Dyson V11 Origin Cordless Vacuum, Nickel/Blue
- Versatile and cordless for whole-home deep cleaning.
Shark NV752 Rotator Powered Lift-Away TruePet Upright Vacuum with HEPA Filter, Large Dust Cup Capacity, LED Headlights, Upholstery Tool, Perfect Pet Power Brush & Crevice Tool, Bordeaux
- 2-IN-1 POWERED LIFT-AWAY TECHNOLOGY: Allows you to lift the pod away to deep-clean hard-to-reach areas, like under furniture, while the powered brushroll keeps spinning.
O-Cedar EasyWring Microfiber Spin Mop, Bucket Floor Cleaning System, Red, Gray, Standard
- HANDS-FREE WRINGING: Our exclusive mop bucket design features a built-in wringer that allows for hands-free wringing while Splash Guard keeps water splash and spray inside the bucket when wringing or when transporting the bucket from room to room
Electric Spin Scrubber for Cleaning Bathroom: Cordless Power Shower Scrubber - Electric Cleaning Brush for Tile Tub
- Multi-Surface Efficiency: Experience a deep clean across various surfaces with our Electric Spin Scrubber. Perfect for tiles, windows, bathtubs, toilets, and kitchen sinks. Effortlessly tackle dirt and grime where you need it most.
AIDEA Microfiber Cleaning Cloths, 50PK, Microfiber Towels for Cars, Premium All Purpose Car Cloth, Dusting Cloth Cleaning Rags, Absorbent Towels for SUVs, House, Kitchen, Window, 12"×12"
- Super Absorbent: Experience the excellent quality of AIDEA all-purpose microfiber cleaning cloths; made from 87% polyester and 13% polyamide; offering exceptional absorbency and quickly wicking away water to keep you dry; ideal for swiftly and safely removing dirt, grime, and liquids
Have you ever struggled with a messy workshop or faced the hassle of dust and debris while working on a project? A vacuum system can be your best friend in creating a cleaner and more efficient workspace. It not only keeps your area tidy but also improves safety and productivity.
Key Takeaways
- Understanding Vacuum Systems: Vacuum systems are essential for maintaining cleanliness and safety in workshops by effectively removing dust and debris.
- Types of Vacuum Systems: Choose from various options including centralized, portable, wet/dry, shop, and industrial vacuum systems based on your specific project needs.
- Key Components: Essential components include vacuum pumps, vacuum chambers, fittings, and valves, each serving a crucial role in the system’s functionality and efficiency.
- Step-by-Step Building Guide: Follow a structured plan for assembling your vacuum system, including defining requirements, choosing components, and ensuring airtight seals.
- Common Mistakes to Avoid: Prevent system failures by regularly maintaining components, ensuring proper sealing, and inspecting connections to maintain optimal performance.
Understanding Vacuum Systems
Vacuum systems play a crucial role in maintaining a clean and efficient workspace. They effectively remove dust and debris, ensuring a safer environment for your projects.
What Is a Vacuum System?
A vacuum system creates a space devoid of air or matter, allowing you to collect and remove unwanted materials. It typically consists of a vacuum pump, which generates the vacuum, and a network of hoses and filters. These components work together to capture and contain debris, improving air quality and cleanliness in your workshop. For example, when working with power tools, a vacuum system can significantly reduce dust particles that affect both health and visibility.
Types of Vacuum Systems
Several vacuum systems cater to different needs in a workshop. Understanding these types helps you select the right one for your projects.





- Centralized Vacuum Systems:
- Centralized systems are installed in a dedicated location, connected to multiple workspaces via a network of pipes.
- They offer powerful suction and eliminate noise near the work area, maintaining a quiet environment.
- Portable Vacuum Systems:
- Portable systems are easy to move and can be used in various locations.
- They often come with wheels and are powered by electricity or batteries, providing flexibility during tasks.
- Wet/Dry Vacuums:
- Wet/dry vacuums handle both liquid and solid debris.
- They work well for cleaning up spills in addition to dust, making them versatile in any workshop.
