Dyson V11 Origin Cordless Vacuum, Nickel/Blue
- Versatile and cordless for whole-home deep cleaning.
Shark NV752 Rotator Powered Lift-Away TruePet Upright Vacuum with HEPA Filter, Large Dust Cup Capacity, LED Headlights, Upholstery Tool, Perfect Pet Power Brush & Crevice Tool, Bordeaux
- 2-IN-1 POWERED LIFT-AWAY TECHNOLOGY: Allows you to lift the pod away to deep-clean hard-to-reach areas, like under furniture, while the powered brushroll keeps spinning.
O-Cedar EasyWring Microfiber Spin Mop, Bucket Floor Cleaning System, Red, Gray, Standard
- HANDS-FREE WRINGING: Our exclusive mop bucket design features a built-in wringer that allows for hands-free wringing while Splash Guard keeps water splash and spray inside the bucket when wringing or when transporting the bucket from room to room
Electric Spin Scrubber for Cleaning Bathroom: Cordless Power Shower Scrubber - Electric Cleaning Brush for Tile Tub
- Multi-Surface Efficiency: Experience a deep clean across various surfaces with our Electric Spin Scrubber. Perfect for tiles, windows, bathtubs, toilets, and kitchen sinks. Effortlessly tackle dirt and grime where you need it most.
AIDEA Microfiber Cleaning Cloths, 50PK, Microfiber Towels for Cars, Premium All Purpose Car Cloth, Dusting Cloth Cleaning Rags, Absorbent Towels for SUVs, House, Kitchen, Window, 12"×12"
- Super Absorbent: Experience the excellent quality of AIDEA all-purpose microfiber cleaning cloths; made from 87% polyester and 13% polyamide; offering exceptional absorbency and quickly wicking away water to keep you dry; ideal for swiftly and safely removing dirt, grime, and liquids
Have you ever wanted to create custom shapes or prototypes but felt limited by the tools at your disposal? Building a vacuum former might be the solution you need. This handy device allows you to mold plastic into unique designs, opening up a world of creativity for your projects.
In this article, you’ll learn how to construct your own vacuum former from scratch. Whether you’re a hobbyist looking to experiment or a professional seeking efficient production methods, this guide will provide you with the essential steps and tips. By the end, you’ll have the knowledge to make your own vacuum former and start bringing your ideas to life.
Key Takeaways
- Understanding Vacuum Forming: Vacuum forming is a process that uses heat and vacuum pressure to mold plastic sheets into specific shapes, allowing for precise replicas of designed molds.
- Versatile Applications: This technique is widely used across industries for prototype development, packaging solutions, theatrical props, custom signage, and automotive components.
- Essential Materials and Tools: Key components for building a vacuum former include plastic sheets (HIPS or acrylic), a heat source, a sturdy frame, sealing gaskets, a vacuum table, and a vacuum pump.
- Step-by-Step Construction: The construction process involves designing your mold, building the frame, setting up the vacuum table, and conducting tests to ensure functionality.
- Testing for Effectiveness: After assembly, testing your vacuum former is crucial, focusing on vacuum seal integrity, uniform heating of plastic, and troubleshooting common issues like uneven thickness or sticking.
- Enhancing Creativity: By building a vacuum former, you unlock new creative possibilities for custom projects, enhancing both hobbyist and professional applications.
Understanding Vacuum Forming
Vacuum forming is a simple yet effective process used to create three-dimensional shapes from plastic sheets. This method involves heating a plastic sheet until it’s pliable, then using a vacuum to pull it down over a mold, forming a specific shape.
What Is Vacuum Forming?
Vacuum forming is a manufacturing process that utilizes heat and vacuum pressure to mold plastic. During this process, you heat a plastic sheet until it softens. After that, you place the heated sheet over a mold and activate the vacuum, which sucks the sheet down into the mold’s contours. This technique results in a precise replica of the mold’s design. Common plastic materials used include polystyrene, ABS, and polypropylene.





