11 Origin Cordless Vacuum, Nickel/Blue
- Versatile and cordless for whole-home deep cleaning.
Shark NV752 Rotator Powered Lift-Away TruePet Upright Vacuum with HEPA Filter, Large Dust Cup Capacity, LED Headlights, Upholstery Tool, Perfect Pet Power Brush & Crevice Tool, Bordeaux
- 2-IN-1 POWERED LIFT-AWAY TECHNOLOGY: Allows you to lift the pod away to deep-clean hard-to-reach areas, like under furniture, while the powered brushroll keeps spinning.
O-Cedar EasyWring Microfiber Spin Mop, Bucket Floor Cleaning System, Red, Gray, Standard
- HANDS-FREE WRINGING: Our exclusive mop bucket design features a built-in wringer that allows for hands-free wringing while Splash Guard keeps water splash and spray inside the bucket when wringing or when transporting the bucket from room to room
Electric Spin Scrubber for Cleaning Bathroom: Cordless Power Shower Scrubber - Electric Cleaning Brush for Tile Tub
- Multi-Surface Efficiency: Experience a deep clean across various surfaces with our Electric Spin Scrubber. Perfect for tiles, windows, bathtubs, toilets, and kitchen sinks. Effortlessly tackle dirt and grime where you need it most.
AIDEA Microfiber Cleaning Cloths, 50PK, Microfiber Towels for Cars, Premium All Purpose Car Cloth, Dusting Cloth Cleaning Rags, Absorbent Towels for SUVs, House, Kitchen, Window, 12"×12"
- Super Absorbent: Experience the excellent quality of AIDEA all-purpose microfiber cleaning cloths; made from 87% polyester and 13% polyamide; offering exceptional absorbency and quickly wicking away water to keep you dry; ideal for swiftly and safely removing dirt, grime, and liquids
Have you ever wondered how a vacuum ejector creates suction without any moving parts? It might seem like magic, but there’s a simple science behind it. Whether you’re in a workshop or managing a factory, understanding this tool can save you time and energy.
Key Takeaways
- Principle of Operation: Vacuum ejectors create suction using fluid dynamics principles, notably the Venturi effect, enabling efficient air or gas removal without moving parts.
- Components: Key elements include a nozzle for high-speed fluid jet generation, a Venturi tube to enhance vacuum effect, and an exhaust port for releasing expelled air.
- Versatile Applications: Common in industries such as packaging, material handling, medical devices, and semiconductor manufacturing, demonstrating their functional utility across various sectors.
- Advantages Over Electric Pumps: Vacuum ejectors are cost-effective, energy-efficient, and low maintenance, making them a preferred choice in many applications.
- Limitations: They are not suitable for generating very low vacuum levels or high flow rates and may require clean motive fluids to maintain performance.
- Environmental Impact: As eco-friendly devices, vacuum ejectors avoid the use of harmful materials and do not rely on complex machinery, supporting sustainable practices.
Overview of Vacuum Ejectors
Vacuum ejectors create suction using a fluid dynamics principle. They utilize high-velocity fluid to draw air or gas from a chamber without moving parts. This makes them reliable and low maintenance.
Components of a Vacuum Ejector
- Nozzle: Produces high-speed fluid jet. The fluid often comes from compressed air or other gas sources.
- Venturi tube: Enhances the vacuum effect. As fluid speeds up in the nozzle, it creates a low-pressure zone, pulling in surrounding air.
- Exhaust port: Releases expelled air or gas. It ensures a continuous process as the ejector operates.
How It Works
- Fluid Entry: Compressed air enters the nozzle.
- Jet Creation: The nozzle constricts the air, increasing its velocity.
- Pressure Drop: The high-speed jet causes a drop in pressure within the Venturi tube.
- Suction Effect: The low-pressure area draws in air, creating a vacuum.
- Discharge: The mixture of air and fluid exits through the exhaust port.
Applications
Vacuum ejectors commonly find use in various industries. Examples include:
- Packaging: Creating vacuum seals for food preservation.
- Material Handling: Lifting and transferring lightweight items.
- Medical Devices: Assisting in suction for procedures.
- Semiconductor Manufacturing: Maintaining clean environments during fabrication.
Advantages
Vacuum ejectors offer several benefits:





- No Moving Parts: Reduces maintenance costs and downtime.
- Simplicity: Easy to integrate into existing systems.
- Cost-Effective: Low operating costs compared to electric vacuum pumps.
