Dyson V11 Origin Cordless Vacuum, Nickel/Blue
- Versatile and cordless for whole-home deep cleaning.
Shark NV752 Rotator Powered Lift-Away TruePet Upright Vacuum with HEPA Filter, Large Dust Cup Capacity, LED Headlights, Upholstery Tool, Perfect Pet Power Brush & Crevice Tool, Bordeaux
- 2-IN-1 POWERED LIFT-AWAY TECHNOLOGY: Allows you to lift the pod away to deep-clean hard-to-reach areas, like under furniture, while the powered brushroll keeps spinning.
O-Cedar EasyWring Microfiber Spin Mop, Bucket Floor Cleaning System, Red, Gray, Standard
- HANDS-FREE WRINGING: Our exclusive mop bucket design features a built-in wringer that allows for hands-free wringing while Splash Guard keeps water splash and spray inside the bucket when wringing or when transporting the bucket from room to room
Electric Spin Scrubber for Cleaning Bathroom: Cordless Power Shower Scrubber - Electric Cleaning Brush for Tile Tub
- Multi-Surface Efficiency: Experience a deep clean across various surfaces with our Electric Spin Scrubber. Perfect for tiles, windows, bathtubs, toilets, and kitchen sinks. Effortlessly tackle dirt and grime where you need it most.
AIDEA Microfiber Cleaning Cloths, 50PK, Microfiber Towels for Cars, Premium All Purpose Car Cloth, Dusting Cloth Cleaning Rags, Absorbent Towels for SUVs, House, Kitchen, Window, 12"×12"
- Super Absorbent: Experience the excellent quality of AIDEA all-purpose microfiber cleaning cloths; made from 87% polyester and 13% polyamide; offering exceptional absorbency and quickly wicking away water to keep you dry; ideal for swiftly and safely removing dirt, grime, and liquids
Ever wondered how to tell if your vacuum system is working properly? Using a vacuum gauge can make all the difference. Whether you’re troubleshooting a home project or maintaining equipment, knowing how to read and interpret vacuum levels is crucial.
Key Takeaways
- Understanding Vacuum Gauges: Familiarize yourself with how vacuum gauges work and the importance of accurate readings for system performance.
- Types of Vacuum Gauges: Recognize the different types of vacuum gauges (Aneroid, Bourdon Tube, Capacitive, Thermocouple, Ionization) and their specific applications for effective measurement.
- Correct Setup and Usage: Follow the proper steps to set up and use a vacuum gauge, including selecting the right gauge, ensuring secure connections, and recording measurements diligently.
- Interpreting Readings: Learn how to interpret vacuum gauge readings to diagnose common issues, such as leaks or blockages, and ensure efficient operation of your vacuum system.
- Maintenance is Key: Regular maintenance, including cleaning and calibration, is essential for the accuracy and longevity of your vacuum gauge.
- Wide Applications: Understand the diverse applications of vacuum gauges across industries like food packaging, pharmaceutical production, and automotive testing for better decision-making.
Understanding Vacuum Gauges
Understanding vacuum gauges is vital for ensuring your vacuum system operates efficiently. These instruments provide crucial insight into vacuum levels, helping you troubleshoot issues and maintain your equipment effectively.
What Is a Vacuum Gauge?
A vacuum gauge measures the pressure within a vacuum system. It indicates how much air is removed from a chamber or system, providing a clear reading of the vacuum level. Different gauges display this measurement differently, typically in units like inches of mercury (inHg), millibars (mbar), or torr. Knowing how to read a vacuum gauge helps you identify whether your system achieves the desired vacuum for your application.
Types of Vacuum Gauges
Different types of vacuum gauges cater to various applications and needs. Here are the most common types:





- Aneroid Gauges:
- Measure vacuum pressure through mechanical movement.
- Simple and cost-effective, suitable for basic applications.
- Bourdon Tube Gauges:
- Use a coiled tube that straightens under pressure changes.
- Provide accurate readings for a wide range of vacuum levels.
- Capacitive Gauges:
- Detect vacuum through changes in capacitance as pressure varies.
- Offer high accuracy for low-pressure measurements and are ideal for sensitive applications.
- Thermocouple Gauges:
- Utilize a temperature sensor to measure the heat loss of a heated element in a vacuum.
- Suitable for high-vacuum applications and provide a broad measurement range.
- Ionization Gauges:
- Measure very low pressures (high vacuums) by indicating the amount of ionization in a gas.