- Shop Vacuums:
- Shop vacuums are robust units typically used for heavy-duty cleaning tasks.
- They can capture larger debris and are often used alongside power tools for maximum efficiency.
- Industrial Vacuum Systems:
- Industrial systems are designed for commercial applications requiring high suction power and capacity.
- They handle large volumes of dust and debris, ideal for large-scale operations.
Selecting the right vacuum system depends on your specific needs, project types, and workspace size. Consider the features and benefits of each type to find the perfect fit for your workshop.
Essential Components
Building an effective vacuum system requires several key components that work together to achieve optimal performance. Understanding these components makes it easier for you to select and assemble what you need.
Vacuum Pumps
Vacuum pumps are the heart of any vacuum system. They remove air and create a vacuum, making it possible to draw unwanted materials.
- Types of Vacuum Pumps: Positive displacement pumps and momentum transfer pumps are common varieties. Positive displacement pumps trap air and expel it, while momentum transfer pumps use high-speed blades to push air out.
- Power Source: Ensure your vacuum pump matches your power supply, whether it’s electric or pneumatic. Choosing the right power source affects overall efficiency and capacity.
- Capacity: Select a pump with adequate capacity for your specific task. For instance, small workshops benefit from rotary vane pumps, while industrial settings may require larger diaphragm pumps.
Vacuum Chambers
Vacuum chambers contain the environment where the vacuum is created. They must be sealed appropriately to maintain the vacuum.
- Material: Choose materials like stainless steel or acrylic, which withstand vacuum pressure without deforming. Durable materials prevent leaks and ensure longevity.
- Seal Quality: Selecting high-quality seals is essential. O-rings and gaskets made of resilient materials maintain airtight conditions.
- Size: Consider the size of your vacuum chamber based on your projects. For small parts, a compact chamber suffices, while larger items may need extended spaces to fit comfortably.
Fittings and Valves
Fittings and valves are crucial for connecting components and controlling airflow.
- Fittings: Use the right fittings for your tubing and hoses. Compression fittings and quick-connects simplify assembly and disassembly without leaks.
- Valves: Incorporate manual or automatic valves to control air intake and release. Ball valves provide reliable shut-off, while solenoid valves enable automated adjustments based on the system needs.
- Adapters: Have a selection of adapters on hand for different hose sizes. Adapters ensure compatibility across various components, increasing system flexibility.
Incorporating these essential components lays a solid foundation for your vacuum system, ensuring it performs efficiently for your workshop needs.
Step-by-Step Guide
Building a vacuum system involves careful planning and precise assembly. Follow these steps to create a reliable system suitable for your workshop.
Planning Your System
- Define your requirements. Assess the specific tasks you’ll perform, such as material handling or dust collection.
- Choose the right vacuum pump type. Consider factors like airflow rates and ultimate vacuum levels.
- Determine the size of your vacuum chamber. Base this on the volume of materials you’ll work with.
- Plan the layout. Ensure that hoses and fittings minimize bends to optimize airflow.
- Calculate power needs. Check the power specifications for each component to avoid compatibility issues.
Assembling the Components
- Gather all components. Ensure you have the vacuum pump, chamber, fittings, valves, and hoses ready.
- Connect the vacuum pump to the hoses. Use clamps or fittings to secure connections tightly to prevent leaks.
- Install the vacuum chamber. Attach it securely to maintain an airtight seal.
- Attach fittings and valves. Use high-quality fittings to enhance the system’s efficiency.
- Verify connections. Inspect each joint and fitting for any signs of air leaks.
- Turn on the vacuum pump. Monitor the power levels and listen for unusual noises.
- Check the vacuum level. Use a gauge to ensure it reaches the required vacuum level for your tasks.
- Inspect for leaks. Apply soapy water to joints; bubbles indicate air leaks.
- Test the system under load. Run the system with materials to ensure it performs effectively.
- Adjust as necessary. If issues arise, revisit your connections and system components.
Common Mistakes to Avoid
Building a vacuum system involves careful attention to detail. Several common mistakes can hinder your project’s success. Avoiding these pitfalls enhances your system’s performance and durability.
