Have you ever faced a situation where one vacuum pump just isn’t enough to get the job done? Whether you’re working on a DIY project or managing a larger industrial setup, connecting two vacuum pumps in parallel can boost your efficiency and save you time.
Key Takeaways
- Understanding different types of vacuum pumps (positive displacement, momentum transfer, and entrapment) is crucial to select the right one for your needs.
- Connecting two vacuum pumps in parallel increases efficiency by doubling the total vacuum capacity and optimizing energy consumption through load sharing.
- Cost-effectiveness is a key benefit; investing in a second pump often proves more economical than upgrading to a higher-capacity single pump.
- Proper setup involves using compatible pumps, ensuring correct plumbing with T-connectors, and securing all connections to prevent air leaks.
- Common challenges, such as imbalances in load distribution and air leaks, can be mitigated through regular monitoring and maintenance.
- Following manufacturer guidelines and maintaining proper calibration help ensure reliable performance and prolong the lifespan of both pumps.
Overview of Vacuum Pumps
Vacuum pumps are essential devices used to remove air and other gases from sealed systems, creating a vacuum. They play a crucial role in various industries, including manufacturing, food packaging, and laboratory settings. Understanding how they work and their types helps you select the right equipment for your application.
Types of Vacuum Pumps
- Positive Displacement Pumps
- Positive displacement pumps remove gas by trapping a fixed volume and pushing it out.
- Common examples include rotary vane and diaphragm pumps.
- Momentum Transfer Pumps
- Momentum transfer pumps utilize jet action to carry gases away from the vacuum chamber.
- Examples include diffusion and turbo pumps.
- Entrapment Pumps
- Entrapment pumps capture gas molecules on a solid or liquid surface.
- Common types are cryopumps and sorption pumps.
Working Principles
- Positive Displacement Method
- The pump increases pressure in a chamber, allowing gas to escape through an exhaust port.
- Momentum Transfer Method
- Gases collide with high-speed blades, transferring momentum and reducing pressure.
- Entrapment Method
- Gas molecules stick to a substrate, effectively reducing the number of free molecules in the vacuum.
Applications of Vacuum Pumps
- Manufacturing
- Vacuum pumps are integral in processes such as mold-making and coating.
- Laboratories
- They create controlled environments for experiments and analyses.
- Food Packaging
- Used to prolong shelf life by removing air from packaging.
- Ensure both pumps are compatible in terms of pressure and flow rates.
- Use appropriate plumbing and fittings to minimize flow resistance.
- Consider control systems to prevent one pump from overloading the other during operation.
By understanding the fundamentals of vacuum pumps, you can optimize their use in your projects, whether you’re connecting two pumps in parallel or employing them for other applications.
Benefits of Connecting Two Vacuum Pumps in Parallel
Connecting two vacuum pumps in parallel provides significant advantages, enhancing overall performance and reliability.
Increased Efficiency
Increased efficiency stands out as a primary benefit. Connecting two pumps allows for a more substantial vacuum flow rate. When a single pump faces limitations, a parallel setup effectively doubles the total capacity, ensuring adequate vacuum levels are maintained. This is particularly useful in high-demand applications, such as large-scale manufacturing or laboratory processes requiring sustained vacuum levels.
Moreover, load sharing between the pumps optimizes energy consumption. Each pump operates within its preferred range, reducing wear and extending service life. When one pump operates at lower capacity, it draws less power, leading to energy savings.
Cost-Effectiveness
Cost-effectiveness enhances the appeal of connecting vacuum pumps in parallel. Investing in a second pump can be more affordable than upgrading to a higher-capacity single pump. The overall system benefits from reduced upfront costs while delivering the needed performance.
Maintenance costs also decrease with a parallel setup. With two pumps operating, you can rotate their usage, allowing for downtime without halting processes. This approach prolongs the lifespan of each pump, minimizes repair frequency, and cuts service expenses.
Overall, the combination of increased efficiency and cost-effectiveness makes connecting two vacuum pumps in parallel a smart choice for various applications.
Steps to Connect Two Vacuum Pumps in Parallel
Connecting two vacuum pumps in parallel maximizes efficiency and reliability. Follow these steps to ensure a successful setup.
Required Tools and Materials
- Vacuum Pumps: Two identical vacuum pumps with similar specifications.
- Vacuum Hoses: Sufficient length to connect both pumps to the desired outlet.
- T-connectors: Necessary for linking the vacuum hoses together.
- Clamps: Use clamps to secure hoses and prevent leaks.
- Wrenches: Needed for tightening fittings and connectors.
- Sealant: Consider using sealant tape for additional leak prevention.
- Position Pumps: Place both vacuum pumps securely side by side, ensuring adequate space around each pump for ventilation.
- Connect Hoses: Attach one end of a hose to each pump’s inlet. Securely fit hoses with clamps.
- Install T-connectors: Join the hoses from both pumps using T-connectors. Ensure the configuration allows for even flow distribution.
- Connect to Outlet: Attach another hose to the open end of the T-connector and route it to the desired vacuum outlet. Secure this connection with clamps as well.
- Seal Connections: Use sealant tape or sealant on all threaded connections to prevent air leaks, ensuring a strong vacuum seal.
- Test Setup: Turn on both pumps to ensure they operate smoothly. Monitor for unusual sounds or vibrations, indicating a potential issue.
- Adjust Settings: If applicable, adjust the settings on both pumps for optimal performance, ensuring they operate within their recommended pressure ranges.
- Monitor Performance: Regularly check vacuum levels and pump indicators to ensure both pumps share the workload efficiently.
