Have you ever faced issues with maintaining a clean workspace or managing dust and debris? Designing an effective vacuum system can be the solution you need. Whether you’re working on a DIY project or setting up a professional workshop, a well-thought-out vacuum system can make all the difference.
Key Takeaways
- Understanding Vacuum Systems: Grasp the importance of vacuum systems in maintaining clean workspaces and explore their various types: positive displacement, momentum transfer, and entrapment systems.
- Key Components: Familiarize yourself with the essential parts of a vacuum system, including pumps, valves, and chambers, each critical for optimal performance and vacuum integrity.
- Design Considerations: Prioritize factors such as pressure ranges, appropriate material selection, and safety features to ensure your vacuum system operates efficiently and safely.
- Define Requirements: Clearly outline your vacuum system’s specific needs, including pressure range, flow rate, and application type, as these will guide your design decisions.
- Choose and Layout Components: Select suitable components based on your requirements and create an efficient layout to optimize performance while ensuring accessibility for maintenance.
Understanding Vacuum Systems
Vacuum systems play a crucial role in keeping workspaces free from dust and debris. Grasping their components and functions helps you design an effective setup tailored to your needs.
Types of Vacuum Systems
- Positive Displacement Vacuum Systems
Positive displacement systems operate by trapping a specific volume of air and releasing it, creating a vacuum. Examples include rotary vane and diaphragm pumps. These systems excel in applications requiring high vacuum levels and consistency. - Momentum Transfer Vacuum Systems
Momentum transfer systems use high-speed blades or jets to transfer momentum to gas molecules, propelling them out of the chamber. Turbo molecular pumps serve as common examples. These systems are suitable for applications where ultra-high vacuum (UHV) is necessary. - Entrapment Vacuum Systems
Entrapment systems trap gas molecules physically or chemically within a confined space. Examples include cryopumps and ion pumps. These systems provide clean vacuum conditions without contamination and are often used in sensitive environments.
- Industrial Manufacturing
Vacuum systems maintain a clean workspace by removing dust and harmful particles, enhancing overall efficiency and product quality in industries like automotive and electronics. - Food Packaging
Vacuum sealing prolongs shelf life by removing air from packaging. This method is widely used in the food industry to prevent spoilage and maintain freshness. - Medical Devices
Vacuum systems ensure the cleanliness of medical equipment and help maintain precise environments in laboratories. This practice protects against contamination and ensures accurate test results. - Research and Development
In laboratories, vacuum systems support experiments requiring controlled environments. Applications include material testing and the synthesis of advanced materials, where vacuum conditions minimize interference from external elements.
Understanding the types and applications of vacuum systems enables you to create a tailored design that meets specific needs. Adjust your setup based on the intended use and desired performance outcomes.
Key Components of a Vacuum System
Understanding the key components of a vacuum system is essential for effective design and operation. The main parts include pumps, valves, and chambers, each playing a unique role in the system.
Pumps
Pumps are pivotal in generating the vacuum. They remove air or gas from a confined space to create low-pressure conditions. Different types of pumps serve various needs:
- Positive Displacement Pumps: These pumps trap a fixed volume of air and expel it, making them suitable for high-vacuum applications.
- Momentum Transfer Pumps: These utilize high-speed rotating blades to transfer momentum from gas molecules, effectively removing them from the chamber. They excel in medium to high vacuum levels.
- Entrapment Pumps: These capture gas molecules on surfaces or in solid mediums. They work well in ultra-high vacuum scenarios.
Choose a pump based on the desired pressure and application environment.
Valves
Valves control the flow of gases within the system. Their selection influences vacuum performance and stability. Key types of valves include:
- Isolation Valves: These prevent the backflow of gases, crucial in maintaining vacuum integrity. Ball and gate valves are common examples.
- Throttle Valves: These adjust the gas flow, allowing fine-tuning of vacuum levels. These valves help maintain desired pressures during operation.
- Relief Valves: These protect the system by releasing excess pressure to avoid damage. Pressure-sensitive designs provide reliable operation.
Select valves carefully to ensure optimal performance and reliability in your vacuum system.
Chambers
Chambers house the area where the vacuum occurs. Designing these chambers requires attention to size, shape, and material:
- Size and Shape: Ensure the chamber has adequate volume to accommodate the process requirements while also allowing efficient gas flow.
- Material: Choose materials that can withstand the conditions inside the chamber, including temperature and chemical exposure. Common choices include stainless steel and aluminum for their durability.
- Sealing: Implement effective sealing techniques to prevent leaks. Gaskets and o-rings can help maintain the required vacuum levels.
Focus on the design of your chamber to enhance the overall effectiveness of your vacuum system.
Design Considerations for Vacuum Systems
Designing a vacuum system involves key factors that ensure efficiency and safety. Below are essential considerations.
Pressure Ranges
Specifying pressure ranges is crucial for effective system design. Vacuum systems typically operate within low, medium, and high vacuum pressures. Low vacuum ranges from atmospheric pressure to 1 Torr, medium vacuum spans from 1 Torr to 10^-3 Torr, and high vacuum ranges from 10^-3 Torr to 10^-9 Torr. Knowing your application’s pressure needs allows you to select the correct pumps and components. For example, a semiconductor manufacturing process often requires high vacuum levels, while packaging applications may only need low vacuum.