Vacuum ejectors play a vital role in many applications, demonstrating efficiency without complex mechanisms. Understanding their operation enhances productivity in workshops and factories.
Working Principle of Vacuum Ejectors
Vacuum ejectors create suction using fluid dynamics, efficiently moving air or fluids without any moving parts. They rely on precise components and principles to perform effectively in various applications.
The Role of Nozzles
Nozzles serve as the entry point for high-pressure fluid, typically air, and enable acceleration. You direct this fast-moving stream through a constricted area, which decreases pressure. The design of the nozzle influences the velocity of the fluid, impacting overall performance. For instance, a well-shaped nozzle can maximize suction, enhancing the ejector’s efficiency.
The Importance of Venturi Effect
The Venturi effect plays a crucial role in creating suction. As fluid flows through the narrowed section of the ejector, it accelerates, dropping pressure as per Bernoulli’s principle. This pressure drop draws in surrounding air or fluid, forming a vacuum. In practical applications, utilizing the Venturi effect allows vacuum ejectors to maintain consistent suction levels, vital for processes in packaging, medical devices, and more. For example, in manufacturing, they efficiently pick up lightweight materials, significantly improving workflow.
Applications of Vacuum Ejectors
Vacuum ejectors find wide-ranging applications across numerous industries due to their efficiency and reliability. Understanding these uses highlights their versatility and importance in various processes.
Industrial Uses
Vacuum ejectors play a crucial role in many industrial sectors. They support material handling in manufacturing and packaging by providing consistent suction for lifting, moving, and securing products. For instance, they facilitate the automated loading and unloading of goods on conveyor systems.
Vacuum systems enhance the efficiency of plastic molding processes by creating a vacuum environment, helping mold fill uniformly. They also assist in vacuum forming, where sheets of plastic are shaped over molds using suction. Other industrial applications include:
- Food Processing: Vacuum ejectors help in packaging food products by removing air, improving shelf life.
- Pharmaceuticals: They ensure sterile conditions during the packaging and dispensing of medications.
- Woodworking: Vacuum systems hold wood materials in place during machining processes.
Scientific Applications
Vacuum ejectors also find extensive use in scientific applications. They support laboratories in various functions that require precise control over the environment. For example:
- Sample Collection: Vacuum ejectors facilitate the collection of gas or liquid samples in research settings.
- Vacuum Distillation: In chemistry, they create a vacuum that lowers boiling points, allowing distillation at lower temperatures.
Vacuum systems enhance experiments by providing controlled conditions. They help maintain an inert atmosphere for sensitive reactions, reducing contamination risks. Additionally, they aid in material separation processes, like filtration and evaporation, by generating the necessary vacuum pressure.
Advantages of Vacuum Ejectors
Vacuum ejectors offer numerous advantages that enhance efficiency and functionality across various applications.
Cost-Effectiveness
Vacuum ejectors provide a low-cost solution for creating vacuum systems. They typically require less maintenance than other vacuum generation methods, saving you time and money.
Simplicity and Versatility
Vacuum ejectors feature straightforward designs. Their simplicity allows for easy integration into existing systems. Versatile applications include material handling, packaging, and scientific processes, making them suitable for diverse industries.
Energy Efficiency
Vacuum ejectors operate without the need for moving parts, leading to lower energy consumption. This efficiency translates to reduced operational costs while still delivering reliable performance.
Compact Design
Vacuum ejectors usually come in compact sizes, requiring minimal installation space. This compactness is especially beneficial in environments with space constraints, allowing for efficient use of available areas.
Quick Response Time
Vacuum ejectors deliver rapid suction capability. Their quick response ensures immediate performance, essential for applications like material pick-and-place operations.
Low Noise Levels
Vacuum ejectors operate quietly compared to mechanical vacuum pumps. Low noise levels contribute to a more pleasant working environment, particularly in settings where sound minimization is crucial.
Minimal Maintenance Requirements
Vacuum ejectors require less maintenance than other vacuum generation methods. Their simple design minimizes wear and tear, reducing the frequency and extent of maintenance tasks.
Environmentally Friendly
Vacuum ejectors don’t rely on harmful materials or complex machinery, making them an eco-friendly option for vacuum generation. Their performance also contributes to sustainable practices in various industries.
By leveraging these advantages, vacuum ejectors support effective and efficient operation across multiple applications, enhancing productivity and reliability.
Limitations of Vacuum Ejectors
Vacuum ejectors, while effective, come with certain limitations that may affect their performance and applicability in specific situations.
