Have you ever wondered how shiny coatings are applied to everyday items like smartphones or decorative pieces? Vacuum metal deposition is the secret behind that sleek finish and durability. This technique not only enhances appearance but also improves functionality, making it essential in various industries.
Key Takeaways
- Definition and Process: Vacuum metal deposition (VMD) is a technique for applying thin metallic films to surfaces in a vacuum, enhancing both aesthetics and performance through physical vapor deposition (PVD) methods.
- Diverse Applications: VMD is utilized across multiple industries, including electronics, automotive, aerospace, consumer goods, and medical devices, improving visual appeal and functional properties.
- Key Steps: The VMD process involves creating a vacuum, heating metallic materials to vaporize them, depositing the vapor onto a substrate, and finally cooling to achieve a durable coating.
- Material Selection: Common materials used in VMD include metals like aluminum, gold, and silver, along with alloys and barrier layers, each chosen for their specific properties to enhance performance.
- Advantages: The process offers enhanced aesthetic qualities and improved durability, making products resistant to wear, corrosion, and oxidation, ultimately extending their lifespan.
- Considerations: Potential challenges include environmental concerns due to toxic materials and substantial initial setup costs, which should be weighed against long-term benefits when opting for VMD.
Overview Of Vacuum Metal Deposition
Vacuum metal deposition (VMD) is a sophisticated process that creates thin metallic films on various substrates. This method enhances both appearance and performance, essential for numerous applications.
Definition And Purpose
Vacuum metal deposition refers to the technique of depositing metal layers onto surfaces in a vacuum environment. This process typically uses physical vapor deposition (PVD) methods, where metal materials evaporate and condense on the target object. The purpose of VMD lies in producing durable, shiny coatings that improve aesthetics and functionality. It serves to enhance corrosion resistance, electrical conductivity, and barrier properties for products like electronics, automotive parts, and decorative items.
Applications In Various Industries
Vacuum metal deposition finds extensive use across several industries, including:
- Electronics: VMD coats components in smartphones, tablets, and televisions, improving their appearance and performance.
- Automotive: It enhances decorative elements and functional parts, offering both visual appeal and protection against wear.
- Aerospace: The process applies coatings that reduce friction and prevent corrosion on aircraft components, enhancing longevity.
- Consumer Goods: VMD provides a sleek, shiny finish for everyday items like household appliances and cosmetic packaging, appealing to consumer preferences.
- Medical Devices: Coatings applied through VMD ensure biocompatibility and increase the durability of instruments.
Each application benefits from the unique properties of VMD, making it a vital process in modern manufacturing.
The Vacuum Metal Deposition Process
Vacuum Metal Deposition (VMD) involves several key steps to create high-quality metallic coatings on various surfaces in a vacuum environment. This process ensures durability and enhances the visual appeal of products.
Key Steps In The Process
- Vacuum Creation: First, a vacuum chamber is evacuated to eliminate air and other contaminants. This minimizes oxidation and improves the coating quality.
- Heating the Material: Next, the metallic source materials are heated. Vaporization occurs when these materials reach high temperatures, allowing them to transition from solid to gas.
- Deposition: Then, the vaporized material condenses onto the target surface. This forms a thin metal film as the atoms collide with the substrate.
- Cooling and Solidification: After deposition, the coating cools and solidifies. This finalizes the coating process, ensuring adherence and uniform thickness.
Materials Used In Vacuum Metal Deposition
VMD utilizes various materials, each chosen for specific properties:
- Metals: Common choices include aluminum, gold, and silver. These metals enhance appearance and provide electrical conductivity.
- Alloys: Alloys like nickel-chromium may be used for increased durability and corrosion resistance.
- Barrier Layers: Materials such as titanium or chromium create barrier layers that improve adhesion and enhance protection.
Understanding these steps and materials helps clarify how VMD contributes to the performance and aesthetics of a wide range of products.
Advantages Of Vacuum Metal Deposition
Vacuum metal deposition (VMD) offers several advantages, making it a preferred choice in various industries. Understanding these benefits highlights VMD’s value in enhancing products.
