Dyson V11 Origin Cordless Vacuum, Nickel/Blue
- Versatile and cordless for whole-home deep cleaning.
Shark NV752 Rotator Powered Lift-Away TruePet Upright Vacuum with HEPA Filter, Large Dust Cup Capacity, LED Headlights, Upholstery Tool, Perfect Pet Power Brush & Crevice Tool, Bordeaux
- 2-IN-1 POWERED LIFT-AWAY TECHNOLOGY: Allows you to lift the pod away to deep-clean hard-to-reach areas, like under furniture, while the powered brushroll keeps spinning.
O-Cedar EasyWring Microfiber Spin Mop, Bucket Floor Cleaning System, Red, Gray, Standard
- HANDS-FREE WRINGING: Our exclusive mop bucket design features a built-in wringer that allows for hands-free wringing while Splash Guard keeps water splash and spray inside the bucket when wringing or when transporting the bucket from room to room
Electric Spin Scrubber for Cleaning Bathroom: Cordless Power Shower Scrubber - Electric Cleaning Brush for Tile Tub
- Multi-Surface Efficiency: Experience a deep clean across various surfaces with our Electric Spin Scrubber. Perfect for tiles, windows, bathtubs, toilets, and kitchen sinks. Effortlessly tackle dirt and grime where you need it most.
AIDEA Microfiber Cleaning Cloths, 50PK, Microfiber Towels for Cars, Premium All Purpose Car Cloth, Dusting Cloth Cleaning Rags, Absorbent Towels for SUVs, House, Kitchen, Window, 12"×12"
- Super Absorbent: Experience the excellent quality of AIDEA all-purpose microfiber cleaning cloths; made from 87% polyester and 13% polyamide; offering exceptional absorbency and quickly wicking away water to keep you dry; ideal for swiftly and safely removing dirt, grime, and liquids
Have you ever poured resin only to find bubbles ruining your perfect finish? You’re not alone. Many crafters face this frustrating challenge, but the good news is that you can minimize those pesky air pockets with the right vacuum levels.
Understanding how much vacuum to apply when degassing resin is key to achieving a flawless result. This article will guide you through the process, helping you figure out the ideal vacuum pressure and techniques to ensure your resin projects come out looking professional. With a few simple adjustments, you’ll be on your way to creating stunning pieces without the hassle of unwanted bubbles.
Key Takeaways
- Understand Vacuum Units: Familiarize yourself with common vacuum units such as inches of mercury (inHg), millibars (mbar), and pascals (Pa) to set the correct vacuum levels for resin degassing.
- Optimal Vacuum Pressure: Aim for a vacuum pressure between 25 and 28 inHg for epoxy and polyester resins, and between 22 and 26 inHg for silicone resins to effectively remove air bubbles.
- Adjust for Thickness and Temperature: Be mindful that thicker resins may require a higher vacuum level, and warmer temperatures can reduce viscosity, potentially allowing for lower vacuum settings.
- Choose the Right Equipment: Invest in quality vacuum pumps and chambers; rotary vane pumps and adequately sized vacuum chambers ensure efficient degassing.
- Follow Best Practices: Implement a thorough step-by-step degassing process and monitor the mixture closely to achieve a bubble-free finish, ensuring optimal resin quality.
- Troubleshoot Common Issues: If bubbles persist after degassing, adjust the vacuum level or re-evaluate your mixing and pouring techniques to enhance results.
Understanding Vacuum Levels
Using the correct vacuum levels ensures effective degassing of resin, preventing air bubbles that compromise your final product. This section dives into the importance of vacuum pressure and the units typically used in the process.
Importance of Vacuum in Degassing
Vacuuming removes air trapped in resin. As the vacuum level decreases, the pressure drops, allowing air bubbles to expand and rise to the surface. A suitable vacuum environment helps achieve complete degassing, resulting in a smooth, clear finish. For optimal results, aim for a vacuum pressure between 25 and 28 inches of mercury (inHg). This range maximizes bubble removal while keeping the resin’s properties intact.





