Dyson V11 Origin Cordless Vacuum, Nickel/Blue
- Versatile and cordless for whole-home deep cleaning.
Shark NV752 Rotator Powered Lift-Away TruePet Upright Vacuum with HEPA Filter, Large Dust Cup Capacity, LED Headlights, Upholstery Tool, Perfect Pet Power Brush & Crevice Tool, Bordeaux
- 2-IN-1 POWERED LIFT-AWAY TECHNOLOGY: Allows you to lift the pod away to deep-clean hard-to-reach areas, like under furniture, while the powered brushroll keeps spinning.
O-Cedar EasyWring Microfiber Spin Mop, Bucket Floor Cleaning System, Red, Gray, Standard
- HANDS-FREE WRINGING: Our exclusive mop bucket design features a built-in wringer that allows for hands-free wringing while Splash Guard keeps water splash and spray inside the bucket when wringing or when transporting the bucket from room to room
Electric Spin Scrubber for Cleaning Bathroom: Cordless Power Shower Scrubber - Electric Cleaning Brush for Tile Tub
- Multi-Surface Efficiency: Experience a deep clean across various surfaces with our Electric Spin Scrubber. Perfect for tiles, windows, bathtubs, toilets, and kitchen sinks. Effortlessly tackle dirt and grime where you need it most.
AIDEA Microfiber Cleaning Cloths, 50PK, Microfiber Towels for Cars, Premium All Purpose Car Cloth, Dusting Cloth Cleaning Rags, Absorbent Towels for SUVs, House, Kitchen, Window, 12"×12"
- Super Absorbent: Experience the excellent quality of AIDEA all-purpose microfiber cleaning cloths; made from 87% polyester and 13% polyamide; offering exceptional absorbency and quickly wicking away water to keep you dry; ideal for swiftly and safely removing dirt, grime, and liquids
Have you ever noticed your vacuum not performing as well as it should? A faulty vacuum check valve might be the culprit. This small but crucial component ensures that air flows in the right direction, keeping your vacuum running smoothly. If it’s not working properly, you could be losing suction power and wasting time.
Key Takeaways
- Understanding Vacuum Check Valves: They are essential components that ensure airflow direction, preventing backflow and maintaining vacuum pressure across various systems like automotive and HVAC.
- Signs of a Faulty Valve: Watch for loss of vacuum pressure, unusual noises, increased energy consumption, visible wear, and inconsistent performance, all indicating potential valve issues.
- Timely Inspection Importance: Regular checks of the valve can prevent costly repairs and downtime, enhancing system efficiency and extending equipment lifespan.
- Inspection Process Steps: Use necessary tools like a vacuum gauge, conduct visual checks, assess functionality, and perform cleaning, to ensure proper operation of the vacuum check valve.
- Maintenance Best Practices: Routine inspections and cleaning, along with seal checks, can help keep the valve in optimal condition, significantly reducing the risk of malfunctions.
- Replacement Indicators: Persistent leaks, frequent malfunctions, odd noises, and age over five years are clear signs that it’s time to consider replacing the vacuum check valve.
Understanding Vacuum Check Valves
A vacuum check valve is crucial for maintaining proper airflow in vacuum systems. Understanding how it functions ensures you can identify issues before they affect performance.
What Is a Vacuum Check Valve?
A vacuum check valve is a one-way valve designed to allow airflow in one direction only. This prevents backflow and maintains consistent vacuum pressure. Common types include spring-loaded and diaphragm check valves, each serving similar purposes but in different applications. For instance, in automotive systems, a spring-loaded valve often regulates vacuum pressure to control various engine components.
Common Applications
Vacuum check valves serve several applications across different industries, including:





- Automotive Systems: Used in brake boosters and engine control units to maintain vacuum integrity.
- HVAC Systems: Ensures efficiency by preventing air from flowing backward in ductwork.
- Industrial Equipment: Facilitates safe operation in vacuum packaging and material handling equipment.
- Medical Devices: In vacuum pumps for suction aids, ensuring consistent flow without back pressure.
Recognizing these applications helps you appreciate the valve’s importance in diverse systems.
Signs of a Faulty Vacuum Check Valve
Recognizing the signs of a faulty vacuum check valve ensures you address issues promptly. A malfunctioning valve can lead to inefficient system performance and increased operational costs.
Symptoms to Watch For
- Loss of Vacuum Pressure: If your system struggles to maintain vacuum pressure, the valve might allow backflow.
- Unusual Noises: Listen for hissing or wheezing sounds during operation; these often indicate air leaks through the valve.
- Increased Energy Consumption: Notice a spike in energy use? It may signal that the system works harder due to a defective valve.
- Visible Wear and Tear: Inspect the valve for cracks, discoloration, or corrosion, as these physical signs usually point to failure.
- Inconsistent Performance: If your vacuum system experiences fluctuations, the valve may not be sealing properly.
Importance of Timely Inspection
Timely inspection of the vacuum check valve prevents costly repairs and system downtime. Keeping an eye on its condition promotes optimal performance and extends the lifespan of your equipment. Regular checks reduce the risk of more severe issues, saving you time and money in the long run. Consider inspecting the valve every few months, especially in high-use environments.
How to Check a Vacuum Check Valve
Checking a vacuum check valve requires a few tools and a systematic approach. This process helps ensure your vacuum system operates efficiently.