Overlooking Maintenance
Skipping maintenance leads to decreased efficiency and potential system failure. Regularly inspect components, including filters and hoses, to ensure they function properly. Clean vacuum chambers to prevent debris buildup that can affect performance. Schedule routine checks every few months for optimal results. Keeping an eye on your system ensures it operates at peak performance.
Improper Sealing
Improper sealing creates leaks that reduce vacuum efficiency. Always use high-quality seals compatible with your materials. Check connections between the pump, hoses, and fittings for tightness. Use proper sealing techniques, like applying Teflon tape on threaded connections, to prevent leaks. Test seals under operational conditions to confirm they hold. Good sealing practices ensure your vacuum system runs effectively without losing power.
Conclusion
Building a vacuum system can be a rewarding project that enhances your workshop experience. By carefully selecting the right components and following the steps outlined, you’ll create a system that meets your specific needs.
Remember to pay attention to maintenance and sealing to keep everything running smoothly. With a little patience and effort, you’ll enjoy the benefits of a cleaner and more efficient workspace. So go ahead and start your vacuum system journey; you won’t regret it!
Frequently Asked Questions
What are the benefits of using vacuum systems in workshops?
Vacuum systems enhance cleanliness by reducing dust and debris, improve safety by minimizing hazards, and boost productivity by streamlining processes. They create a controlled environment for various tasks, helping prevent contamination and ensuring a smoother workflow.
What components are required for an effective vacuum system?
Key components include vacuum pumps, vacuum chambers, and fittings/valves. Each part plays a crucial role in maintaining a strong and reliable vacuum, ensuring efficient operation of the system in a workshop setting.
How do I choose the right vacuum pump for my needs?
Consider factors such as the desired vacuum level, the type of materials you’ll be working with, and the pump’s capacity. Assess your workflow requirements to determine power sources, performance ratings, and compatibility with other system components.
What types of vacuum pumps are available?
Common types of vacuum pumps include diaphragm, rotary vane, and piston pumps. Each type varies in mechanism, performance, and suitability for different applications, so choose one that aligns with your workshop’s specific requirements.
How do I build a vacuum system step-by-step?
Start by defining your requirements. Next, select the appropriate pump, size your vacuum chamber, plan the layout, and calculate power needs. Follow with assembling components, connecting hoses, installing the chamber, and ensuring all connections are sealed properly.
What common mistakes should I avoid when building a vacuum system?
Avoid overlooking maintenance, as it can lead to inefficiencies and failure. Also, ensure proper sealing to prevent leaks, which can reduce vacuum strength and overall performance. Regular checks and adjustments are vital for optimal functionality.
How can I maintain my vacuum system for optimal performance?
Regular maintenance includes cleaning filters, inspecting seals, checking for leaks, and ensuring all components are functioning properly. Create a maintenance schedule to perform these checks routinely, prolonging the life and efficiency of your vacuum system.
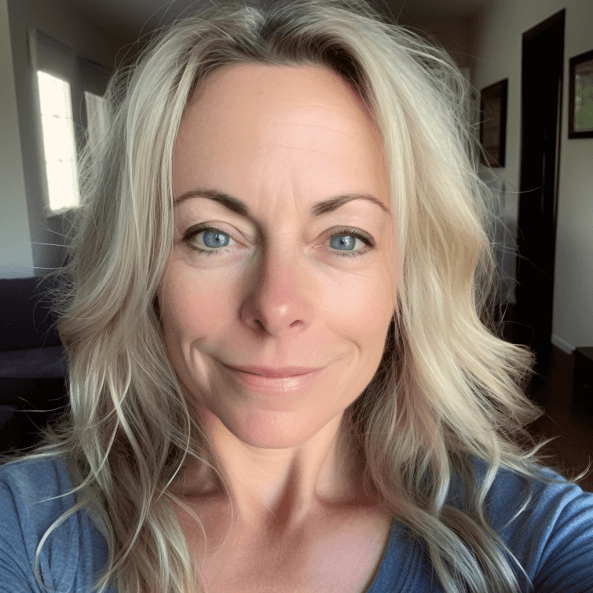