Enhanced Aesthetic Qualities
VMD provides superior aesthetic qualities through the application of shiny, reflective coatings. These coatings can mimic the appearance of precious metals, elevating the product’s visual appeal. For example, consumer goods like electronics and jewelry often use aluminum or gold finishes for a premium look. The uniformity achieved through VMD ensures consistent coverage across surfaces, enhancing the overall design and attractiveness of the items.
Improved Durability And Performance
VMD significantly boosts durability and performance through the creation of robust metallic layers. These layers increase resistance to wear, corrosion, and oxidation. For instance, automotive components utilize nickel-chromium alloys to withstand harsh environments, extending the lifespan of parts. Additionally, VMD enhances electrical conductivity in electronic devices, improving their functionality and reliability. Products coated through VMD tend to have longer performance life, making them a cost-effective investment.
Challenges And Limitations
Vacuum Metal Deposition presents challenges and limitations that affect its application in various industries. Understanding these can help you make informed decisions when considering this coating method.
Environmental Concerns
Vacuum Metal Deposition processes can have environmental implications. The use of metals like chromium and cadmium raises concerns due to their toxicity. Proper safety measures and waste management practices ensure minimal environmental impact. Companies employing VMD often must adhere to strict regulations regarding emissions and disposal of materials. Look for vendors that implement eco-friendly practices in their VMD operations.
Cost Considerations
Cost is a critical factor when choosing VMD for your projects. Initial setup expenses can be significant, especially for small businesses. Equipment investment and operational costs, including energy usage, play a role in the overall budget. However, the long-term benefits, such as enhanced durability and reduced maintenance costs, may justify the investment. Evaluate both short-term and long-term financial impacts when considering VMD for your products.
Conclusion
Vacuum Metal Deposition opens up exciting possibilities for enhancing the durability and aesthetic appeal of various surfaces. By choosing the right materials and understanding the challenges involved, you can make informed decisions that align with your project needs.
As you explore VMD for your applications, keep in mind the importance of eco-friendly practices and cost considerations. With the right approach, you can enjoy the long-term benefits that VMD offers while contributing to a more sustainable future. Embrace the potential of VMD and elevate your projects to new heights.
Frequently Asked Questions
What is Vacuum Metal Deposition (VMD)?
Vacuum Metal Deposition (VMD) is a coating process that involves applying thin metallic films in a vacuum environment. This technique creates durable and visually appealing coatings, often used in various industries for enhanced protection and aesthetics.
What materials are used in VMD?
Common materials used in VMD include aluminum, gold, and nickel-chromium. Each material offers unique properties, such as appearance or durability, making them suitable for different applications.
What are barrier layers in VMD?
Barrier layers, such as titanium and chromium, are applied in VMD to enhance adhesion and provide protection. These layers improve the overall quality and longevity of the coatings.
What challenges does VMD face?
VMD faces challenges including environmental concerns due to toxicity from metals like chromium and cadmium. This highlights the need for implementing more eco-friendly practices in the coating process.
What are the cost considerations for VMD?
The cost of VMD includes significant initial setup and operational expenses. However, the long-term benefits, such as enhanced durability and reduced maintenance costs, make it a valuable investment for many projects.
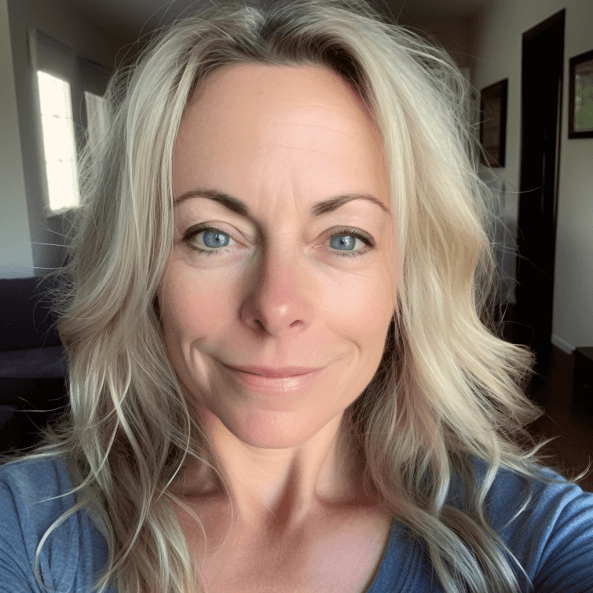