Dyson V11 Origin Cordless Vacuum, Nickel/Blue
- Versatile and cordless for whole-home deep cleaning.
Shark NV752 Rotator Powered Lift-Away TruePet Upright Vacuum with HEPA Filter, Large Dust Cup Capacity, LED Headlights, Upholstery Tool, Perfect Pet Power Brush & Crevice Tool, Bordeaux
- 2-IN-1 POWERED LIFT-AWAY TECHNOLOGY: Allows you to lift the pod away to deep-clean hard-to-reach areas, like under furniture, while the powered brushroll keeps spinning.
O-Cedar EasyWring Microfiber Spin Mop, Bucket Floor Cleaning System, Red, Gray, Standard
- HANDS-FREE WRINGING: Our exclusive mop bucket design features a built-in wringer that allows for hands-free wringing while Splash Guard keeps water splash and spray inside the bucket when wringing or when transporting the bucket from room to room
Electric Spin Scrubber for Cleaning Bathroom: Cordless Power Shower Scrubber - Electric Cleaning Brush for Tile Tub
- Multi-Surface Efficiency: Experience a deep clean across various surfaces with our Electric Spin Scrubber. Perfect for tiles, windows, bathtubs, toilets, and kitchen sinks. Effortlessly tackle dirt and grime where you need it most.
AIDEA Microfiber Cleaning Cloths, 50PK, Microfiber Towels for Cars, Premium All Purpose Car Cloth, Dusting Cloth Cleaning Rags, Absorbent Towels for SUVs, House, Kitchen, Window, 12"×12"
- Super Absorbent: Experience the excellent quality of AIDEA all-purpose microfiber cleaning cloths; made from 87% polyester and 13% polyamide; offering exceptional absorbency and quickly wicking away water to keep you dry; ideal for swiftly and safely removing dirt, grime, and liquids
Have you ever struggled with achieving a smooth, professional finish on your fiberglass projects? You’re not alone. Many DIY enthusiasts and professionals alike face challenges when working with fiberglass, especially when it comes to getting that perfect vacuum bagging technique.
This article will guide you through the process of vacuum bagging fiberglass, making it easier to achieve a flawless result. You’ll learn essential tips and tricks that can save you time and effort while ensuring your projects turn out just the way you envisioned. Whether you’re a seasoned pro or just starting, mastering this technique can elevate your work to the next level.
Key Takeaways
- Vacuum Bagging Basics: This technique involves enclosing fiberglass and resin in a sealed bag to remove air, resulting in a smoother finish and stronger bonds.
- Essential Tools: The key components needed for vacuum bagging include a vacuum pump, vacuum bag, release film, breather fabric, and sealant tape.
- Step-by-Step Process: Proper preparation and layering of the materials, along with consistent pressure monitoring, are critical for successful vacuum bagging.
- Material Selection: Choose the right type of fiberglass—cloth, mat, or chopped strand mat—based on your project requirements to ensure optimal results.
- Common Challenges: Be aware of issues like air leaks and inconsistent pressure, which can affect the quality of your fiberglass project; regular monitoring and prompt adjustments are essential.
- Practice and Environment: Gain confidence by starting with smaller projects and ensure your workspace is at an optimal temperature for resin curing.
Understanding Vacuum Bagging
Vacuum bagging is a method used to compress fiberglass materials, ensuring a strong bond and a smooth finish. The process involves enclosing the fiberglass, resin, and additional materials in a sealed plastic bag, then removing air to create a vacuum. This technique reduces the amount of trapped air and voids in the final product, resulting in a cleaner appearance and increased strength.
Key Components
- Vacuum Pump
A vacuum pump removes air from the bag, allowing you to create the pressure needed. - Vacuum Bag
A durable plastic bag designed to withstand vacuum pressure without leaking. - Release Film
This film separates the fiberglass from the bag, preventing adhesion and making removal easier. - Breather Fabric
It allows air to escape while preventing resin from blocking airflow. - Sealant Tape
Use sealant tape to ensure the vacuum bag is airtight, preventing leaks.
