Have you ever found yourself needing a vacuum pump but only have an air compressor lying around? You’re not alone. Many DIY enthusiasts and professionals face this dilemma, especially when working on projects that require suction for tasks like woodworking or automotive repairs.
Key Takeaways
- Understanding Functions: Air compressors and vacuum pumps have opposite functions—compressors push air out, while vacuum pumps draw air in; knowing this is crucial for conversion.
- Essential Tools: Gather necessary tools and materials such as wrenches, screwdrivers, vacuum hoses, and rubber gaskets to ensure a smooth conversion process.
- Step-by-Step Guide: Follow a systematic approach, including disconnecting power, modifying components, and sealing connections to effectively convert an air compressor into a vacuum pump.
- Optimal Performance Tips: Ensure all connections are airtight, monitor the vacuum gauge, and perform regular maintenance on the air compressor to extend its life and improve efficacy.
- Regular Inspections: Periodically check for wear and replace damaged components to maintain efficient operation of your converted vacuum pump.
Understanding Air Compressors and Vacuum Pumps
Air compressors and vacuum pumps serve vital roles in various applications. Though they perform opposite functions, understanding their mechanisms helps when converting an air compressor to a vacuum pump.
Air Compressors
Air compressors convert power into kinetic energy. They draw in air and compress it, increasing pressure. This process allows compressed air to be stored for powering tools, inflating tires, and more. Common types include:
- Reciprocating Compressors: Use pistons to compress air.
- Rotary Screw Compressors: Use two rotating helical screws for continuous air flow.
- Centrifugal Compressors: Utilize a rotating disc to increase air pressure.
Vacuum Pumps
Vacuum pumps create a vacuum by removing air or gas from a sealed environment. They find use in many applications, such as:
- Medical Equipment: Essential for suction devices in surgeries.
- Manufacturing: Necessary for processes like material handling and packaging.
- Research Labs: Utilized in experiments requiring controlled atmospheric conditions.
Key Differences
The key differences between air compressors and vacuum pumps lie in their operations:
- Airflow Direction: Air compressors push air out while vacuum pumps draw air in.
- Pressure vs. Vacuum: Compressors generate high pressure; vacuum pumps create low pressure.
- Applications: Compressors suit pneumatic tools, while pumps target suction needs.
Practical Considerations
When considering the conversion from an air compressor to a vacuum pump, remember:
- Compatibility: Ensure the compressor’s motor can handle the changes.
- Attachment: Use appropriate fittings and hoses to create a seal for the vacuum.
- Modifications: Be ready for potential modifications to the compressor’s mechanism.
Understanding these components helps simplify the conversion process and makes your tasks more efficient.
Tools and Materials Needed
To convert an air compressor to a vacuum pump, specific tools and materials are necessary to ensure a successful and efficient process.
Essential Tools
- Wrenches: Use adjustable and socket wrenches for loosening and tightening various fittings.
- Screwdrivers: Keep Phillips and flat-head screwdrivers on hand for removing and securing screws.
- Pliers: Needle-nose and regular pliers help grip small parts.
- Hose Clamps: Use clamps to secure vacuum hoses and ensure airtight seals.
- Rubber Gaskets: Utilize gaskets that fit your compressor model to prevent air leaks.
- Vacuum Gauge: Attach a vacuum gauge to monitor pressure levels during operation.
- Vacuum Hose: Acquire a suitable vacuum hose that fits both the air compressor and the intended application. Ensure the diameter matches your connections.
- Connector Fittings: Obtain fittings that allow a seamless connection between the compressor and vacuum hose.
- Sealant: Use pipe sealant or Teflon tape to secure threaded connections and eliminate leaks.
- Filters: Install appropriate filters to protect the compressor from dust and debris during operation.
- Oil: If your compressor uses oil, ensure you have the right type for lubrication during vacuum operation.
By gathering these tools and materials, you set the foundation for a successful air compressor to vacuum pump conversion.
Step-by-Step Conversion Process
Converting your air compressor to a vacuum pump requires careful planning and execution. Follow these steps to ensure a successful transformation.
Preparing the Air Compressor
- Disconnect Power: Unplug your air compressor to eliminate any risk during the conversion process.
- Drain Air Tank: Open the drain valve at the bottom of the tank to remove any residual air. This ensures you start with a clean slate.
- Clear the Work Area: Organize your workspace. Make sure that your tools and materials are within reach to avoid unnecessary interruptions.
Modifying the Components
- Remove the Air Filter: Unscrew and detach the air filter for easier access to the internal components.
- Install Rubber Gasket: Apply a rubber gasket to the existing compressor head. This fills gaps, preventing air leaks during vacuum operation.
- Connect Vacuum Hose: Use connector fittings to attach the vacuum hose to the compressor’s discharge port. Ensure a snug fit to prevent air loss.
- Seal the Connections: Use sealant to secure all connections. This step ensures a tight seal, optimizing vacuum performance.
