Ever looked at a vacuum pressure gauge and felt a bit lost? You’re not alone. Many people find themselves puzzled when trying to interpret the readings, especially if they’re new to working with vacuum systems. Understanding how to read these gauges is essential for ensuring your equipment operates efficiently and safely.
In this article, you’ll learn the basics of vacuum pressure gauges and how to read them correctly. You’ll discover the key terms and measurements that will make it easier to monitor your vacuum system. By the end, you’ll feel more confident in using these tools, helping you avoid costly mistakes and keep your projects on track.
Key Takeaways
- Understanding Gauge Types: Familiarize yourself with different vacuum pressure gauges—mechanical, electrical, thermocouple, and ionization—and their specific applications for better decision-making.
- Interpreting Readings: Learn to read the scale accurately, which typically appears as a negative value, signifying vacuum pressure in units like inches of mercury (inHg) and millibars (mbar).
- Key Measurement Units: Recognize the common units of measurement used in vacuum gauges to effectively convert and compare readings, such as inches of mercury (inHg), millibar (mbar), and Pascal (Pa).
- Importance of Calibration: Regular calibration of vacuum pressure gauges every six months is essential for accuracy, helping to maintain the reliability of your readings.
- Environmental Factors: Be aware of environmental conditions, such as temperature and humidity, that can affect gauge performance, and take measures to protect gauges from these elements.
- Application in Industries: Vacuum pressure gauges are critical in various sectors, including laboratories, industry, HVAC systems, and aerospace, ensuring safety and efficiency in operations.
Understanding Vacuum Pressure Gauges
Understanding vacuum pressure gauges helps you use them effectively in various applications. Gauges measure the level of vacuum by comparing the pressure inside a system to atmospheric pressure.
Types of Vacuum Pressure Gauges
- Mechanical Gauges
Mechanical gauges use a Bourdon tube to measure vacuum pressure. The tube bends with changes in pressure, providing a direct reading on the dial. These gauges are simple, reliable, and require no power supply. - Electrical Gauges
Electrical gauges, like capacitive or piezoresistive types, convert pressure changes into electrical signals. These gauges provide digital readings, making them easier to interpret. They offer high accuracy and often come with data logging features. - Thermocouple Gauges
Thermocouple gauges measure vacuum pressure through thermal conductivity. The gauge’s response varies with changes in pressure. These gauges are suitable for measuring high vacuums, offering sensitivity and reliability. - Ionization Gauges
Ionization gauges measure ultra-high vacuum levels. They use ionized gas to produce a current proportional to pressure. These gauges provide precise readings and are commonly used in scientific research or semiconductor manufacturing.
- Laboratory Equipment
Vacuum gauges are crucial in labs for experiments requiring controlled environments. They help in maintaining optimal conditions for experiments and ensure accurate results. - Industrial Processes
In industries, vacuum gauges monitor processes like packaging and food preservation. They ensure that products are sealed correctly and maintain their freshness. - HVAC Systems
Vacuum pressure gauges play a vital role in heating, ventilation, and air conditioning systems. They help technicians assess the integrity of refrigeration systems and ensure optimal performance. - Vacuum Pumps
You often find these gauges on vacuum pumps. They assist in monitoring the pump’s performance, indicating when maintenance or adjustment is necessary. - Aerospace and Automotive Industries
Vacuum pressure gauges aid in testing and diagnostics, guaranteeing safety and efficiency in aircraft and vehicle systems.
Using vacuum pressure gauges effectively in these applications enhances safety and efficiency, reducing costs and risks related to improper pressure measurements.
Components of a Vacuum Pressure Gauge
Understanding the components of a vacuum pressure gauge aids in accurate readings and effective system monitoring. Here’s a breakdown of the essential parts:
Dial and Scale
The dial displays the pressure levels in a clear, readable format. Scales often show measurements in inches of mercury (inHg) or millibars (mbar), depending on the gauge type. The scale ranges from atmospheric pressure down to the lowest vacuum levels. Look for the units that apply to your specific application. For instance, a scale might range from 0 to -30 inHg for measuring deep vacuum systems.
Pointer and Mechanism
The pointer indicates the current pressure level by moving along the scale. The mechanism, which may be mechanical or electronic, translates changes in pressure into pointer movement. Mechanical gauges use a flexible diaphragm that bends with pressure changes. Electronic gauges, on the other hand, utilize sensors to detect pressure variations. Each option has its advantages; mechanical gauges often provide simplicity, while electronic ones may offer higher accuracy.
By familiarizing yourself with these components, you can effectively interpret readings and maintain your vacuum systems with greater precision.
How to Read a Vacuum Pressure Gauge
Reading a vacuum pressure gauge involves understanding its components and measurements. You’ll be equipped to interpret the readings accurately.
