Have you ever struggled with achieving a flawless finish on your carbon fiber projects? If you’re working with this lightweight material, you know that proper vacuum bagging is crucial for eliminating air pockets and ensuring a strong, durable bond.
In this article, you’ll learn step-by-step how to vacuum bag carbon fiber like a pro. Whether you’re a seasoned builder or just starting out, mastering this technique will elevate your work and help you avoid common pitfalls. Get ready to enhance your skills and produce high-quality results that stand the test of time.
Key Takeaways
- Understand Vacuum Bagging: Familiarize yourself with vacuum bagging for carbon fiber to ensure a strong, durable bond and eliminate air pockets.
- Gather Essential Materials: Having the right tools, such as a vacuum pump, vacuum bagging film, and breather fabric, is crucial for effective vacuum bagging.
- Follow a Step-By-Step Process: Carefully prepare the workspace, lay out carbon fiber, seal the vacuum bag, and apply vacuum pressure for optimal results.
- Avoid Common Mistakes: Implement proper sealing techniques and choose compatible materials to prevent air leaks and ensure high quality in your carbon fiber projects.
- Enjoy the Benefits: Vacuum bagging enhances bonding, reduces excess resin, improves surface finish, and increases precision in carbon fiber manufacturing.
Understanding Vacuum Bagging
Vacuum bagging is a technique that enhances the manufacturing process of carbon fiber projects. It creates a strong and uniform bond between layers of material while removing excess resin and air pockets. Understanding this method is crucial for achieving a high-quality finish.
What Is Vacuum Bagging?
Vacuum bagging involves enclosing your carbon fiber layup in a bag and removing air to create a vacuum seal. You place the layup on a flat surface, cover it with a flexible plastic bag, and connect a vacuum pump to extract air. This process compresses the material, ensuring full contact and better adhesion between layers. You’ll need a vacuum gauge to monitor the pressure and ensure an effective seal.
Benefits of Vacuum Bagging Carbon Fiber
Vacuum bagging offers several advantages when working with carbon fiber:
- Eliminates Air Pockets: The vacuum process removes trapped air, preventing weak spots in your composite structure.
- Enhances Bonding: A tighter seal promotes better resin distribution and can improve the overall strength and durability of the final product.
- Reduces Excess Resin: By pulling the bag tight, excess resin gets removed, resulting in lighter and stronger components.
- Improves Surface Finish: The compression helps maintain a smooth surface, reducing the need for extensive finishing work.
- Increases Precision: Consistent pressure leads to more uniform thickness throughout the layup, providing predictable performance.
Overall, vacuum bagging is essential for anyone looking to create high-quality carbon fiber products.
Materials Needed for Vacuum Bagging
Vacuum bagging carbon fiber requires specific materials for successful results. Using the right supplies ensures a smooth process and a high-quality finish.
Essential Tools and Equipment
- Vacuum Pump: A reliable vacuum pump removes air from the bag to create a vacuum, essential for proper compression.
- Vacuum Bagging Film: This plastic film creates an air-tight seal around your carbon fiber laminate. Choose films made for high temperatures and strong vacuums.
- Vacuum Sealant Tape: Use this tape to seal any openings and joints in your vacuum bag. It holds everything in place and prevents leaks.
- Breather Fabric: This material allows air to flow through the laminate while still keeping it compressed. It helps in achieving an even vacuum across the surface.
- Release Agent: Apply a release agent to your mold or surface to prevent adhesion between the laminate and the mold. This allows for easier demolding once the process is complete.
- Woven Fabric Scrim: Enhances the strength of your vacuum bag and helps distribute pressure evenly across the carbon fiber layers.
- Pre-Preg Carbon Fiber: This type of carbon fiber has resin already infused into the fibers. It’s commonly used in vacuum bagging due to its excellent strength and finish.
- Wet Layup Carbon Fiber: In this method, you manually apply resin to the fabric layers. It allows for more control over the resin content but requires careful management during vacuum bagging.
- Fabric and Mat Combinations: Combining woven fabrics with non-woven mats enhances strength and stability. These combinations work well for complex shapes and improve overall durability.
Understanding these materials and tools enables effective vacuum bagging, leading to high-quality carbon fiber products.
Step-By-Step Guide on How to Vacuum Bag Carbon Fiber
Follow these steps to effectively vacuum bag carbon fiber and achieve optimal results. Each stage plays a vital role in ensuring a successful process.
Preparing the Workspace
Clear and organize your workspace. Gather all essential materials including vacuum pump, vacuum bagging film, vacuum sealant tape, breather fabric, and release agent. Ensure surfaces are clean and free from dust. Good ventilation helps to manage fumes from resin. Layout the tools within easy reach to avoid interruptions.