Applications of Vacuum Forming
Vacuum forming serves a variety of industries and projects, making it a versatile method. Here are some common applications:
- Prototype Development: Designers and engineers use vacuum forming to create quick prototypes, allowing for rapid testing of designs.
- Packaging Solutions: Many products utilize vacuum-formed packaging, providing a cost-effective and protective way to store items.
- Theatrical Props: The film and theater industries often rely on vacuum forming for creating detailed prop components and set pieces.
- Custom Signage: Businesses frequently employ vacuum forming to produce 3D signs, enhancing visibility and appeal.
- Automotive Components: Parts like dashboards and consoles are commonly produced using this method, allowing for intricate shapes.
By understanding vacuum forming, you open up a range of possibilities for your projects, from simple designs to complex shapes in various applications.
Essential Materials and Tools
Building a vacuum former involves specific materials and tools. Gather these essentials for a successful project.
Required Materials
- Plastic Sheets: Choose high-impact polystyrene (HIPS) or acrylic. Thickness of 1/8 inch is common for ease of forming.
- Heat Source: Use an oven or heat gun to soften the plastic sheets effectively.
- Wood or Metal Frame: Construct a frame to hold the plastic. The frame should have a size compatible with your projects.
- Sealing Gasket: Silicone or rubber gaskets help create a tight seal between the frame and the vacuum base.
- Vacuum Table: An airtight surface helps maintain vacuum pressure when forming.
- Drill: Use a drill for making holes in your vacuum table for airflow.
- Saw: A jigsaw or circular saw cuts the frame materials accurately.
- Measuring Tape: Employ a measuring tape to ensure precise dimensions for your frame and plastic sheets.
- Clamps: Utilize clamps to secure the plastic sheets during heating.
- Vacuum Pump: Invest in a vacuum pump for creating the necessary suction for forming.
Gathering these materials and tools lays the foundation for your vacuum forming process. With the right components, you’ll create custom shapes efficiently.
Step-by-Step Guide to Build a Vacuum Former
Building a vacuum former involves a few essential steps. Follow this guide to create a functional vacuum former that meets your project needs.
Preparing the Design
- Sketch your design. Start by creating detailed drawings of the object you want to create. Include dimensions and specific shapes.
- Choose the material. Select a plastic sheet, such as HIPS or acrylic, based on your project’s requirements.
- Cut the plastic. Using a saw, cut the sheet into a size slightly larger than your design to ensure sufficient coverage.
Constructing the Frame
- Gather materials. Use wood or metal for the frame construction. Ensure that it’s sturdy enough to withstand heat and vacuum pressure.
- Measure and cut pieces. Measure the dimensions required for the frame. Cut the pieces accordingly with a saw.
- Assemble the frame. Connect the cut pieces using screws or bolts. Check for stability, and make adjustments if needed.
- Add a sealing gasket. Attach a sealing gasket around the frame’s edge to ensure air-tight fit during the vacuum process.
- Set up the vacuum table. Create a vacuum table by drilling holes in a flat surface, ensuring even air distribution.
- Connect the vacuum pump. Attach the vacuum pump to the table using hoses. Ensure a secure connection to maintain suction.
- Test the vacuum. Run the vacuum pump and check for leaks. Make adjustments as necessary to achieve a strong vacuum.
- Align your frame. Position the frame with the heated plastic sheet over the vacuum table. Ensure the setup is stable before proceeding.
Following these steps allows you to build a reliable vacuum former tailored for your specific projects.
Testing Your Vacuum Former
Once you’ve built your vacuum former, testing it ensures it operates effectively. Follow these steps to verify functionality and make necessary adjustments.
Initial Tests and Adjustments
- Check the Vacuum Seal: Place a plastic sheet over the frame. Activate the vacuum pump. If air leaks around the edges, adjust the gaskets or sealing surfaces.
- Heat the Plastic: Use a heat gun or oven to preheat the plastic sheet. Ensure it becomes flexible without overheating. Test different temperatures for optimal results.
- Form a Test Shape: Position the heated plastic over a mold. Activate the vacuum and observe how the plastic conforms to the shape. Note any areas where it doesn’t form correctly.