Interpreting the Scale
Understanding the scale of a vacuum pressure gauge is essential for correct readings. The scale usually displays pressure as a negative value (indicating vacuum), especially on gauges marked with units like inches of mercury (inHg) or millibar (mbar). To read the gauge, observe where the pointer aligns with the scale.
For example, if the pointer is at the 15 inHg mark, the system has a vacuum pressure of 15 inches of mercury. If readings are in mbar, you might see values ranging from zero (atmospheric pressure) to a lower number, depending on the vacuum strength. Regularly checking and noting these readings helps maintain system efficiency.
Common Units of Measurement
Vacuum pressure gauges often use a few standard units of measurement. Familiarity with these units helps in translating readings into meaningful data for system analysis:
- Inches of Mercury (inHg): A common measurement for vacuum level in the U.S. One inHg equals 0.491 psi.
- Millibar (mbar): Widely used in scientific and industrial applications. One mbar equals 0.01 bar, or approximately 0.0145 psi.
- Pascal (Pa): This is the SI unit for pressure. It expresses a range from atmospheric pressure (1013 hPa) to lower vacuum pressures.
By keeping these units in mind, you can convert and compare readings across different gauges and systems effectively. Being aware of the system specifications helps prevent misunderstanding and aids in timely adjustments.
Tips for Accurate Readings
Accurate readings from vacuum pressure gauges enhance your ability to monitor system performance effectively.
Proper Calibration
Ensure proper calibration for precise measurements. Calibration should occur at regular intervals, typically once every six months. Use manufacturer instructions to adjust the gauge accurately. Verify calibration against a known reference gauge to confirm accuracy. If discrepancies arise, recalibrate immediately to prevent misreading.
Environmental Considerations
Consider environmental factors that impact readings. Temperature fluctuations can cause gauge inaccuracies. Aim to keep gauges in a stable temperature area, ideally between 15°C to 25°C (59°F to 77°F). Humidity also plays a role; excessive moisture can lead to corrosion. Protect gauges from moisture with suitable enclosures or moisture-resistant models. Be mindful of vibrations; they can disrupt readings. Mount your gauge securely to minimize these effects, ensuring consistent performance.
Conclusion
Mastering how to read a vacuum pressure gauge is essential for anyone working with vacuum systems. By getting familiar with the different types of gauges and their components you can ensure your equipment runs smoothly and safely.
Remember to keep an eye on calibration and environmental factors to maintain accuracy. Regular checks and adjustments will help you avoid potential issues down the line.
With practice you’ll find that reading these gauges becomes second nature. So go ahead and dive in with confidence knowing you have the tools to monitor your vacuum systems effectively.
Frequently Asked Questions
What are vacuum pressure gauges used for?
Vacuum pressure gauges are essential for measuring the pressure within a vacuum system. They help ensure safe and efficient operation of equipment by providing accurate readings, allowing users to monitor and maintain optimal performance.
What types of vacuum pressure gauges are there?
There are several types of vacuum pressure gauges, including mechanical gauges, electrical gauges, thermocouple gauges, and ionization gauges. Each type has its unique advantages, suitable for different applications and pressure ranges.
How often should vacuum pressure gauges be calibrated?
It is recommended to calibrate vacuum pressure gauges every six months. Regular calibration ensures accurate readings and maintains the effectiveness of the vacuum system, as per the manufacturer’s instructions.
What factors affect the accuracy of vacuum gauges?
Factors such as temperature stability, humidity control, and minimizing vibrations can significantly impact the accuracy of vacuum pressure gauges. Proper environmental conditions are crucial for consistent performance.
Why is understanding units of measurement important in vacuum systems?
Understanding and familiarizing yourself with common units of measurement is crucial in vacuum systems. It aids in analyzing system performance, comparing different gauges, and making necessary maintenance adjustments effectively.
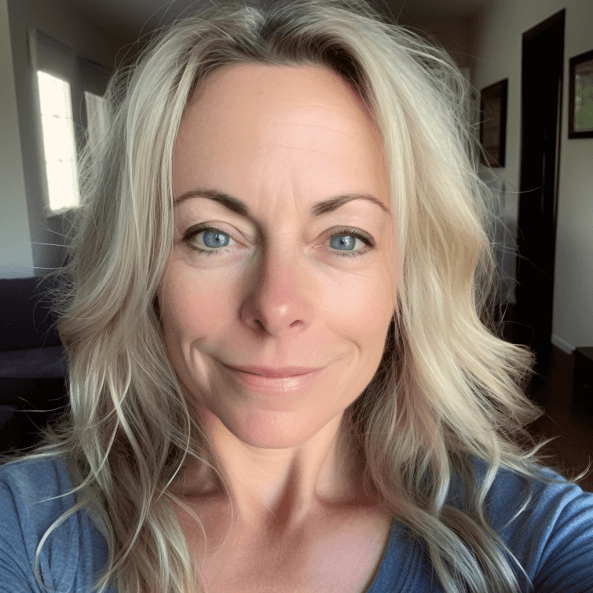