- Necessary for vacuum systems requiring extreme precision.
Familiarizing yourself with these types enhances your understanding of which gauge is most suitable for your specific vacuum needs. Each type brings unique advantages and limitations, so select accordingly to match your application.
Importance of Using a Vacuum Gauge
Understanding the importance of a vacuum gauge enhances your efficiency when maintaining vacuum systems. These gauges provide critical insights into pressure levels, aiding in effective troubleshooting and overall maintenance.
Benefits of Accurate Measurements
Accurate measurements support optimal system performance. A vacuum gauge helps you:
- Prevent Equipment Damage: By monitoring pressure levels, you can avoid conditions that may lead to equipment failure.
- Enhance Process Control: Regular readings allow you to adjust processes for consistency and efficiency.
- Improve Energy Efficiency: Knowing exactly how much vacuum your system maintains can reduce energy consumption.
For example, in a manufacturing setting, maintaining the correct vacuum level ensures product quality and reduces waste.
Common Applications
Vacuum gauges find application across various industries. Here’s where they prove most valuable:
- Food Packaging: Ensuring airtight seals to prolong shelf life.
- Pharmaceutical Production: Maintaining sterile environments during drug manufacturing.
- Automotive Testing: Assessing fuel system performance under vacuum conditions.
Understanding these applications allows you to leverage vacuum gauges correctly, ensuring you select the right gauge for your specific needs.
How to Use a Vacuum Gauge
Using a vacuum gauge correctly ensures accurate pressure readings, which enhances system performance. Follow these steps to set up your gauge and take reliable readings.
Setting Up the Vacuum Gauge
- Select the Right Gauge: Choose a vacuum gauge that suits your application. Options include analog, digital, and capacitance gauges.
- Prepare the Connection: Ensure the gauge fits the inlet of your vacuum system. Use appropriate adapters if needed.
- Check Calibration: Confirm the gauge is calibrated properly. Refer to the manufacturer’s guidelines for calibration details.
- Connect Securely: Attach the gauge securely to avoid leaks. Tighten fittings with the appropriate tools, ensuring a snug fit.
- Power On the Gauge: If using a digital gauge, turn it on and allow it to warm up as per the manufacturer’s recommendation.
- Observe the Display: Watch for a stable reading. Analog gauges may fluctuate, so give them a moment to settle.
- Document the Pressure: Record the pressure measurements at different intervals. This data is crucial for troubleshooting and efficiency calculations.
- Evaluate Results: Compare readings with standard operating conditions. Anomalies may indicate issues requiring immediate attention.
Following these steps helps you effectively utilize a vacuum gauge, ensuring optimal operation of your vacuum system.
Interpreting Vacuum Gauge Readings
Understanding vacuum gauge readings is crucial for effective system management. These readings provide insights into pressure levels, helping diagnose issues within vacuum systems.
Understanding Measurement Units
Most vacuum gauges measure pressure in units like inches of mercury (inHg), millimeters of mercury (mmHg), or pascals (Pa). Familiarize yourself with these units to interpret the measurements correctly. For instance:
- Inches of Mercury (inHg): Commonly used in North America, with a standard atmosphere at 29.92 inHg.
- Millimeters of Mercury (mmHg): More prevalent in Europe, where a standard atmosphere is 760 mmHg.
- Pascals (Pa): A metric unit where 1 atm equals 101,325 Pa. This unit is often used in scientific applications.
Always check the unit displayed on your gauge to ensure accurate readings.
Diagnosing Issues Based on Readings
Interpreting gauge readings provides critical information for troubleshooting. Here’s how to diagnose common issues:
- Normal Readings: If your gauge indicates a steady reading within the expected range, your system functions correctly.
- Low Vacuum Pressure: Readings below optimal levels often signal leaks. Inspect seals and connections for wear or damage.
- High Vacuum Pressure: Excessively high readings may indicate blockages. Check filters, hoses, and vents to ensure they aren’t obstructed.
- Fluctuating Readings: If your gauge shows inconsistent pressure, monitor for disturbances. These could result from equipment cycling or environmental changes.
By systematically evaluating these readings, you can swiftly address potential problems in your vacuum system, ensuring optimal performance.
Maintenance and Care for Vacuum Gauges
Keeping your vacuum gauge in great shape ensures accurate readings and prolonged lifespan. Regular maintenance includes cleaning and calibration, both vital for optimal performance.
Cleaning Procedures
- Turn Off Equipment: Always switch off the equipment before cleaning to avoid accidents.
