Dyson V11 Origin Cordless Vacuum, Nickel/Blue
- Versatile and cordless for whole-home deep cleaning.
Shark NV752 Rotator Powered Lift-Away TruePet Upright Vacuum with HEPA Filter, Large Dust Cup Capacity, LED Headlights, Upholstery Tool, Perfect Pet Power Brush & Crevice Tool, Bordeaux
- 2-IN-1 POWERED LIFT-AWAY TECHNOLOGY: Allows you to lift the pod away to deep-clean hard-to-reach areas, like under furniture, while the powered brushroll keeps spinning.
O-Cedar EasyWring Microfiber Spin Mop, Bucket Floor Cleaning System, Red, Gray, Standard
- HANDS-FREE WRINGING: Our exclusive mop bucket design features a built-in wringer that allows for hands-free wringing while Splash Guard keeps water splash and spray inside the bucket when wringing or when transporting the bucket from room to room
Electric Spin Scrubber for Cleaning Bathroom: Cordless Power Shower Scrubber - Electric Cleaning Brush for Tile Tub
- Multi-Surface Efficiency: Experience a deep clean across various surfaces with our Electric Spin Scrubber. Perfect for tiles, windows, bathtubs, toilets, and kitchen sinks. Effortlessly tackle dirt and grime where you need it most.
AIDEA Microfiber Cleaning Cloths, 50PK, Microfiber Towels for Cars, Premium All Purpose Car Cloth, Dusting Cloth Cleaning Rags, Absorbent Towels for SUVs, House, Kitchen, Window, 12"×12"
- Super Absorbent: Experience the excellent quality of AIDEA all-purpose microfiber cleaning cloths; made from 87% polyester and 13% polyamide; offering exceptional absorbency and quickly wicking away water to keep you dry; ideal for swiftly and safely removing dirt, grime, and liquids
Have you ever wondered if your vacuum system is working efficiently? Maybe you’ve noticed some issues with performance or just want to ensure everything’s running smoothly. Understanding how to check vacuum pressure can save you time and money by preventing bigger problems down the line.
Key Takeaways
- Understanding Vacuum Pressure: Vacuum pressure measures how much pressure is below atmospheric levels, indicating the efficiency of your vacuum system; lower pressure means better performance.
- Importance of Measurement: Regular vacuum pressure checks help optimize performance, extend equipment life, maintain process control, and ensure safety in critical applications.
- Tools for Measurement: Use specific tools such as vacuum gauges (analog, digital, compound) along with hoses, adapters, and sealants to ensure accurate readings.
- Step-by-Step Checking Process: Follow a systematic approach: gather tools, prepare the system, connect the gauge, activate the system, read and evaluate the gauge, and document findings.
- Interpreting Readings: Understand readings in inches of mercury (inHg) or millibars (mbar) to assess vacuum system efficiency, with specific ranges indicating strong, moderate, or weak vacuum conditions.
- Troubleshooting Techniques: Low vacuum pressure may signal issues like leaks or equipment failure; routinely check hoses, pumps, gauges, and filters to maintain optimal performance.
Understanding Vacuum Pressure
Vacuum pressure refers to the pressure in a system where the atmospheric pressure has been reduced. Knowing how to measure it helps you maintain your vacuum system’s efficiency and performance.
What Is Vacuum Pressure?
Vacuum pressure measures how much pressure is below atmospheric pressure. It’s expressed in units such as inches of mercury (inHg) or millibars (mbar). For example, 29.92 inHg indicates a complete vacuum, while a reading of 0 inHg reflects standard atmospheric pressure at sea level. In simple terms, the lower the vacuum pressure, the more effective your vacuum system is at removing air or gases.
Importance of Vacuum Pressure Measurement
Measuring vacuum pressure is crucial for several reasons:





- Performance Optimization: Regular checks ensure the vacuum system operates at peak efficiency. If pressure readings drop unexpectedly, it may signal leaks or other issues.
- Equipment Longevity: Consistent monitoring extends the life of your vacuum system. Avoiding excessive wear and tear from improper pressure levels saves costs on repairs.
- Process Control: Many industrial processes depend on specific vacuum conditions. Accurate measurements maintain product quality and prevent waste.