Limited Vacuum Levels
Vacuum ejectors generate vacuum pressure through a combination of motive fluid flow and Venturi effect. However, their ability to reach very low vacuum levels is restricted. Applications requiring high vacuum, like semiconductor manufacturing, often necessitate alternative technologies.
Inefficiency at High Flow Rates
Ejectors perform well at low and medium flow rates but can be inefficient at high flow scenarios. As the flow of the motive fluid increases, the performance can decline. For large-scale operations requiring continuous high flow, you might consider different vacuum systems.
Dependency on Motive Fluid Quality
The quality of the motive fluid significantly influences ejector performance. Contaminants in the fluid can reduce efficiency and lead to wear. Using clean fluids or incorporating filtration systems adds complexity and potential costs to the ejector setup.
Noise Levels
While vacuum ejectors typically operate quietly compared to mechanical pumps, certain models can produce noticeable noise levels in specific settings. When noise control is a priority, selecting low-noise options or adding sound dampening measures may be necessary.
Energy Consumption
While generally energy-efficient, the overall energy consumption depends on the specific application and operating conditions. In processes where continuous operation is necessary, assess whether the ejector is the most energy-efficient solution compared to alternatives like rotary vane pumps.
Limited Application Range
Ejectors excel in applications with compatible materials but struggle in scenarios involving volatile or corrosive substances. Evaluating the material compatibility of your specific application can guide whether a vacuum ejector meets your needs.
Assessing these limitations before implementing vacuum ejectors can help you better understand their role in your processes and ensure that you select the right technology for your requirements.
Conclusion
Vacuum ejectors are a great choice for many industrial applications thanks to their efficiency and versatility. While they offer several advantages like cost savings and eco-friendliness, it’s important to keep their limitations in mind. By understanding how they work and where they excel or fall short, you can make informed decisions that best suit your needs. Whether you’re using them for packaging or material handling, knowing the ins and outs will help you get the most out of your vacuum ejector system.
Frequently Asked Questions
What are vacuum ejectors used for?
Vacuum ejectors are used in various industries for creating a vacuum or suction. They are commonly employed in packaging, material handling, and chemical processing to move or hold items without physical contact. Their versatility makes them suitable for many applications.
What are the benefits of using vacuum ejectors?
Vacuum ejectors offer several advantages, including cost-effectiveness, energy efficiency, and a reduced environmental impact. They’re generally simpler and easier to maintain than many other vacuum generation methods, making them a popular choice in industrial processes.
What are the limitations of vacuum ejectors?
Despite their benefits, vacuum ejectors have limitations. They struggle to achieve very low vacuum levels, lose efficiency at high flow rates, and rely on the quality of the motive fluid. Additionally, they can be noisy and may consume variable amounts of energy.
How do I choose the right vacuum ejector for my application?
Choosing the right vacuum ejector involves considering the required vacuum level, flow rate, and application specifics. Evaluate the ejector’s performance concerning your needs, and account for factors such as noise levels, energy consumption, and the quality of the motive fluid used.
Are vacuum ejectors energy efficient?
Yes, vacuum ejectors are considered energy efficient for many applications. They can generate a vacuum without needing large energy inputs. However, performance can vary based on design and the efficiency of the motive fluid used. Understanding these factors can help optimize their energy use.
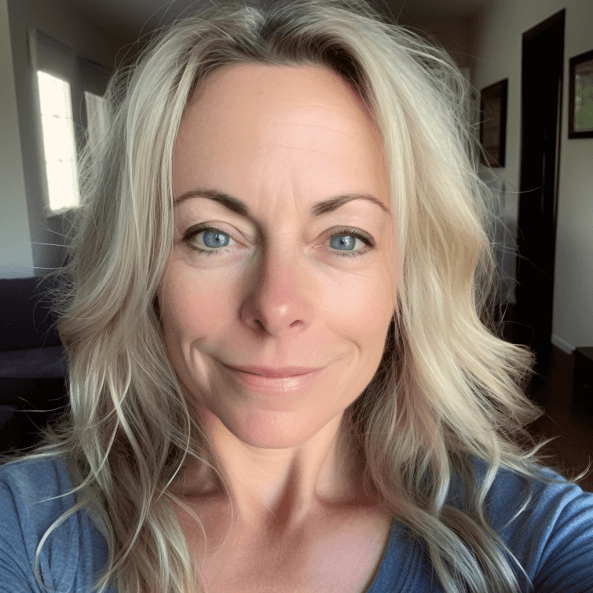