Have you ever wanted to create custom shapes or prototypes at home but didn’t know where to start? Vacuum forming might be the answer you’re looking for. This simple technique allows you to mold plastic into unique designs using everyday materials and tools.
Key Takeaways
- Understanding the Process: Vacuum forming involves heating plastic sheets, placing them over molds, and using a vacuum to shape the material effectively.
- Materials and Tools: Essential materials for home vacuum forming include polystyrene, acrylic, and PETG sheets, along with heat sources and vacuum chambers.
- Step-by-Step Procedure: Successful vacuum forming includes preparing molds, heating plastic evenly, forming the product over the mold, and allowing it to cool before removal.
- Common Challenges: Address issues like uneven thickness, air bubbles, and inadequate vacuum seals by ensuring proper heating, mold cleanliness, and secure equipment setup.
- Safety First: Always wear protective gear, ensure good ventilation, and monitor heat sources while working to avoid injuries and accidents during the process.
- Applications and Creativity: Vacuum forming can be used for prototyping, custom packaging, arts and crafts, props, and automotive parts, providing a versatile tool for creative projects.
Understanding Vacuum Forming
Vacuum forming is a straightforward technique that allows you to mold plastic into various shapes using household materials. With the right tools, you can create custom designs and prototypes easily.
What Is Vacuum Forming?
Vacuum forming involves heating a sheet of plastic until it’s soft, then placing it over a mold. A vacuum sucks the plastic down onto the mold, creating the desired shape. This process works well with materials like polystyrene, acrylic, and PETG. The key steps include:
- Heating: Use an oven or heat gun to warm the plastic until it becomes pliable.
- Molding: Place a mold on a flat surface.
- Forming: Position the heated plastic over the mold and create a vacuum to pull it down.
The whole process typically takes about 10 to 30 minutes, depending on the material and method.
Applications of Vacuum Forming
Vacuum forming has numerous applications in various fields. You can use it for:
- Prototyping: Create models for products or designs, helping you visualize the end result.
- Packaging: Design custom blister packaging for items. This approach enhances product presentation and protection.
- Arts and Crafts: Make sculptures, décor elements, or custom shapes for projects.
- Theater and Film Props: Craft realistic props that look great on stage or screen.
- Automotive Parts: Produce custom parts or enhancements for vehicles.
By understanding how to vacuum form, you’ll unlock a world of possibilities for your projects.
Materials Needed for Home Vacuum Forming
To successfully vacuum form at home, gather the right materials and tools. Here’s what you’ll need to get started.
Types of Plastic Sheets
You can choose from several types of plastic sheets for vacuum forming:
- Polystyrene: This is the most common choice. It’s easy to heat and mold. Thickness options range from 0.020 to 0.060 inches.
- Acrylic: Known for its clarity and durability, acrylic is suitable for detailed designs. Use sheets between 0.020 to 0.125 inches thick.
- PETG: Offers excellent clarity and toughness. It’s also more flexible than polystyrene. Choose thicknesses from 0.020 to 0.060 inches.
- PVC: This material is sturdy and resistant to impact, making it great for functional parts. Use sheets of 0.030 to 0.060 inches.
Tools and Equipment Required
You’ll need specific tools and equipment for effective vacuum forming:
- Heat Source: A heat gun or oven helps you heat the plastic sheets evenly. An oven is often more effective for larger sheets.
- Vacuum Chamber: This enclosure uses a vacuum pump to create suction. Alternatively, use a homemade rig with a shop vacuum.
- Molds: Create your molds from wood, metal, or 3D-printed materials. Ensure they’re smooth to guarantee a good finish.
- Thermometer: A thermometer allows you to monitor the heating process accurately.
- Safety Gear: Wear gloves and goggles for protection. Heated plastic can cause burns.
Having the right materials and tools ensures a smoother vacuum forming experience.
Step-by-Step Guide to Vacuum Forming at Home
Vacuum forming at home involves a straightforward process that anyone can follow with the right materials and tools. Here’s how to do it effectively.
Preparing the Mold
Choose a mold that represents the shape you want to create. Molds can be made from wood, foam, or thermoplastic materials. Ensure the mold is clean and free of debris. If the mold has sharp edges, sand them down to avoid damaging the plastic during the forming process. To facilitate easier removal of the formed product, apply a release agent, like petroleum jelly or a commercial mold release spray, to your mold.
Setting Up the Vacuum Forming Station
Set up a dedicated vacuum forming station in a well-ventilated area. You’ll need a heat source, such as a toaster oven or heat gun, and a vacuum chamber or vacuum cleaner attached to a custom box. Secure the mold to a sturdy base to prevent movement. Ensure your vacuum source is ready and has enough suction power to effectively pull the heated plastic over the mold.
Heating the Plastic Sheet
Select the appropriate thickness of plastic sheet based on your project’s requirements. Place the plastic sheet in the heat source. Monitor the temperature using a thermometer; different plastics require specific heating temperatures, typically between 300°F to 400°F (150°C to 200°C). Heat the sheet until it becomes pliable and starts to sag slightly. Remove it promptly to avoid overheating.
Forming the Product
Carefully position the heated plastic sheet over the prepared mold. Activate your vacuum source immediately to ensure the plastic conforms to the mold shape. Hold the plastic in place for a few seconds until the vacuum solidifies the mold. Once the forming process is complete and the plastic has cooled down, deactivate the vacuum and gently release the formed product from the mold. If necessary, trim any excess plastic for a clean finish.