- Safety Assurance: Certain applications, like chemical handling or food packaging, require precise vacuum levels. Incorrect pressure readings could lead to hazardous situations.
Incorporating vacuum pressure checks into your routine maintenance will enhance system reliability and performance.
Tools Required for Checking Vacuum Pressure
To check vacuum pressure accurately, you’ll need specific tools to ensure reliable readings.
Vacuum Gauges
Vacuum gauges are essential for measuring vacuum pressure. Here are a few types:
- Analog Gauges: These use a dial to display pressure. They’re simple and provide a visual representation, making them user-friendly.
- Digital Gauges: They offer precise readings and are easy to read. Many models include features like data logging.
- Compound Gauges: These measure both vacuum and positive pressures. They’re versatile and useful in various applications.
When selecting a gauge, consider the measurement range needed for your system.
Additional Equipment Needed
Besides vacuum gauges, a few other tools enhance your vacuum pressure checks:
- Hoses: Use flexible and durable hoses to connect your gauge to the system. Ensure they can handle the pressure levels encountered.
- Adapters: Depending on your system type, you may need specific adapters to connect the gauge securely.
- Sealants: Ensure connections are airtight with sealants or tape. Leaks can lead to inaccurate readings.
- Calibrated Reference Pump: A calibrated pump assists in verifying gauge accuracy. Regular calibration maintains measurement precision.
Gathering these tools ensures an efficient and accurate assessment of vacuum pressure.
How to Check Vacuum Pressure
Checking vacuum pressure involves simple steps, ensuring accurate readings and system efficiency. Follow these instructions to gauge your vacuum pressure correctly.
Step-by-Step Guide
- Gather Tools: Collect necessary tools, including a vacuum gauge, connecting hoses, and a calibrated reference pump. Ensure the gauge type—analog, digital, or compound—fits your needs.
- Prepare the System: Turn off all equipment connected to the vacuum system. Disconnect the power supply for safety. Ensure the area is clean and free from any contaminants.
- Connect the Gauge: Attach the vacuum gauge to the designated port on the vacuum system using appropriate hoses and adapters. Make sure the connection is tight to prevent leaks.
- Activate the System: Power on the vacuum system. Allow it to run for a few minutes until it reaches a stable operating condition.
- Read the Gauge: Observe the reading on the vacuum gauge. Take note of the pressure level indicated, which may be in inches of mercury (inHg) or millibars (mbar).
- Evaluate the Results: Compare the gauge reading with manufacturer’s specifications for your equipment. A lower pressure than expected suggests potential leaks or issues within the system.
- Document Findings: Make a record of the vacuum pressure reading. Regular documentation aids in monitoring performance over time.
- Ignoring Calibration: Failing to calibrate your vacuum gauge before use affects accuracy. Always check calibration against known standards.
- Neglecting Leaks: Overlooking potential leaks during connection compromises readings. Inspect all connections for tightness.
- Misreading Gauge Types: Confusing gauge types could lead to incorrect readings. Be aware of how different gauges display pressure.
- Inconsistent Maintenance: Skipping regular vacuum pressure checks can result in performance degradation. Establish a routine schedule for monitoring.
- Using Unapproved Tools: Employing non-compatible tools may yield inaccurate measurements. Always use equipment designed for your vacuum system.
Following these steps ensures reliable vacuum pressure readings, enhancing overall system performance and longevity.
Interpreting Vacuum Pressure Readings
Understanding vacuum pressure readings is essential for assessing your system’s performance. These readings provide insights into how effectively your vacuum system operates.
Understanding the Measurements
Vacuum pressure is typically measured in inches of mercury (inHg) or millibars (mbar). Here’s how to interpret these measurements:
- Inches of Mercury (inHg): This scale indicates how far a column of mercury can be pushed by atmospheric pressure. A reading higher than 0 inHg means the system operates below atmospheric pressure. Common ranges include:
- 20 inHg: Strong vacuum
- 15-20 inHg: Moderate vacuum
- Below 15 inHg: Weak vacuum.
- Millibars (mbar): This unit measures pressure in metric terms. One atmosphere equates to about 1013 mbar. Key ranges include:
- 100 mbar: Strong vacuum
- 200-300 mbar: Moderate vacuum
- Above 300 mbar: Weak vacuum.
