Have you ever wished you could create custom shapes or parts for your projects without spending a fortune? Vacuum forming plastic at home might be the perfect solution for you. This simple technique allows you to mold plastic into unique designs, whether for crafts, prototypes, or repairs.
Key Takeaways
- Understanding Vacuum Forming: Vacuum forming is a technique that shapes plastic by heating it and using suction to mold it over a form, making it ideal for various home projects.
- Essential Materials: Successful vacuum forming requires specific materials, including suitable thermoplastics (like ABS and PVC), a heat source, and custom molds that can withstand heat and vacuum pressure.
- Step-by-Step Process: Key steps in vacuum forming include selecting and preparing the mold, heating the plastic, creating a vacuum seal, allowing it to cool, and finally removing the formed plastic.
- Common Mistakes to Avoid: It’s crucial to avoid improper heating, inadequate mold preparation, insufficient vacuum pressure, and not allowing adequate cooling time, all of which can negatively affect your results.
- Experimentation and Adjustment: Experimenting with different plastic types and mold designs, along with maintaining accurate temperature control, can lead to better results in your vacuum forming projects.
- Documentation for Improvement: Keeping a log of your techniques and results helps track progress and refine your approach over time for future projects.
Understanding Vacuum Forming
Vacuum forming is a popular method for shaping plastic into specific designs using heat and suction. This process allows you to create custom objects or parts suited for various projects at home.
What Is Vacuum Forming?
Vacuum forming involves heating a plastic sheet until it’s pliable and then drawing it over a mold using suction. The basic steps include:
- Heating: Place the plastic sheet in a frame and heat it in an oven until it becomes soft.
- Positioning the Mold: Place the heated sheet over a mold that represents the desired shape.
- Applying Vacuum: Use a vacuum to create suction, pulling the plastic tightly over the mold.
- Cooling: Allow the plastic to cool and harden into the shape of the mold.
This technique is effective because it’s simple and requires minimal equipment. You can create items ranging from trays and containers to detailed prototypes in a matter of minutes.
Applications of Vacuum Forming
Vacuum forming serves multiple purposes across various fields:
- Prototyping: Designers use vacuum forming to create quick models of products for testing before mass production.
- Crafting: Hobbyists make custom decorations, cosplay accessories, and educational models.
- Packaging: Many packaging solutions, like clamshells or blister packs, result from vacuum forming.
- Repair Parts: This technique lets you fabricate replacement parts for older products that may no longer be in production.
Depending on your project, vacuum forming provides versatility and an economical way to produce unique plastic shapes.
Materials Needed
Gathering the right materials is essential for successful vacuum forming at home. Below are the necessary components to get started.
Types of Plastic Suitable for Vacuum Forming
- Polystyrene (PS): This lightweight plastic is popular for prototypes and simple projects. It offers good clarity and rigidity.
- Acrylonitrile Butadiene Styrene (ABS): ABS is known for its toughness and impact resistance. It’s ideal for creating durable items.
- Polypropylene (PP): This flexible plastic works well for items requiring bending or flexibility. It’s resistant to chemicals and moisture.
- Polyvinyl Chloride (PVC): PVC sheets come in various thicknesses and are suitable for both indoor and outdoor projects.
- PETG (Polyethylene Terephthalate Glycol-Modified): PETG is a clear, strong material that’s easy to work with and offers good detail reproduction.
- Oven: A conventional oven or a dedicated heat source is necessary for warming the plastic sheets.
- Vacuum Forming Machine: If unavailable, a homemade setup using a vacuum cleaner and a wooden frame can work.
- Heat Resistant Gloves: These protect your hands when handling hot plastics.
- Molds: Create or source molds from materials like wood or metal. The mold’s shape directly affects the final product.
- Sheet Plastic: Purchase sheets in one of the suitable plastic types listed above.
- Tape: Use tape to secure the plastic sheet to the mold during forming.
- Scraper or Spatula: This tool helps remove the formed plastic from the mold without damage.
- Ruler or Measuring Tape: Accurate measurements ensure precise cutting of the plastic sheets.
Gather these materials to efficiently start your vacuum forming projects.
Step-by-Step Guide to Vacuum Forming Plastic at Home
Vacuum forming plastic at home involves several clear steps. Follow this guide for a successful project.
Preparing the Mold
- Choose Your Mold Material: Use wood, metal, or an existing plastic shape. Ensure the material withstands heat and vacuum pressure.
- Create the Mold Surface: Sand the mold to make it smooth. A smooth surface results in a better finish on your plastic piece.
- Seal the Mold: Apply a release agent like petroleum jelly or a commercial mold release. This prevents the plastic from sticking.
Heating the Plastic
- Select the Right Plastic: Choose thermoplastics such as ABS, PETG, or polystyrene. Each type has specific temperature requirements.
- Preheat the Oven: Set the oven temperature between 300°F to 400°F (150°C to 200°C). Refer to the plastic manufacturer’s guidelines.