- Evaluate Thickness: Check the finished product for even thickness. If certain areas are thicker or thinner, adjust the heating time or mold design accordingly.
- Inadequate Vacuum: If the vacuum isn’t strong enough, inspect the connections. Make sure all hoses are secure and the vacuum pump functions properly.
- Uneven Heating: If the plastic doesn’t heat uniformly, arrange your heating source evenly. Experiment with different heating times and distances.
- Sticking: If the plastic adheres to the mold, apply a release agent. Consider altering mold materials for non-stick properties.
- Bubbles or Wrinkles: If you notice air bubbles or wrinkles in the formed shape, check for adequate heating and proper vacuum application. Ensure the vacuum table surface is flat.
These testing and troubleshooting steps enhance your vacuum forming experience, enabling you to produce high-quality prototypes and shapes effectively.
Conclusion
Building your own vacuum former can be a rewarding project that opens up a world of creativity. With the right materials and a little patience you can craft custom shapes that suit your needs perfectly.
Take the time to test and troubleshoot your vacuum former to ensure it operates smoothly. This will not only enhance your skills but also improve the quality of your prototypes.
So gather your tools and get started on this exciting journey. You’ll be amazed at what you can create with your very own vacuum former. Happy forming!
Frequently Asked Questions
What is vacuum forming?
Vacuum forming is a manufacturing process that shapes plastic sheets into 3D forms using heat and vacuum pressure. It’s widely used in various industries for creating custom shapes and prototypes.
Who can benefit from building a vacuum former?
Both hobbyists and professionals can benefit from building a vacuum former. It allows you to create custom prototypes and shapes tailored to specific projects, enhancing creativity and efficiency.
What materials do I need to build a vacuum former?
Essential materials for building a vacuum former include plywood or MDF for the frame, a heat source (like an oven), a vacuum pump, and plastic sheets. Additional tools like screws, a router, and a cutting tool are also necessary.
How do I set up a vacuum table?
To set up a vacuum table, construct a flat surface that can accommodate your plastic sheet. Ensure it has holes or grooves for air to escape and connect it to your vacuum pump to create suction.
What are common troubleshooting issues in vacuum forming?
Common issues include inadequate vacuum, uneven heating, and plastic sticking to the mold. These can be addressed by checking the vacuum seal, adjusting heating methods, and ensuring proper alignment of the mold and plastic sheet.
How can I test my vacuum former after building it?
Test your vacuum former by forming simple shapes using plastic sheets. Check for a proper vacuum seal, evaluate the thickness of formed shapes, and inspect for bubbles, wrinkles, or other imperfections during the process.
What applications can vacuum forming be used for?
Vacuum forming is commonly used for producing prototypes, packaging, signage, and automotive parts. Its versatility makes it suitable for a wide range of creative and industrial projects.
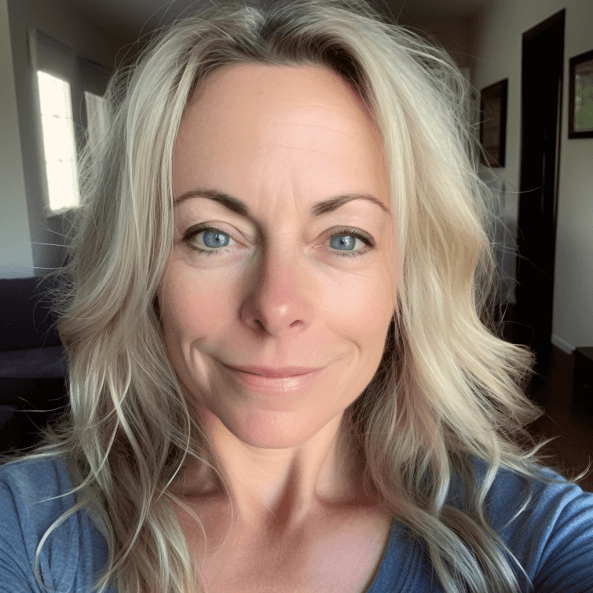