Have you ever wondered how manufacturers create high-quality materials without the risk of contamination? A vacuum furnace might just be the answer. This specialized equipment plays a crucial role in industries like aerospace and automotive, where precision is key.
Imagine needing to heat metal to extreme temperatures while keeping it free from any unwanted gases or impurities. That’s exactly what a vacuum furnace does. By removing air and creating a controlled environment, it allows for efficient processing of materials.
In this article, you’ll discover how vacuum furnaces operate and why they’re essential for producing reliable and durable components. You’ll gain insights into their benefits and applications, making it easier to understand their importance in modern manufacturing.
Key Takeaways
- Functionality of Vacuum Furnaces: Vacuum furnaces create a controlled atmosphere by removing air and gases, preventing oxidation and contamination during the heating process of metals and alloys.
- Core Components: Key components include the vacuum chamber, heating elements (resistance, induction, radiant), vacuum system for air removal, and control systems for regulating temperature and pressure.
- Applications Across Industries: Primarily used in aerospace for heat treatment of superalloys and titanium, and in medical equipment manufacturing for producing high-quality implants and surgical tools.
- Benefits of Vacuum Processing: Offers enhanced material properties, reduced oxidation risks, improved energy efficiency, and consistent quality control, crucial for meeting strict industry standards.
- Heating Methods: Various heating techniques such as resistance, induction, and radiant heating allow for precise processing tailored to specific materials.
- Importance in Manufacturing: Vacuum furnaces are vital for producing reliable, high-quality materials that are essential for various sectors, underscoring their role in modern manufacturing processes.
Overview of Vacuum Furnaces
Vacuum furnaces play a crucial role in the manufacturing process by providing a unique environment for material processing. A vacuum furnace operates by removing air and other gases from the chamber, creating a controlled atmosphere. This vacuum condition prevents oxidation and contamination, essential for producing high-quality materials such as metals and alloys.
Components of a Vacuum Furnace
- Vacuum Chamber: The primary component that houses the materials during processing.
- Heating Elements: Components that generate heat, usually made from alloys designed to withstand extreme conditions.
- Vacuum System: Includes pumps that evacuate air and gases, maintaining the vacuum environment.
- Control System: Regulates temperature, pressure, and other parameters to ensure optimal processing conditions.
Heating Methods
- Resistance Heating: Uses electric currents in heating elements to produce heat.
- Induction Heating: Employs electromagnetic fields to heat materials directly.
- Radiant Heating: Utilizes infrared radiation for uniform temperature distribution.
Applications of Vacuum Furnaces
- Heat Treatment: Strengthens metals without introducing contaminants.
- Sintering: Binds powder materials into solid forms with precise control over density and microstructure.
- Melting: Produces high-purity metals essential for aerospace and automotive industries.
- Reduced Oxidation: The absence of air eliminates oxidation risks during processing.
- Enhanced Quality: Achieves superior material properties with minimal impurities.
- Energy Efficiency: Well-insulated designs lead to lower energy consumption compared to conventional furnaces.
Understanding these aspects provides valuable insight into how vacuum furnaces function and why they are vital in manufacturing high-quality, durable materials. Their applications across various industries highlight their importance in producing reliable components that meet stringent standards.
Principles of Operation
Vacuum furnaces operate by creating a controlled environment that eliminates air and contaminants. This method enhances material properties through precise temperature control and homogeneous heating.
Main Components
- Vacuum Chamber: The core structure where materials are processed. It maintains low-pressure conditions that prevent oxidation and contamination during heating.
- Heating Elements: Typically made of heat-resistant materials, these elements provide the necessary heat through methods like resistance or induction.
- Vacuum System: Includes pumps and gauges that create and monitor the vacuum level. It ensures that the internal atmosphere remains devoid of air and moisture.
- Control System: This system regulates temperature, pressure, and time settings. Advanced systems enable automated processes for efficiency and consistency.
- Resistance Heating: Electric current passes through a resistance element, generating heat. This method is efficient for sintering and heat treatment.
- Induction Heating: Magnetic fields induce electric currents in the workpiece, leading to rapid heating. It’s suitable for metals and alloys requiring fast processing.
- Radiant Heating: Infrared radiation heats the workpiece surface directly. This method is often used for preheating before further processing.
These components and heating methods work collectively to optimize the vacuum furnace’s performance, ensuring the production of high-quality materials essential for various industries.
Advantages of Using a Vacuum Furnace
Vacuum furnaces offer several key advantages that enhance manufacturing processes. They create a controlled environment that eliminates air and contamination, leading to superior material properties.