Steps to Vacuum Bag Fiberglass
- Prepare the Mold
Clean the mold surface. Make sure there are no residues that could interfere with the fiberglass. - Lay Down the Release Film
Place the release film over the mold. Ensure it covers all surfaces and extends beyond the edges. - Add Fiberglass Layers
Layer the fiberglass mat or cloth over the release film according to your project’s specifications. - Apply Resin
Saturate the fiberglass with resin. This can be done using a brush, roller, or infusion method. - Cover with Breather Fabric
Place the breather fabric over the resin-saturated fiberglass to allow venting. - Seal with Vacuum Bag
Drape the vacuum bag over the assembly and seal it tightly at the edges with sealant tape. - Connect the Vacuum Pump
Attach the vacuum pump to the bag. Start the pump to remove air and create a vacuum. - Monitor Pressure
Check the vacuum gauge. Maintain consistent pressure for optimal results.
Common Questions
- What type of vacuum pump should I use?
Choose a pump that matches the size of your projects, ideally one with an adequate CFM rating for efficiency. - How long should I maintain the vacuum?
Typically, holding the vacuum for 30 to 60 minutes suffices, but refer to the resin manufacturer’s guidelines. - Can I reuse vacuum bags?
Yes, vacuum bags can often be reused if they remain in good condition.
- Practice makes perfect
Try vacuum bagging on smaller projects before moving to larger ones. This builds confidence. - Temperature Matters
Ensure your workspace is at an optimal temperature for curing the resin. - Clean up spills immediately
Keep your workspace tidy to avoid contamination which affects the final product.
By mastering vacuum bagging, you can enhance the quality of your fiberglass projects, achieving results that meet professional standards.





Materials Needed
Gathering the right materials is crucial for successful vacuum bagging of fiberglass. You must have all the necessary components ready before starting your project.
Fiberglass Options
Choose from several types of fiberglass depending on your project needs:
- Fiberglass Cloth: This woven material offers flexibility and strength. It works well for thinner applications.
- Fiberglass Mat: This non-woven material provides bulk and thickness. It’s ideal for creating strong, rigid structures.
- Chopped Strand Mat: This fiberglass comes in short strands, allowing for easy application. It fills gaps well and bonds to the resin effectively.
Consider the intended use of your finished piece when selecting the fiberglass type.
Vacuum Bagging Tools
Utilize various tools to streamline the vacuum bagging process effectively:
- Vacuum Pump: Essential for creating the vacuum. Choose a pump with sufficient power for your bag size.
- Vacuum Bag: Use a durable, airtight bag designed for vacuum application. Ensure it can withstand the pressure.
- Release Film: This non-sticky film protects the fiberglass from direct contact with the bag. It allows resin flow while preventing adhesion.
- Breather Fabric: Placed beneath the vacuum bag, this fabric helps distribute the vacuum evenly and allows air to escape.
- Sealant Tape: Use this to seal the edges of your vacuum bag securely. It prevents air leaks during the vacuum process.
Assembling these materials will set you up for success in vacuum bagging fiberglass.
The Vacuum Bagging Process
The vacuum bagging process involves several crucial steps to ensure proper application and a quality finish. Each stage requires careful attention to detail for effective results.
Preparing the Fiberglass
Prepare your fiberglass material based on the project requirements. Choose the type of fiberglass—cloth, mat, or chopped strand mat—suitable for your specific application. Cut the fiberglass to size, ensuring it fits your mold without excess overlap. If applying multiple layers, plan the orientation of each layer to maximize strength.
Setting Up the Vacuum Bag
Set up the vacuum bag by placing your prepared fiberglass onto the mold. Position the release film over the fiberglass to prevent adhesion to the bag. Lay breather fabric on top to allow air to escape during vacuuming. Ensure the bag fits snugly around the mold and overlaps adequately for sealing. Use sealant tape on the edges where the bag meets the mold for a tight seal.
Sealing the Bag
Seal the vacuum bag by pressing the edges firmly against the mold and applying additional sealant tape for security. Inspect the seals for any gaps or weaknesses, as these can lead to leaks. Ensure that the top of the bag also has a solid closure, preventing any air from entering during the vacuuming process.
Vacuuming Process
Initiate the vacuuming process by connecting your vacuum pump to the bag. Turn on the pump and monitor the vacuum gauge. Aim for a pressure of around 20 inches of mercury (inHg) for optimal results. Once the desired vacuum level is reached, maintain it for the recommended period to ensure proper resin infusion and curing. Check the bag periodically for leaks throughout the vacuuming phase, and make adjustments as needed.