- Use a Soft Cloth: Wipe the gauge face with a soft, lint-free cloth. Avoid abrasive materials that can scratch the surface.
- Remove Residual Debris: For stubborn contaminants, use isopropyl alcohol on a cotton swab to gently clean hard-to-reach areas.
- Inspect Connections: Check for any buildup at connection points. Clean these areas to ensure proper airflow and accurate readings.
- Store Properly: After cleaning, store the vacuum gauge in a protective case or bag to prevent dust accumulation.
- Schedule Regular Calibration: Conduct calibration at least once a year, or more frequently if the gauge is used heavily.
- Use a Calibration Reference: Compare your gauge with a standard reference gauge to identify discrepancies.
- Document Readings: Keep a log of calibration results. This record helps track trends over time and identify when recalibration is necessary.
- Follow Manufacturer Guidelines: Each gauge may have specific calibration procedures. Always refer to the manufacturer’s instructions for the best practices.
- Professional Calibration Services: For best results, consider using professional calibration services, especially for critical applications where accuracy is paramount.
These practices ensure your vacuum gauge remains effective and reliable in measuring vacuum levels.
Conclusion
Using a vacuum gauge effectively can make a world of difference in your vacuum system’s performance. By understanding the readings and maintaining your gauge, you can troubleshoot issues quickly and keep everything running smoothly.
Remember to clean and calibrate your gauge regularly to ensure it’s always providing accurate information. Following these simple practices not only extends the life of your gauge but also enhances the efficiency of your entire system.
Stay proactive with your maintenance and you’ll find that managing your vacuum system becomes a much easier task. Happy gauging!
Frequently Asked Questions
What is the purpose of a vacuum gauge?
A vacuum gauge measures the pressure within a vacuum system, helping to ensure efficient operation and troubleshoot potential issues. By providing clear readings, it aids in diagnosing conditions like leaks or blockages.
What are the different types of vacuum gauges?
There are several types of vacuum gauges, including mechanical, electronic, and thermal gauges. Each type offers unique advantages suited to specific applications, such as high accuracy or broad pressure ranges.
How do I read vacuum gauge measurements?
Vacuum gauge readings are often given in units like inches of mercury (inHg) or pascals (Pa). Understanding these units helps in accurately gauging the pressure levels in a vacuum system for effective management.
Why is maintenance important for vacuum gauges?
Regular maintenance, including cleaning and calibration, is essential for vacuum gauges. It ensures accurate readings, extends the gauge’s lifespan, and maintains the system’s overall efficiency.
How often should I calibrate my vacuum gauge?
It is recommended to calibrate vacuum gauges regularly, depending on usage. Schedule calibration at least once a year or more frequently if the gauge is used extensively to ensure optimal performance and reliability.
What are best practices for cleaning vacuum gauges?
Best practices for cleaning vacuum gauges include using a soft cloth and appropriate cleaning solutions. Inspect connections and check for any blockages during the cleaning process to maintain gauge accuracy.
Should I follow manufacturer guidelines for vacuum gauge care?
Yes, following manufacturer guidelines for care and maintenance is crucial. This ensures that the gauge operates accurately and efficiently, helping you avoid costly errors in vacuum system management.
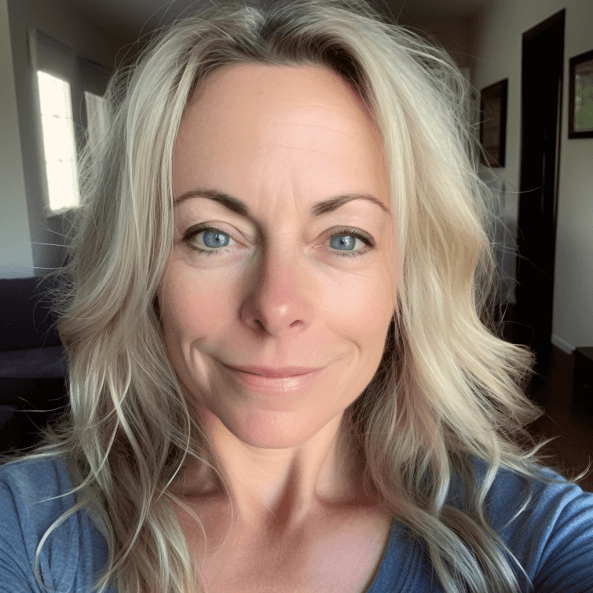