By following these organized steps, you can effectively connect two vacuum pumps in parallel, enhancing your system’s performance.
Common Challenges and Solutions
Connecting two vacuum pumps in parallel can present some challenges. Understanding these issues can help you ensure a successful setup.
Potential Issues
- Imbalance in Load Distribution
Imbalances may occur if one pump takes on more load than the other. This can lead to premature wear on the pump with a higher load. You can mitigate this by selecting pumps with similar specifications. - Air Leaks
Leaks in the connection points can reduce the overall vacuum efficiency. Regularly check all connections and seals for any signs of wear or damage. - Vibration and Noise
Parallel pumps might generate increased vibration and noise levels. If vibration becomes excessive, consider using vibration dampening mounts to minimize the impact. - Electrical Compatibility
Different pumps might require varying electrical specifications. Ensure both pumps are compatible with the same power source to avoid operational issues.
- Monitor Performance
Consistently check the vacuum levels to ensure both pumps function as expected. Install pressure gauges on both pumps to track performance. - Check Connections
If performance drops, inspect all connections for leaks or blockages. Tighten any loose fittings and replace worn seals immediately. - Evaluate Pump Calibration
Confirm that both pumps are calibrated correctly. Mismatched calibration can lead to inefficiency and potential damage. - Adjust Operating Conditions
If one pump consistently underperforms, review the operating conditions. Adjusting the load or repositioning the pumps may help achieve better balance. - Consult Manufacturer Guidelines
Following manufacturer instructions can resolve issues specific to the model of vacuum pump you’re using. Refer to the manual for troubleshooting advice tailored to your equipment.
Conclusion
Connecting two vacuum pumps in parallel can significantly boost your system’s efficiency and reliability. By following the right setup process and addressing common challenges, you can create a more effective vacuum solution tailored to your needs.
Remember to keep an eye on performance and regularly check for any issues. With a bit of attention and care, you’ll enjoy the benefits of a well-functioning parallel setup. Your vacuum system will thank you for it!
Frequently Asked Questions
What are the benefits of connecting two vacuum pumps in parallel?
Connecting two vacuum pumps in parallel enhances efficiency, increases overall system reliability, and improves performance in high-demand environments like manufacturing and laboratories. This setup allows for better load distribution, reduces wear on individual pumps, and ensures continuous operation even if one pump fails.
How do I set up two vacuum pumps in parallel?
To set up vacuum pumps in parallel, first gather the necessary tools, such as wrenches, hose connectors, and vacuum gauges. Connect the pumps using appropriate piping while ensuring secure seals. Finally, test the system for performance, checking for leaks and measuring the vacuum level to ensure both pumps operate efficiently together.
What challenges might I face when connecting pumps in parallel?
Common challenges include load distribution imbalance, air leaks, vibration issues, and electrical compatibility. These problems can affect performance and reliability, so it’s essential to address them during setup to ensure smooth operation.
How can I mitigate load distribution imbalance?
To mitigate load distribution imbalance, select vacuum pumps with similar specifications and capacities. Regularly monitor performance, adjust operating conditions, and ensure proper calibration to maintain balanced workload across both pumps.
What should I do if there are air leaks in my setup?
If you detect air leaks, check all connections, seals, and fittings. Tighten or replace any faulty components to eliminate leaks. Conduct tests using a vacuum gauge to confirm that the system maintains an appropriate vacuum level after repairs.
How can vibration issues be addressed?
To address vibration issues, use vibration dampening mounts to isolate the pumps from the foundation and each other. Additionally, ensure that the pumps are installed on a stable surface and regularly check for signs of wear that can contribute to excessive vibrations.
How do I ensure electrical compatibility between the pumps?
To ensure electrical compatibility, check the voltage and phase ratings of both pumps before installation. Verify that the pumps can operate on the same electrical circuit without exceeding the load capacity. Consult the manufacturer’s specifications for additional guidelines.
How often should I monitor the performance of the connected pumps?
Regular monitoring of performance is recommended to catch potential issues early. Check the vacuum level, power consumption, and any signs of vibration or unusual sounds on a weekly basis. Consistent oversight helps maintain efficient operation and prolongs pump life.
What manufacturer guidelines should I follow for troubleshooting?
Always refer to the manufacturer’s guidelines for specific troubleshooting steps tailored to your vacuum pumps. These guidelines often provide insights on common issues, maintenance routines, and technical support contact information to resolve complex problems efficiently.
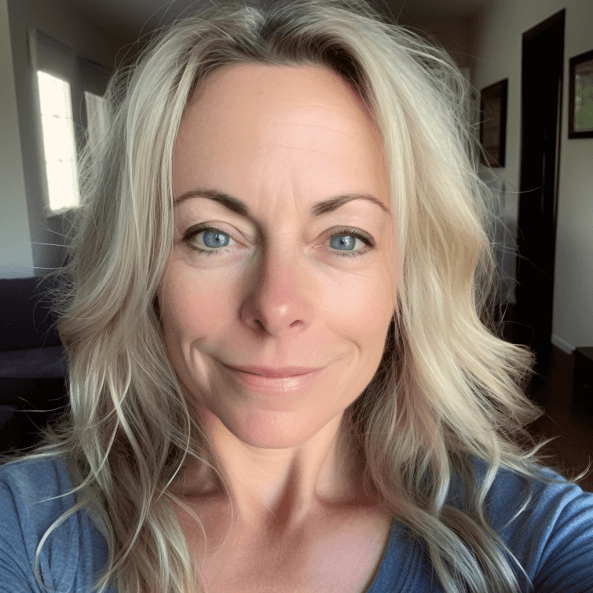