Common Vacuum Units Used
Understanding vacuum units simplifies the degassing process. Here are common units you might encounter:
- Inches of Mercury (inHg): Commonly used in many degassing processes. A vacuum of 25 inHg or lower is typically effective.
- Millibars (mbar): Used in some countries, where 1 inHg equals about 33.86 mbar.
- Pascals (Pa): The SI unit for pressure. 1 inHg is roughly 3,386.39 Pa.
Knowing these units helps ensure you set the correct vacuum level based on your equipment specifications.
Recommended Vacuum Levels for Resin Degassing
Choosing the right vacuum level is essential for successful resin degassing. Proper vacuum pressure removes air bubbles, ensuring a smooth finish.
Vacuum Levels for Different Types of Resin
- Epoxy Resin: Use a vacuum level between 25 and 28 inHg. This range effectively pulls air out without compromising the resin structure.
- Polyester Resin: Target a vacuum level of about 24 inHg. Polyester resin typically requires slightly lower vacuum pressure, as it can be more sensitive to rapid bubble expansion.
- Silicone Resin: Aim for a vacuum level between 22 and 26 inHg. Different silicones may react differently, so adjusting according to the specific product is beneficial.
- Resin Thickness: Thicker resin may require a higher vacuum level to efficiently remove trapped air. Adjust your vacuum setting based on the viscosity of the resin.
- Temperature: Higher temperatures can reduce resin viscosity, allowing air bubbles to escape more easily. You might find that a lower vacuum level suffices in warmer conditions.
- Mixing Techniques: Agitated mixing can introduce more air. If you’re mixing vigorously, consider increasing the vacuum level to compensate for extra trapped bubbles.
- Equipment Quality: The efficiency of your vacuum pump also affects the vacuum level achievable. Ensure your equipment operates correctly for optimal results.
Equipment Needed for Effective Degassing
Choosing the right equipment is essential for successful resin degassing. You need specific tools to achieve optimal vacuum levels and prevent air bubbles effectively.
Vacuum Pumps
Vacuum pumps are crucial for creating a vacuum in the degassing process. Select a pump that reaches at least 25 inHg, suitable for various resins like epoxy and polyester. Consider these options:
- Rotary Vane Pumps: These pumps provide strong vacuum levels and are ideal for most resin projects. Look for models with a rating of at least 3-5 CFM (cubic feet per minute).
- Diaphragm Pumps: These pumps offer a quieter alternative with lower maintenance. They typically work well for smaller batches.
- Vacuum Pump Kits: Some kits come with necessary accessories, like oil and hoses, making setup easier.
Vacuum Chambers
Vacuum chambers allow you to place your resin mixes inside while the pump creates a vacuum. A good chamber ensures effective air removal. Key features include:
- Material: Consider chambers made of high-quality materials like thick acrylic or aluminum for durability.
- Size: Choose a chamber large enough to accommodate your resin container. A minimum volume of 2-5 gallons suits most projects.
- Clear Lid: A clear lid enables you to monitor the degassing process easily.
- Gauge: Ensure the chamber includes a vacuum gauge to track pressure levels accurately.
Using the right vacuum pump and chamber optimizes your degassing process, leading to professional-looking resin pieces.
Best Practices for Degassing Resin
Degassing resin properly helps you achieve a bubble-free finish. Follow these best practices to get optimal results.
Step-by-Step Degassing Process
- Prepare Your Equipment: Gather a vacuum pump and a vacuum chamber. Check that everything’s clean and in good condition.
- Mix the Resin Thoroughly: Combine resin and hardener according to the manufacturer’s instructions. Stir slowly to minimize air introduction.
- Pour the Mixture into the Chamber: Place the mixed resin in a vacuum chamber. Avoid overfilling to allow for bubble expansion.
- Apply Vacuum: Start the vacuum pump. Aim for a vacuum level between 25 to 29 inches of mercury (inHg). Monitor the gauge closely.
- Observe the Mixture: Watch for bubbles rising. Be patient; this can take several minutes. When bubbles stop forming, you’ll know the process is working.
- Release the Vacuum Slowly: Gradually return the chamber to normal pressure. This prevents rapid pressure changes, which can introduce new bubbles.