Gathering Necessary Tools
- Wrench Set: Use a wrench to remove fittings and secure connections.
- Screwdriver: A flathead or Phillips screwdriver aids in accessing screws.
- Vacuum Gauge: Check pressure levels to identify issues in the system.
- Cleaning Supplies: Keep a cloth and brush handy for cleaning the valve.
- Safety Gear: Wear gloves and goggles for protection during inspection.
- Turn Off the System: Always power down the vacuum system before starting the inspection. This prevents accidental operation.
- Locate the Valve: Find the vacuum check valve in your setup. Consult your system’s manual for exact positioning.
- Visual Inspection: Examine the valve for signs of wear, cracks, or other damage. Look for any visible leaks.
- Check with the Vacuum Gauge: Attach the vacuum gauge to the system’s port. Observe the pressure readings; abnormal levels indicate valve malfunction.
- Remove and Inspect: If issues arise, detach the valve. Clean it with a brush and cloth to remove any debris. Inspect the inner parts for blockages or damage.
- Test the Valve’s Functionality: Reinstall the valve and recheck the pressure. The valve should allow airflow in one direction while blocking it in the opposite direction.
- Reassemble and Power Up: Once inspection and cleaning are complete, reattach all components securely. Power on the system and monitor for proper operation.
By adhering to this structured approach, you can effectively check your vacuum check valve and maintain system performance.
Maintenance Tips and Best Practices
Regular maintenance extends the lifespan of your vacuum check valve and enhances system efficiency. Implementing these tips ensures that your valve remains in optimal condition.
Routine Checks and Cleaning
Conduct routine checks every few months to identify potential issues. Follow these steps:
- Examine the Valve: Inspect for any visible signs of wear, such as cracks or leaks. Ensure connections are secure.
- Clean the Valve: Use a soft cloth to remove dust and debris. A blocked valve can disrupt airflow, so ensure it’s free from obstruction.
- Check the Seals: Inspect the rubber seals for any deterioration. Replace worn seals to maintain a proper vacuum.
- Test for Obstructions: Blow air through the valve in the direction of flow. If air flows both ways, the valve may be malfunctioning.
When to Replace the Valve
Know when it’s time to replace your vacuum check valve. Consider these signs:
- Persistent Leaks: If leaks occur despite repairs, replacement is necessary.
- Frequent Malfunctions: Regular issues with closure or opening indicate a failing valve that needs replacement.
- Unusual Noises: Odd sounds during operation may signal internal damage.
- Age of the Valve: If the valve is over five years old and shows signs of wear, consider replacing it to prevent future problems.
Following these maintenance tips helps ensure your vacuum system operates smoothly and efficiently, mitigating the risk of unplanned downtime and costly repairs.
Conclusion
Regularly checking your vacuum check valve can save you time and money in the long run. By staying proactive with maintenance and inspections you can keep your system running smoothly. Remember to look out for signs that indicate it’s time for a replacement and don’t hesitate to take action if something seems off.
With a little attention and care your vacuum system will perform at its best ensuring efficiency and reliability. So go ahead and make those checks a part of your routine to enjoy hassle-free operation.
Frequently Asked Questions
What is a vacuum check valve?
A vacuum check valve is a device that allows airflow in one direction while preventing backflow. It plays a crucial role in maintaining optimal airflow and performance in various industrial systems.
Why are vacuum check valves important?
These valves ensure that the airflow direction remains consistent, which is essential for the efficiency and reliability of vacuum systems across different industries. They help prevent costly damages caused by improper airflow.
How often should vacuum check valves be inspected?
It’s recommended to inspect vacuum check valves at regular intervals, ideally every few months, to identify and address any potential issues before they lead to inefficiencies or costly repairs.
What are common signs a vacuum check valve needs replacement?
Indicators that a valve may need replacing include persistent leaks, frequent malfunctions, unusual noises, and age-related wear. Addressing these early can help avoid system failures.
What maintenance tips can improve the lifespan of vacuum check valves?
Regular maintenance includes routine inspections, cleaning the valves, checking seals for wear, and testing for any obstructions. Following these practices can enhance efficiency and extend valve lifespan.
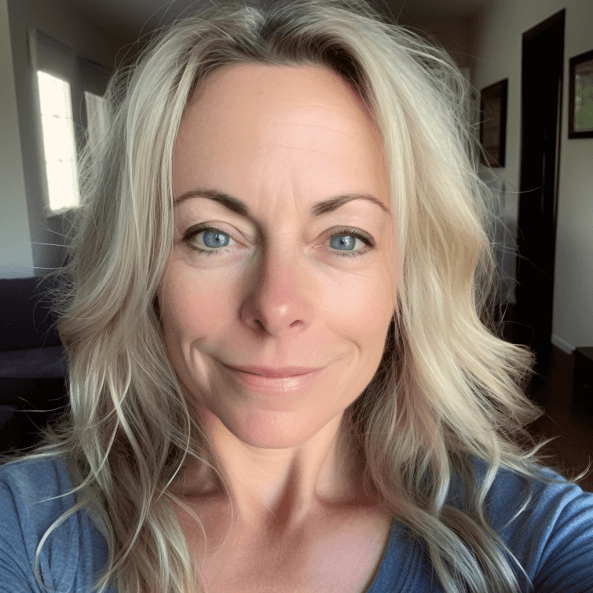