Common Challenges
Vacuum bagging fiberglass presents several challenges. Understanding these issues helps you achieve better results.
Air Leaks
Air leaks compromise the vacuum bag’s integrity. Check all seams and connections, ensuring they’re tightly secured with sealant tape. Pay attention to corners and edges, as these spots often let air escape. To identify leaks, use a pressure gauge or listen for hissing sounds. Repair any leaks immediately to maintain optimal pressure during the process.
Inconsistent Pressure
Inconsistent pressure can lead to uneven resin distribution. Monitor the vacuum pressure throughout the process. If you see fluctuations, adjust the vacuum pump settings. Ensure all components, including the breather fabric and release film, are properly positioned. Use a vacuum gauge to measure the pressure accurately during the infusion phase. Consistent pressure ensures a uniform bond and finish.
Conclusion
Vacuum bagging fiberglass can seem daunting at first but with the right approach it becomes a manageable task. By gathering the proper materials and tools you set yourself up for success. Remember to pay attention to detail during the setup process and monitor everything closely while vacuuming.
Don’t hesitate to troubleshoot any issues that arise along the way. With practice you’ll find that this technique not only enhances the strength of your fiberglass projects but also improves their overall appearance. Enjoy the process and take pride in the quality of your work. Happy crafting!
Frequently Asked Questions
What is vacuum bagging in fiberglass work?
Vacuum bagging is a technique used in fiberglass projects to achieve a smooth finish. It involves enclosing the fiberglass in a vacuum bag and removing air to create pressure, which helps in evenly distributing resin and compacting the materials for enhanced strength and appearance.
What materials are essential for vacuum bagging fiberglass?
Key materials include different types of fiberglass (cloth, mat, or chopped strand mat), a vacuum bag, release film, breather fabric, sealant tape, and a vacuum pump. Choosing the right materials is crucial for the success of your fiberglass project.
How do I prepare fiberglass for vacuum bagging?
Start by selecting the appropriate type of fiberglass for your project. Cut it to the required size, ensuring clean edges. Lay it out with the release film and breather fabric before sealing it in the vacuum bag to prevent sticking and allow for proper resin flow.
What are the steps involved in vacuum bagging?
The vacuum bagging process involves preparing the fiberglass, setting up the vacuum bag with release film and breather fabric, securely sealing the bag with sealant tape, and then using a vacuum pump to remove air and create necessary pressure for resin infusion and curing.
How do I troubleshoot air leaks in vacuum bagging?
To troubleshoot leaks, regularly inspect the bag for any signs of air escape. Common leak points include the seal and bag edges. Use sealant tape to repair any visible leaks and ensure the bag is properly secured to maintain consistent pressure during the process.
Why is pressure monitoring important in vacuum bagging?
Monitoring pressure is critical because inconsistent pressure can lead to uneven resin distribution, resulting in a poor-quality finish. Regular checks help maintain optimal vacuum levels, ensuring a uniform bond and achieving the desired strength and appearance in your fiberglass project.
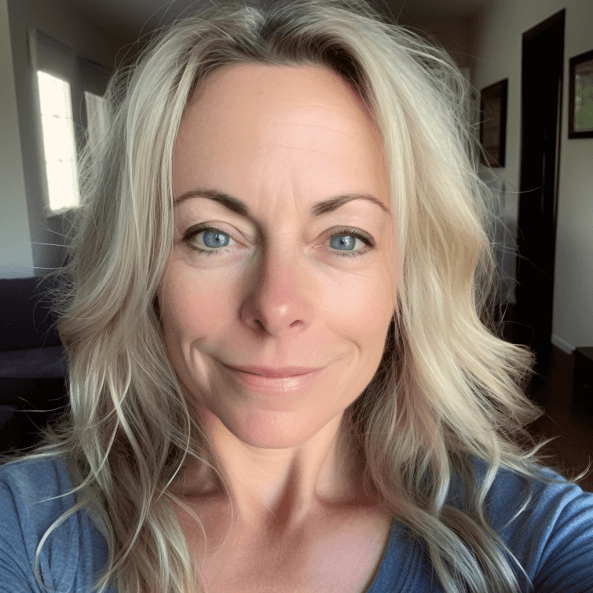