- Cure the Resin: Allow the resin to cure as per instructions. Keep it in a controlled environment for the best results.
- Bubbles Persist After Degassing: Increase the vacuum level to 29 inHg if bubbles remain. Consider extending the time spent in the vacuum.
- Resin Overflows: Avoid overfilling the chamber. Use smaller batches if necessary, and keep an eye on the mixture as it expands.
- Poor Vacuum Levels: Ensure all seals on the chamber are intact. Check that the pump operates correctly and the gauge is functioning.
- Uneven Curing: Maintain consistent temperature throughout the curing process. An environment that’s too cold or warm can affect results.
Implement these best practices for effective resin degassing, and you’ll enhance the quality of your projects significantly.
Conclusion
Getting the vacuum levels right is key to achieving that perfect resin finish you’re aiming for. By understanding the nuances of your specific resin and following best practices, you can significantly reduce air bubbles and enhance the overall quality of your projects.
Remember that patience is essential during the degassing process. Keep an eye on your setup and don’t hesitate to make adjustments as needed. With the right approach and equipment, you’ll be well on your way to creating stunning, bubble-free resin pieces that you can be proud of. Happy crafting!
Frequently Asked Questions
What are vacuum levels in resin projects?
Vacuum levels refer to the amount of air pressure removed from a resin mixture to prevent air bubbles when curing. Understanding vacuum levels is crucial for achieving a smooth and flawless finish in resin applications.
Why is degassing important in resin casting?
Degassing is essential because it removes dissolved air from the resin mixture, which can cause air bubbles, uneven curing, and a compromised final product. Proper degassing leads to a clearer and more polished finish.
What vacuum pressure should I use for different resin types?
The recommended vacuum pressure typically ranges between 25 to 29 inches of mercury. However, optimal pressure may vary based on the specific resin type and the project’s requirements, so checking the product guidelines is advised.
What equipment is needed for degassing resin?
You will need a quality vacuum pump, vacuum chamber, and possibly additional tools like mixing cups and spatulas. This equipment ensures thorough vacuum treatment to eliminate air bubbles during the resin curing process.
How can I prevent persistent bubbles in my resin?
To prevent persistent bubbles, ensure that you mix the resin thoroughly and apply vacuum within the recommended range. Additionally, maintaining proper temperature and using high-quality materials can significantly reduce bubble formation.
What common issues can arise during resin curing?
Common issues include persistent bubbles, resin overflows, poor vacuum levels, and uneven curing. Addressing these problems involves adjusting mixing techniques, vacuum pressure, and ensuring proper equipment is used throughout the process.
What are best practices for degassing resin?
Best practices include preparing all equipment beforehand, mixing resin thoroughly to avoid air pockets, applying the correct vacuum pressure, monitoring the degassing process, and allowing sufficient time for proper curing after degassing.
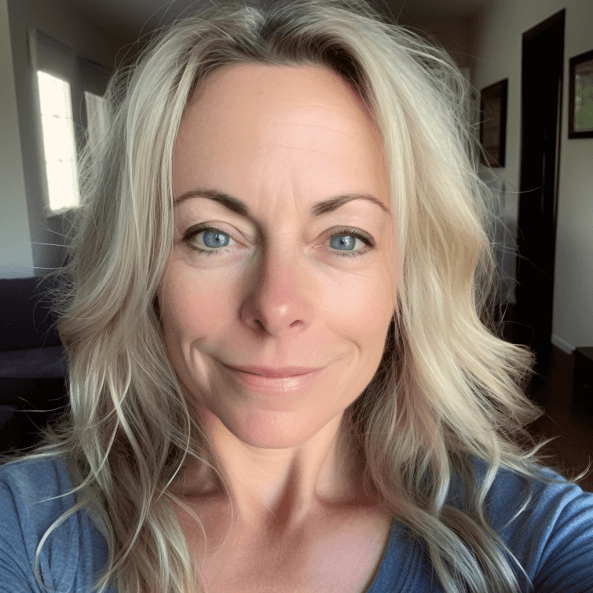