Material Selection
Choosing appropriate materials impacts system performance and longevity. Materials must withstand vacuum pressure while resisting corrosion and wear. Common choices include stainless steel, glass, and certain plastics. For instance, stainless steel suits high-temperature applications due to its strength and resistance to oxidation. Considerations like thermal conductivity and vacuum compatibility are vital. Always ensure materials used for seals and components are rated for the system’s operational environment to avoid failures.
Safety Factors
Prioritizing safety protects equipment and personnel. Design systems to handle unpredicted pressure changes, including incorporating relief valves and pressure sensors. Implementing safety interlocks prevents operation under unsafe conditions, providing added protection. Training staff on vacuum system operation increases awareness of hazards. Regular maintenance checks also extend equipment life and mitigate risks associated with system failures.
Steps to Design a Vacuum System
Designing a vacuum system requires careful planning and execution. Follow these steps to ensure your system meets its intended purpose efficiently.
Define Requirements
Start by defining the specific requirements for your vacuum system. Identify the desired pressure range, volume flow rate, and application type. For example, semiconductor manufacturing may require ultra-high vacuum levels, while food packaging might only need low vacuum levels. Consider the materials involved and the nature of the process. Document these specifications clearly, as they guide the selection of components and overall system design.
Choose Components
Selecting the right components is crucial. Choose a vacuum pump based on the required pressure range and pumping speed. For rough vacuum applications, rotary vane pumps work well. For high vacuum systems, consider turbomolecular pumps. Select appropriate valves such as gate or check valves to control airflow. Choose fittings and tubing materials compatible with your application, ensuring leak-free connections. Always prioritize durability and resistance to the chemicals involved in your process.
Create a Layout
Design the physical layout of the vacuum system. Place components like pumps, valves, and chambers strategically to minimize pressure drops and optimize efficiency. Use a piping diagram to visualize connections. Ensure that all components are accessible for maintenance. Plan for sufficient space around the system for safety and easy operation. Consider vibration isolation and noise reduction if necessary. A well-thought-out layout leads to better performance and ease of use.
Conclusion
Designing a vacuum system can seem daunting but with the right approach it becomes manageable. By clearly defining your requirements and carefully selecting components you’ll create a system that not only meets performance needs but also enhances safety.
Don’t forget to consider the layout for optimal efficiency and accessibility. Each step you take in the design process contributes to a well-functioning vacuum system that serves your specific application.
With thoughtful planning and attention to detail you’re on your way to achieving a reliable and effective vacuum solution. Happy designing!
Frequently Asked Questions
What are vacuum systems used for in industries?
Vacuum systems are crucial for maintaining clean workspaces in various industries such as manufacturing, food processing, and pharmaceuticals. They are used to remove contaminants, dust, and particles from the environment, ensuring a safe and efficient work area.
What types of vacuum systems exist?
There are several types of vacuum systems, including positive displacement pumps, jet pumps, and diffusion pumps. Each system is designed for specific applications, from light-duty tasks to heavy industrial processes, catering to varying pressure requirements and operational needs.
What are the key components of a vacuum system?
The main components of a vacuum system include pumps, valves, and chambers. Pumps create the vacuum, valves control airflow, and chambers are used to contain the materials or processes being worked on, ensuring efficiency and safety in operation.
What considerations should be made when designing a vacuum system?
When designing a vacuum system, it’s important to specify pressure ranges, select suitable materials, and implement safety measures. Proper planning in these areas helps ensure that the system functions correctly and meets the specific needs of the application.
What steps are involved in designing a vacuum system?
Designing a vacuum system involves defining the specific requirements of the application, selecting appropriate components like pumps and valves, and creating an efficient layout. These steps focus on optimizing performance and ensuring accessibility for maintenance and operation.
How does proper planning affect vacuum system performance?
Proper planning is critical to vacuum system performance as it affects component selection, efficiency, and safety. A well-designed system can meet specific operational requirements while ensuring reliable performance and reducing the risk of failures or accidents.
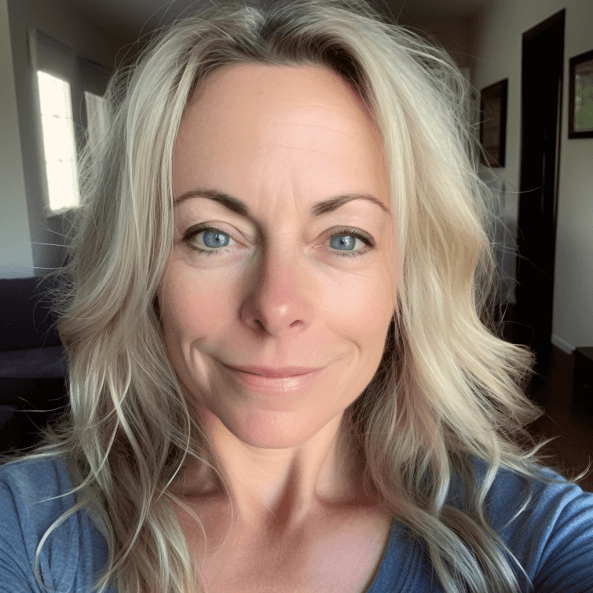