Quality Control
Quality control is critical in manufacturing. Vacuum furnaces ensure that materials undergo uniform heat treatment. Even temperatures prevent defects like warping or cracking. They also minimize oxidation, which is vital for reactive materials such as titanium or zirconium. Consistent results lead to higher-quality end products, allowing you to maintain strict compliance with industry standards.
Energy Efficiency
Energy efficiency stands out as a primary benefit of vacuum furnaces. These systems typically operate at lower temperatures than conventional furnaces, reducing energy consumption. They utilize efficient heating methods like induction or resistance, which target specific areas, optimizing heat distribution. By minimizing heat loss, vacuum furnaces save energy and lower operational costs.
Applications of Vacuum Furnaces
Vacuum furnaces play a crucial role in several industries by enabling precise processing of materials. They ensure high standards in manufacturing through controlled environments that enhance material properties.
Aerospace Industry
In the aerospace industry, vacuum furnaces facilitate the production of lightweight yet strong components. They’re essential for heat treatment of titanium alloys and superalloys used in aircraft engines and frames. Processes like sintering and melting in a vacuum prevent oxidation, ensuring structural integrity and performance under extreme conditions. For example, turbine blades undergo stringent treatments in vacuum furnaces to improve their fatigue resistance and thermal stability.
Medical Equipment
Medical equipment manufacturing benefits significantly from vacuum furnaces. These furnaces are pivotal in producing high-quality implants, surgical instruments, and diagnostic devices. The vacuum environment ensures the purity of materials, reducing the risk of contamination. For instance, titanium implants, known for their biocompatibility, often undergo vacuum heat treatment to achieve the desired mechanical properties while preventing oxidation. This process is critical for ensuring safety and efficacy in medical applications.
Conclusion
Understanding how a vacuum furnace works opens up a world of possibilities in manufacturing. With its ability to create a controlled environment free from contaminants you can achieve high-quality materials that meet the demands of various industries. Whether you’re in aerospace or medical equipment production the benefits of using vacuum furnaces are clear. They not only enhance quality but also improve efficiency and reduce defects. As you explore the potential of vacuum furnaces you’ll see how they can elevate your manufacturing processes and contribute to the creation of innovative products.
Frequently Asked Questions
What are vacuum furnaces?
Vacuum furnaces are specialized heating devices that operate in a vacuum environment to process materials. They are used to heat-treat metals and alloys, sinter materials, and melt substances while eliminating air and contaminants, thereby enhancing the quality of the end product.
What are the benefits of using vacuum furnaces?
The main advantages of vacuum furnaces include improved quality control, prevention of defects, and energy efficiency. They provide a controlled atmosphere, which is essential for producing high-quality materials in industries such as aerospace, automotive, and medical equipment.
How do vacuum furnaces work?
Vacuum furnaces remove air to create a controlled environment, preventing oxidation and contamination during heating. They use various heating methods, such as resistance heating, induction heating, or radiant heating, to reach the desired temperatures for processes like heat treatment and sintering.
Which industries use vacuum furnaces?
Vacuum furnaces are vital in several industries, including aerospace, automotive, and medical equipment. They are particularly important for producing lightweight and strong components, ensuring material purity for implants and surgical instruments, and facilitating advanced manufacturing processes.
What materials can be processed in vacuum furnaces?
Vacuum furnaces can process a variety of materials, including high-performance alloys, titanium, superalloys, and ceramics. These materials benefit from vacuum treatment as it helps maintain their integrity and performance during manufacturing processes like melting, heat treatment, and sintering.
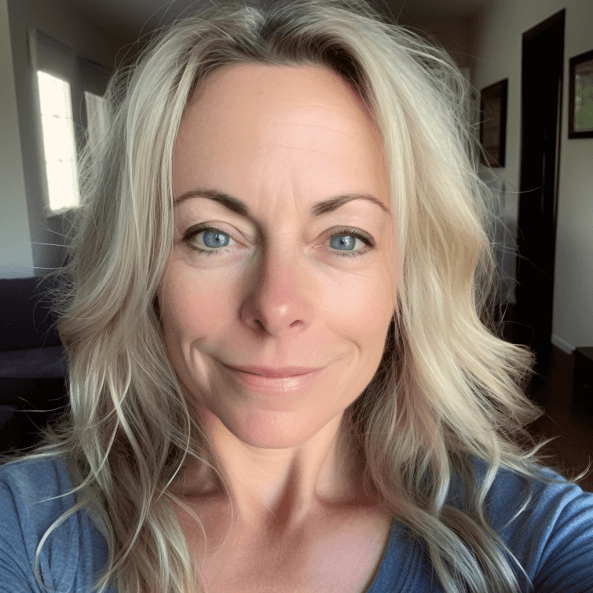