Dyson V11 Origin Cordless Vacuum, Nickel/Blue
- Versatile and cordless for whole-home deep cleaning.
Shark NV752 Rotator Powered Lift-Away TruePet Upright Vacuum with HEPA Filter, Large Dust Cup Capacity, LED Headlights, Upholstery Tool, Perfect Pet Power Brush & Crevice Tool, Bordeaux
- 2-IN-1 POWERED LIFT-AWAY TECHNOLOGY: Allows you to lift the pod away to deep-clean hard-to-reach areas, like under furniture, while the powered brushroll keeps spinning.
O-Cedar EasyWring Microfiber Spin Mop, Bucket Floor Cleaning System, Red, Gray, Standard
- HANDS-FREE WRINGING: Our exclusive mop bucket design features a built-in wringer that allows for hands-free wringing while Splash Guard keeps water splash and spray inside the bucket when wringing or when transporting the bucket from room to room
Electric Spin Scrubber for Cleaning Bathroom: Cordless Power Shower Scrubber - Electric Cleaning Brush for Tile Tub
- Multi-Surface Efficiency: Experience a deep clean across various surfaces with our Electric Spin Scrubber. Perfect for tiles, windows, bathtubs, toilets, and kitchen sinks. Effortlessly tackle dirt and grime where you need it most.
AIDEA Microfiber Cleaning Cloths, 50PK, Microfiber Towels for Cars, Premium All Purpose Car Cloth, Dusting Cloth Cleaning Rags, Absorbent Towels for SUVs, House, Kitchen, Window, 12"×12"
- Super Absorbent: Experience the excellent quality of AIDEA all-purpose microfiber cleaning cloths; made from 87% polyester and 13% polyamide; offering exceptional absorbency and quickly wicking away water to keep you dry; ideal for swiftly and safely removing dirt, grime, and liquids
Have you ever struggled with achieving a smooth, professional finish on your composite projects? You’re not alone. Many DIY enthusiasts and professionals face challenges when it comes to properly vacuum bagging composites, leading to less-than-ideal results.
Key Takeaways
- Understanding Vacuum Bagging: This technique removes air gaps from composite materials, resulting in a denser and stronger finished product.
- Benefits: Vacuum bagging provides an improved surface finish, enhanced fiber alignment, reduced weight, better compaction, and less material waste.
- Essential Materials: Key items include vacuum bagging film, a vacuum pump, sealant tape, release fabric, breather fabric, and the appropriate composite materials and resin system.
- Step-by-Step Process: Follow precise steps for preparing the composite layup, setting up the vacuum bag, and ensuring thorough curing for optimal results.
- Common Mistakes: Avoid poor layup techniques and inadequate sealing to enhance the effectiveness and quality of your vacuum bagging process.
Understanding Vacuum Bagging
Vacuum bagging is a technique used to enhance the quality and finish of composite materials. It removes air gaps, ensuring a denser, stronger product.
What Is Vacuum Bagging?
Vacuum bagging involves placing composite materials within a sealed bag and using a vacuum pump to extract air. This process compresses the materials, allowing resin to flow evenly around the fibers. You’ll typically find this method in aerospace, automotive, and marine applications. The main goal is to achieve a consistent pressure that aids in the curing process.
Benefits of Vacuum Bagging Composites
Vacuum bagging offers several advantages for composite projects. Here are key benefits:





- Improved Surface Finish: It reduces surface imperfections, giving you a smoother finish.
- Enhanced Fiber Alignment: It ensures fibers stay aligned, promoting optimal strength and durability.
- Reduced Weight: By minimizing excess resin, it lowers the overall weight of the finished product.
- Better Compaction: It applies uniform pressure during curing, resulting in fewer voids and better structural integrity.
- Less Material Waste: It allows for precise resin application, conserving materials and lowering costs.
Using vacuum bagging can significantly impact the quality of your composite projects. Consider this method for achieving professional-level results.
Materials Required for Vacuum Bagging
Vacuum bagging requires specific materials and tools to ensure effective results. Gather the following items to get started.
Types of Composites
Composites used in vacuum bagging come in various forms. Familiarize yourself with these common types:
- Fiberglass Composites: Lightweight and strong, these composites work well for many DIY projects.
- Carbon Fiber Composites: Known for their superior strength-to-weight ratio, carbon fiber composites are ideal for high-performance applications.
- Aramid Fiber Composites: These composites offer excellent impact resistance and are often used in aerospace and automotive industries.
- Natural Fiber Composites: Made from renewable resources, these composites provide an eco-friendly option for certain applications.
Necessary Tools and Equipment
The right tools and equipment ensure a smooth vacuum bagging process. Here’s what you’ll need:
- Vacuum Bagging Film: Select high-quality film that can withstand the vacuum pressure without tearing.
- Vacuum Pump: An efficient pump removes air from the bag, creating the necessary pressure for proper compaction.
- Sealant Tape: Use this to create airtight seals around the edges of the vacuum bag.
- Release Fabric: This prevents the composite from sticking to the bag and allows for easy removal.
- Breather Fabric: Place this inside the bag to promote even airflow and improve resin distribution.
- Composite Material: Choose the appropriate fiber reinforcement material for your project, such as fiberglass or carbon fiber.
- Resin System: Select a resin suitable for your composite type, like epoxy or polyester resin, ensuring it adheres well.
By preparing these materials and tools, you can optimize your vacuum bagging experience and achieve professional-grade results in your composite projects.
Step-by-Step Guide on How to Vacuum Bag Composites
Vacuum bagging composites requires precise steps for optimal results. Follow these guidelines to achieve a professional finish.