- Cut the Plastic Sheet: Trim a piece slightly larger than your mold. This ensures full coverage during forming.
- Place the Plastic: Lay the plastic sheet onto the oven rack. Keep an eye on it. The plastic needs to soften but not melt.
- Position Your Mold: Once the plastic is flexible, carefully remove it from the oven. Place the mold directly under the plastic.
- Create a Seal: Activate your vacuum forming machine or DIY setup. The suction will pull the plastic over the mold, ensuring a tight fit.
- Allow to Cool: Let the plastic cool and harden for a few minutes. This solidifies the shape and ensures durability.
- Remove the Formed Plastic: Gently pull the plastic off the mold. If you used a release agent, this should be straightforward.
By following these clear steps, you can effectively vacuum form plastic at home, creating custom shapes for your projects.
Tips for Successful Vacuum Forming
Successful vacuum forming hinges on attention to detail and technique. Follow these tips to enhance your results and streamline the process.
Common Mistakes to Avoid
- Not Heating the Plastic Enough: Heating the plastic sheet until it reaches the optimal temperature ensures it becomes pliable. If the temperature is too low, the material won’t form properly.
- Incorrect Mold Preparation: Ensure molds are smooth and free of debris. Rough surfaces can lead to imperfections in the final product.
- Inadequate Vacuum Pressure: Confirm that your vacuum source provides sufficient suction. Insufficient pressure results in a poor fit and a less precise shape.
- Ignoring Cooling Time: Allow the molded plastic enough time to cool completely. Premature removal from the mold can deform the shape.
- Experiment with Different Plastics: Try various types of plastic sheets like ABS, PVC, or PETG for different effects and applications. Each type has unique characteristics.
- Adjust Mold Design: Create molds with draft angles. This improves the ease of removing the formed part without damaging it.
- Use a Thermocouple: Utilize a thermocouple or an infrared thermometer to measure temperatures accurately. This helps maintain the right heating conditions.
- Practice Mold Creation: Start with simple shapes and gradually move to more complex designs. This builds skill and confidence over time.
- Keep a Log of Your Progress: Document your techniques, temperatures, and results. This record helps identify successful methods and areas needing improvement.
By focusing on these tips and avoiding common pitfalls, you can master vacuum forming and create high-quality plastic parts for your projects.
Conclusion
Vacuum forming at home can be a fun and rewarding experience. With just a few materials and some practice you can create custom plastic shapes that fit your needs perfectly. Don’t hesitate to experiment and tweak your techniques as you go along.
Every project is a chance to learn something new. Keeping a progress log will help you track what works and what doesn’t. So gather your supplies and let your creativity flow. You’re well on your way to mastering the art of vacuum forming!
Frequently Asked Questions
What is vacuum forming?
Vacuum forming is a manufacturing process that involves heating a plastic sheet until it’s pliable, then molding it over a shape using suction. This method allows you to create custom plastic shapes for various projects at home.
What materials can be used for vacuum forming?
You can use various thermoplastics for vacuum forming, including ABS, PETG, polystyrene, and PVC. Each plastic has unique properties, so choose one that suits your project needs and desired finish.
How do I prepare my mold for vacuum forming?
To prepare your mold, ensure it has smooth surfaces and is made from materials like wood or metal. Apply a release agent to prevent the plastic from sticking. Make sure the mold design has sufficient draft angles for easy removal.
What are the best tips for successful vacuum forming?
Key tips include heating the plastic evenly to avoid warping, ensuring strong vacuum pressure, allowing enough cooling time for durability, and experimenting with different plastics. Document your progress for better results over time.
How can I improve my vacuum forming process?
You can enhance your vacuum forming process by practicing mold creation, using thermocouples for precise temperature control, and modifying mold designs based on previous experiences. Keeping a log can also help track improvements.
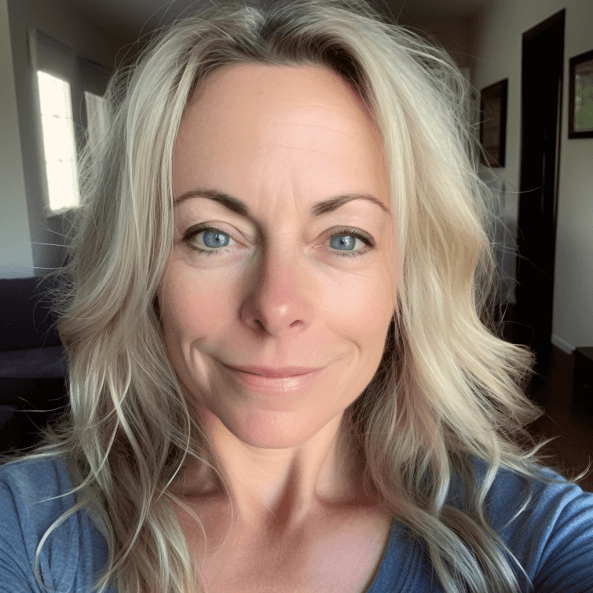