Following these steps enhances your vacuum forming skills, allowing you to create custom shapes and prototypes with ease.
Common Challenges and Solutions
Vacuum forming at home can present some challenges. Understanding common issues and their solutions helps you improve your technique and results.
Troubleshooting Forming Issues
You might encounter several forming issues during vacuum forming. Here are some common problems and their solutions:
- Uneven Thickness: If the plastic isn’t evenly heated, it can cause uneven thickness. Make sure to maintain a consistent heat source and move the plastic slowly over it to ensure uniform heating.
- Bubbles or Imperfections: Air trapped between the mold and plastic can create bubbles. To prevent this, ensure your mold is smooth and clean. Apply a release agent for easier plastic removal.
- Inadequate Vacuum Seal: A weak vacuum can lead to poor forming. Check all seals and connections before starting. Making sure your vacuum chamber is airtight enhances effectiveness.
- Wrinkles in the Plastic: Wrinkles can occur if you rush the forming process. Take your time when lowering the heated plastic onto the mold. Allow it to settle gradually for the best results.
- Plastic Not Adhering to Mold: If the plastic doesn’t cling well to your mold, examine the mold surface. Use a textured surface or a mold with a slight incline to encourage adhesion.
Safety Precautions to Consider
Safety is crucial when vacuum forming at home. Follow these precautions to protect yourself:
- Use Protective Gear: Always wear safety glasses and heat-resistant gloves. This prevents burns and eye injuries when handling hot plastic.
- Ventilate Your Workspace: Ensure good airflow in your work area. Fumes from heating plastic can be harmful, so open windows or use a fan.
- Monitor Your Tools: Keep an eye on your heat source to avoid overheating. Use a thermometer to check the plastic temperature, ensuring you heat it to the appropriate level for forming.
- Secure Your Setup: Ensure that your vacuum chamber and equipment are stable. This prevents accidents during the forming process.
- Handle Materials with Care: Be cautious when dealing with heated plastic and sharp tools. Always follow manufacturer instructions for the equipment used.
By addressing these common challenges and following safety measures, you can enhance your vacuum forming experience.
Conclusion
Vacuum forming at home can be a fun and rewarding experience. With the right materials and tools you can create unique shapes and designs tailored to your needs. Don’t be afraid to experiment and learn from any challenges you encounter along the way.
Remember to prioritize safety by using protective gear and working in a well-ventilated area. With practice you’ll become more comfortable with the process and improve your skills. So gather your supplies and start creating—your next project is just a vacuum away!
Frequently Asked Questions
What is vacuum forming?
Vacuum forming is a manufacturing technique that shapes plastic sheets into custom designs by heating them and using a vacuum to pull the material over a mold. It’s commonly used for creating items like packaging, automotive parts, and displays.
What materials can be used for vacuum forming?
Suitable materials for vacuum forming include polystyrene, acrylic, PETG, and PVC. Each material has its own properties that make it ideal for different applications, ensuring versatility in your projects.
What tools are needed for vacuum forming at home?
Essential tools for vacuum forming at home include a vacuum forming machine or vacuum table, heating source, molds, and safety equipment like gloves and goggles. These tools help ensure a successful and safe forming process.
What are common challenges in vacuum forming?
Common challenges include uneven thickness, bubbles, inadequate vacuum seal, wrinkles, and issues with plastic adhering to molds. Recognizing these problems early can help you apply effective solutions during the process.
How can I prevent wrinkles when vacuum forming?
To prevent wrinkles, ensure the plastic is heated evenly and properly to the correct temperature before forming. Using a well-designed mold and securing it tightly can also help avoid wrinkles during the vacuum process.
What safety precautions should I take when vacuum forming?
Always wear protective gear like gloves and goggles, ensure good ventilation in your workspace, and regularly monitor your heating tools. Additionally, secure your setup and handle materials with care to avoid accidents.
Can vacuum forming be done without professional equipment?
Yes, vacuum forming can be done at home with basic tools and some creativity. While professional equipment makes the job easier and more efficient, many DIY setups can yield good results with proper technique and care.
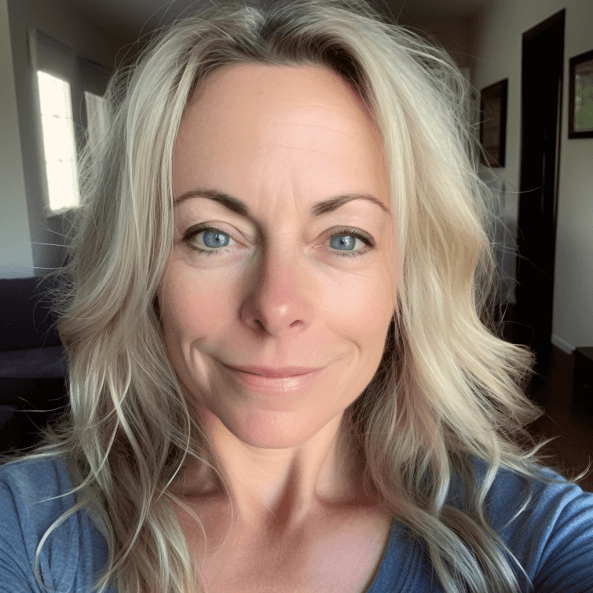