Understanding these scales helps you judge the efficiency of your vacuum system.
Troubleshooting Low Vacuum Pressure
Low vacuum pressure readings typically indicate issues within the system. Here are steps to troubleshoot:
- Check for Leaks: Inspect hoses, fittings, and seals. Look for visible wear or damage. Use soapy water to identify air leaks; bubbles will indicate where air escapes.
- Inspect the Vacuum Pump: Ensure proper operation of the pump. If it’s not generating adequate suction, consider maintenance or replacement.
- Evaluate the Gauge: Confirm the gauge displays accurate readings. If unsure, test it against a known good gauge. Calibration errors can lead to incorrect assessments.
- Examine Filters and Valves: Blocked filters or malfunctioning valves reduce vacuum efficiency. Clean or replace filters regularly and ensure all valves operate smoothly.
- Review System Design: Assess whether the vacuum system meets the application’s needs. Incorrect sizing or design might restrict performance.
Identifying the cause of low vacuum pressure can lead to necessary repairs, ensuring your system operates at its best.
Conclusion
Keeping an eye on vacuum pressure is key to maintaining your system’s efficiency and longevity. By regularly checking your vacuum pressure and using the right tools you can catch potential issues early and prevent costly downtime. Remember to follow those simple steps for accurate readings and take note of any changes in performance.
With a little attention to detail and routine maintenance you can ensure your vacuum system runs smoothly for years to come. So grab your tools and start monitoring your vacuum pressure today. Your system will thank you!
Frequently Asked Questions
What is vacuum pressure?
Vacuum pressure measures the pressure level below atmospheric pressure, typically expressed in inches of mercury (inHg) or millibars (mbar). Understanding vacuum pressure is crucial for optimizing the efficiency of vacuum systems and ensuring their proper operation.
Why is monitoring vacuum pressure important?
Monitoring vacuum pressure is essential for maintaining system performance, extending equipment lifespan, controlling processes accurately, and ensuring safety. Regular checks help identify issues before they lead to significant problems, ultimately saving time and money.
What tools do I need to check vacuum pressure?
To accurately check vacuum pressure, you need specific tools such as vacuum gauges, hoses, adapters, appropriate sealants, and a calibrated reference pump. The right tools ensure efficient and precise assessments of the system’s vacuum pressure.
What types of vacuum gauges are available?
There are several types of vacuum gauges available, including analog, digital, and compound gauges. Each type offers distinct features, with digital gauges often providing more precise readings and easy readability.
What common mistakes should I avoid when checking vacuum pressure?
Common mistakes include ignoring calibration, overlooking potential leaks, misreading gauge types, inconsistent maintenance practices, and using unapproved tools. Avoiding these errors enhances the efficiency and reliability of your vacuum system.
How do I troubleshoot low vacuum pressure?
Troubleshooting low vacuum pressure involves checking for leaks, inspecting the vacuum pump, evaluating the gauge, examining filters and valves, and reviewing the overall system design. These steps help identify and address issues affecting vacuum efficiency.
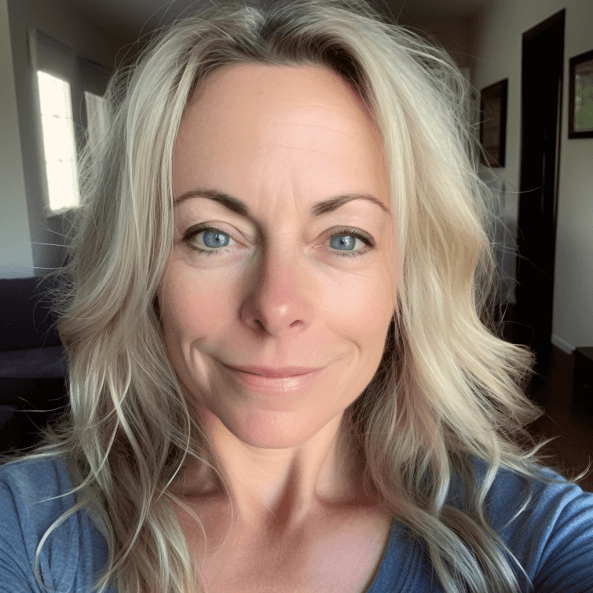