Preparing the Composite Layup
- Gather Materials: Collect all necessary materials, including composite fabric, resin system, and release film.
- Cut Composite Layers: Trim your composite materials to the desired shape and size, allowing for overlap where needed.
- Layering: Lay the composite fibers in a sequence, ensuring each layer has the right orientation for strength.
- Apply Resin: Use a brush or roller to evenly apply resin to the layers. Ensure saturation without excess drainage.
- Add Release Fabric: Place a release fabric on top of the composite layers to prevent them from sticking to the bag.
Setting Up the Vacuum Bag
- Choose the Right Bag: Select a vacuum bag that fits the size of your composite layup. Ensure it is compatible with the materials used.
- Position the Layup: Center the prepared layup within the vacuum bag. Leave room around the edges for sealing.
- Seal the Edges: Use sealant tape to create a tight seal around the bag edges. Ensure no gaps exist for air leaks.
- Insert Breather Fabric: Place breather fabric on top of the layup before sealing the bag. This allows for airflow and helps eliminate trapped air.
- Connect to the Vacuum Pump: Attach the vacuum line to the bag’s port. Make sure it connects securely.
- Start the Vacuum: Turn on the vacuum pump. Monitor the pressure gauge to ensure it reaches the recommended vacuum level.
- Check for Leaks: Inspect the sealed edges for air leaks. If detected, reapply sealant tape as necessary.
- Cure the Composites: Allow the resin to cure as per the manufacturer’s instructions. This usually involves maintaining the vacuum for a specific duration.
- Remove the Bag: Once cured, carefully open the bag and remove the composite. Trim any excess edges for a clean finish.
By following these steps, you can effectively vacuum bag composites and achieve high-quality results.
Common Mistakes to Avoid
Avoiding common mistakes can significantly improve your vacuum bagging process. Focus on these key areas to ensure success.
Incorrect Layup Techniques
Incorrect layup techniques can compromise the quality of your composite. Always ensure even fiber alignment to prevent weak spots. Use proper layering methods for reinforcement. For instance, alternate the direction of fibers in successive layers to enhance strength. Additionally, check for air bubbles as you lay up the material, as these can create voids in the final product.
Inadequate Vacuum Sealing
Inadequate vacuum sealing leads to air leaks, reducing the effectiveness of the vacuum bagging process. Employ high-quality sealing tape for better adhesion. Ensure all edges are sealed tightly, especially around corners and overlaps. Inspect the bag for visible gaps before activating the vacuum pump. If leaks occur, the infusion won’t be uniform. Conduct a leak test with low vacuum pressure before proceeding to full vacuum to confirm all seals are intact.
Conclusion
Vacuum bagging composites can feel daunting at first but with the right tools and techniques you can create impressive results. By carefully following the steps and avoiding common pitfalls you’ll set yourself up for success.
Remember to take your time during preparation and ensure everything’s sealed properly. This attention to detail will pay off in the quality of your finished product.
So gear up and dive into your next composite project with confidence. You’re well on your way to mastering the art of vacuum bagging and achieving those professional finishes you’ve been aiming for. Happy crafting!
Frequently Asked Questions
What is vacuum bagging in composite projects?
Vacuum bagging is a technique used in composite projects to remove air from the layup and compact the materials, ensuring a stronger bond and better finish.
What materials are needed for vacuum bagging?
Key materials for vacuum bagging include vacuum bagging film, a vacuum pump, sealant tape, and the composite materials you are working with, such as fiberglass or carbon fiber.
How do I prepare for vacuum bagging?
Start by preparing the composite layup, ensuring all layers are in place without gaps. Make sure the work area is clean and ready for the vacuum bagging process.
What are the steps to vacuum bag composites?
- Prepare the composite layup.
- Cut and lay out the vacuum bagging film.
- Seal the edges with tape to prevent air leaks.
- Connect the bag to the vacuum pump.
- Begin the vacuum process and cure the composites.
What common mistakes should I avoid during vacuum bagging?
Avoid improper layup techniques, which can weaken the composite, and ensure to check for adequate vacuum sealing to prevent air leaks. Also, don’t rush the curing process; let it complete fully for the best results.
How can I ensure a proper vacuum seal?
Ensure all edges of the vacuum bag are securely sealed with quality sealant tape. Test the seal by creating a slight vacuum before starting the curing process to identify any leaks.
How long does the curing process take after vacuum bagging?
Curing times vary depending on the type of resin used and environmental conditions. Always refer to your resin manufacturer’s guidelines for accurate curing times.
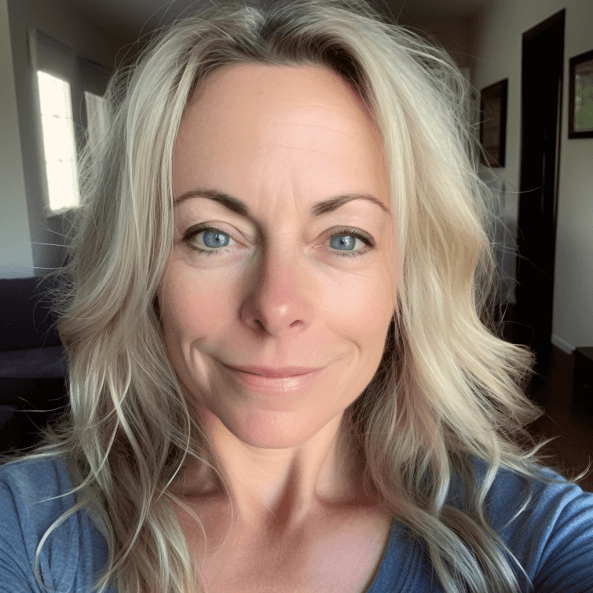