Laying Out the Carbon Fiber
Lay the carbon fiber sheets flat on a clean surface. Ensure they are free from wrinkles and creases. Cut the carbon fiber to size based on your mold or project specifications. If using pre-preg carbon fiber, handle it quickly to maintain its properties. Apply a release agent to the mold surface to ease demolding later.
Sealing the Vacuum Bag
Cut the vacuum bagging film to a suitable size, allowing for ample overlap on all sides. Place the carbon fiber assembly inside the bag. Use vacuum sealant tape to seal the edges of the bag securely. Ensure there are no gaps in the sealing, as leaks can cause loss of vacuum pressure and affect the final result.
Applying Vacuum Pressure
Connect the vacuum pump to the bag’s vacuum port. Start the pump to remove air from the bag. Monitor the pressure gauge for consistent readings. Adjust the bag if necessary to ensure it conforms tightly around the carbon fiber without excessive pressure that might damage it. Allow the vacuum to stabilize, ensuring the carbon fiber layers bond properly.
These steps provide a clear process for vacuum bagging carbon fiber, ensuring all essential actions are taken to achieve a quality finish.
Common Mistakes to Avoid
Avoiding common mistakes during the vacuum bagging process helps ensure a successful carbon fiber project. Here are some critical pitfalls to sidestep:
Inadequate Sealing Techniques
Ensure you seal the vacuum bag properly to prevent leaks. Use high-quality vacuum sealant tape around the edges. Double-check your seals after placement. If the bag isn’t sealed well, vacuum pressure drops, leading to air pockets. Conduct leak tests before starting the vacuum process. Listen for hissing sounds that may indicate a leak. Taking these precautions will prevent wasted materials and time.
Incorrect Material Usage
Choose the right materials for vacuum bagging. Using incompatible resins or films can compromise quality. For instance, ensure the vacuum bagging film can withstand the vacuum pressure required. Using untested or unsuitable carbon fiber can also lead to delamination. Always refer to manufacturer guidelines when selecting materials. This attention to detail minimizes the risk of issues and enhances the overall quality of your finished product.
Conclusion
Proper vacuum bagging is key to achieving that perfect carbon fiber finish you’re aiming for. By following the steps outlined and using the right materials, you’ll set yourself up for success. Remember to keep an eye out for common pitfalls and always test for leaks.
With a little practice and attention to detail, you’ll be creating strong and flawless carbon fiber pieces in no time. Enjoy the process and take pride in your craftsmanship as you master the art of vacuum bagging. Happy crafting!
Frequently Asked Questions
What is vacuum bagging in carbon fiber projects?
Vacuum bagging is a process used in carbon fiber projects to eliminate air pockets and ensure a strong bond between layers of material. By applying vacuum pressure, it enhances bonding, reduces excess resin, and improves the overall finish of the composite.
Why is vacuum bagging important?
Vacuum bagging is crucial because it helps achieve a flawless finish in carbon fiber projects. It eliminates air pockets that can weaken the structure and ensures a tight bond between layers, resulting in a stronger and more durable product.
What materials are needed for vacuum bagging?
Essential materials for vacuum bagging include a vacuum pump, vacuum bagging film, and a release agent. These components work together to create a vacuum environment that improves the quality and strength of the finished carbon fiber product.
How do you perform vacuum bagging on carbon fiber?
To perform vacuum bagging, prepare your carbon fiber layup, apply the release agent, cover it with vacuum bagging film, and use the vacuum pump to create a vacuum. Ensure proper sealing and perform leak tests to maintain quality throughout the process.
What common mistakes should be avoided in vacuum bagging?
Common mistakes include inadequate sealing techniques, using incorrect materials, and neglecting to perform leak tests. Avoiding these errors is crucial for ensuring a strong bond and high-quality finish in carbon fiber projects.
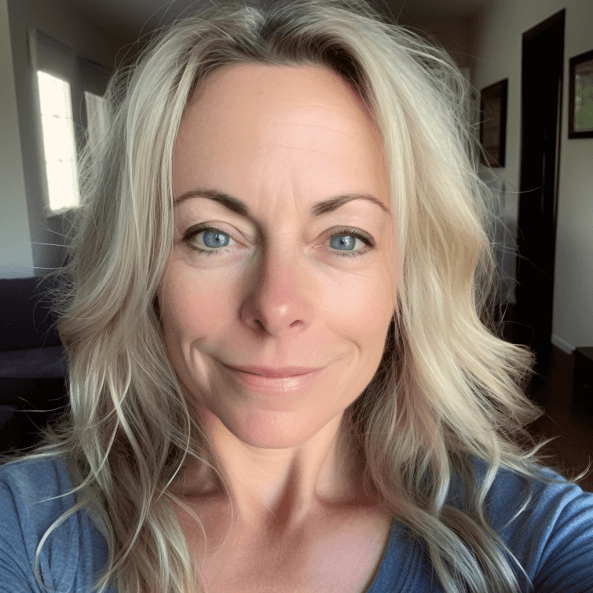