- Attach the Filter: Install a vacuum filter to the hose. This protects the internal components from debris while functioning as a vacuum pump.
- Plug in and Power On: Reconnect the power supply and turn on the air compressor. Watch for unusual sounds or vibrations that may indicate a problem.
- Check the Vacuum Gauge: Observe the vacuum gauge while the compressor operates. Verify that it’s creating the necessary vacuum pressure for your application.
- Evaluate Performance: Test the vacuum pump with a few practical tasks. Monitor the effectiveness in creating a vacuum and make adjustments as necessary.
- Inspect for Leaks: After testing, inspect all connections for air leaks. Tighten or reseal any areas showing signs of leakage.
These steps guide you through the conversion, ensuring your air compressor effectively functions as a vacuum pump.
Tips for Optimal Performance
- Use the Right Hose
Choose a vacuum hose that matches your needs. A flexible, durable hose enhances suction and minimizes leaks. - Seal All Connections
Ensure all connections between the air compressor and the vacuum hose are airtight. Use clamps or sealant to prevent air leaks and maintain optimal performance. - Check the Vacuum Gauge
Monitor the vacuum gauge regularly while in operation. A steady reading indicates efficient performance. If the gauge fluctuates, investigate for potential leaks or blockages. - Maintain the Air Compressor
Keep the air compressor well-maintained. Regularly check oil levels, clean filters, and drain moisture from the tank. Proper maintenance extends the lifespan and functionality of your setup. - Limit Runtime
Avoid prolonged use of the compressor as a vacuum pump. It may overheat, damaging internal components. Use it in short intervals, allowing it to cool down between uses. - Consider an In-Line Filter
Install an in-line filter to prevent debris from entering the vacuum pump. This step protects the motor and enhances performance over time. - Keep the Work Area Clean
Maintaining a clean work area minimizes the chance of clogging or damage. Regularly remove dust and debris to ensure efficient operation. - Test Before Full Use
Conduct a small test run to identify any potential issues. Test the setup with lighter tasks before moving on to heavier applications. - Utilize a Pressure Regulator
Use a pressure regulator to manage the vacuum pressure effectively. This tool helps maintain consistent performance, especially during varied tasks. - Regularly Inspect for Wear
Periodically check all components for signs of wear or damage. Replace any worn parts promptly to avoid performance drops or failures.
Conclusion
Transforming your air compressor into a vacuum pump can be a game changer for your projects. With the right adjustments and careful attention to detail you can achieve efficient performance that meets your needs.
Remember to maintain your setup regularly and keep an eye on all connections and components. This’ll help you get the most out of your conversion while ensuring safety and reliability.
Enjoy the versatility this new tool brings to your workspace and don’t hesitate to experiment with different applications. You’ve taken a great step toward maximizing your equipment’s potential!
Frequently Asked Questions
Can an air compressor be converted into a vacuum pump?
Yes, an air compressor can be converted into a vacuum pump for specific applications. However, it requires careful adjustments and some additional equipment to ensure efficient operation.
What is the main difference between an air compressor and a vacuum pump?
The primary difference lies in airflow direction and pressure generation. An air compressor compresses air to generate pressure, while a vacuum pump removes air to create a vacuum by reducing pressure.
What performance tips should I follow after converting an air compressor?
For optimal performance, use the right hose, seal all connections, check the vacuum gauge, maintain the air compressor, limit runtime, keep the work area clean, and regularly inspect for wear.
How can I ensure the longevity of my converted air compressor?
To extend the lifespan, use a pressure regulator, test before full use, and consider adding an in-line filter. Regular maintenance checks are also crucial for long-term efficiency.
What applications benefit from using a vacuum pump?
Vacuum pumps are commonly used in applications like refrigeration, packaging, and vacuum forming. Converting an air compressor can be beneficial for DIY projects in these fields.
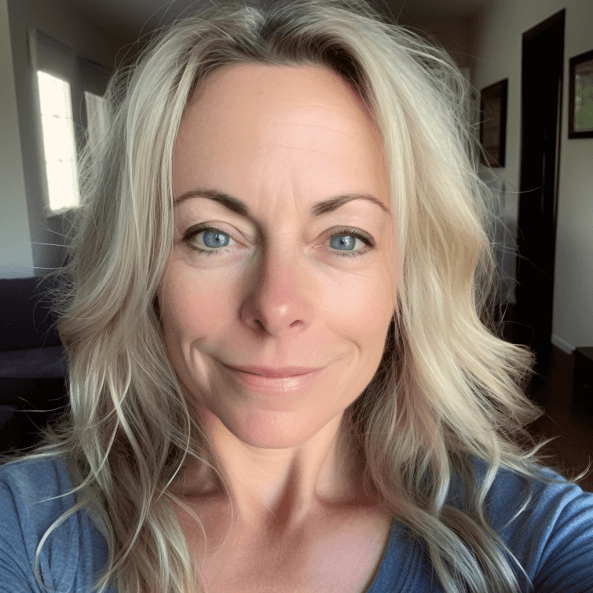