Have you ever wondered how manufacturers ensure that their products are both durable and reliable? One technique that plays a crucial role in achieving this is vacuum pressure impregnation. This method helps to enhance the performance of various materials by filling voids and preventing damage from environmental factors.
Imagine a scenario where your favorite outdoor gear starts to fail due to moisture or wear. Vacuum pressure impregnation can help extend the life of such products by creating a protective barrier. In this article, you’ll discover how this innovative process works and why it’s essential for industries ranging from aerospace to automotive. Get ready to learn how vacuum pressure impregnation can make a significant difference in product quality and longevity.
Key Takeaways
- Definition of VPI: Vacuum pressure impregnation (VPI) is a process that utilizes vacuum and pressure to fill voids in materials with resin, enhancing their durability and reliability.
- Process Steps: The VPI process involves preparing materials, applying vacuum to remove air and moisture, introducing resin, increasing pressure for deeper penetration, and curing the resin for a strong bond.
- Enhanced Durability: VPI significantly increases resistance to environmental factors such as moisture, chemicals, and temperature changes, prolonging the lifespan of products.
- Improved Performance: Materials treated with VPI exhibit better mechanical properties, leading to increased tensile strength and impact resistance, particularly beneficial in high-stress conditions.
- Diverse Applications: VPI is widely applied in industries such as aerospace, automotive, and electronics, ensuring optimal performance and longevity for critical components.
- Customization Options: Various resins can be used in the VPI process, allowing for tailored performance characteristics that meet specific product needs.
What Is Vacuum Pressure Impregnation?
Vacuum pressure impregnation (VPI) is a process that fills voids and porosities in materials using a vacuum and pressure combination. This technique enhances structural integrity by applying a liquid resin or polymer under vacuum conditions. VPI proves beneficial in numerous industries, such as aerospace, automotive, and electronics.
Process Overview
- Preparation: Clean the material to remove contaminants. Ensure it’s free from dust, oil, or moisture.
- Vacuum Application: Place the part in a vacuum chamber. Vacuum removes air and moisture from the material.
- Resin Introduction: Introduce the resin while maintaining the vacuum. The absence of air allows the resin to penetrate into the voids.
- Pressure Increase: Increase the pressure in the chamber. This forces the resin deeper into the material, filling any remaining voids.
- Curing: Allow the resin to cure. Depending on the material and resin type, curing can occur at room temperature or with heat.
Advantages of VPI
- Enhanced Durability: VPI increases resistance to environmental factors like moisture, chemicals, and temperature changes.
- Improved Performance: VPI-treated materials often demonstrate better mechanical properties, such as tensile strength and impact resistance.
- Customization: Various resins can be used to achieve specific performance characteristics tailored to your product needs.
- Aerospace Components: VPI protects critical components from extreme conditions.
- Automotive Parts: Enhanced durability in engine and transmission components leads to improved vehicle performance.
- Electronics: VPI protects circuit boards and components from moisture and corrosion, extending their lifespan.
Vacuum pressure impregnation serves as a vital process in producing high-quality, long-lasting materials. Understanding its mechanics and advantages can help you explore its applications more effectively.
The Process of Vacuum Pressure Impregnation
Understanding the vacuum pressure impregnation (VPI) process involves examining the steps taken to achieve optimal results. Each step plays a crucial role in ensuring the durability and reliability of materials.
Step 1: Preparation of the Material
Preparation ensures that the materials are ready for impregnation. You begin by cleaning the components thoroughly. Remove any debris, oil, or contaminants that could interfere with the resin’s bond. Next, inspect for cracks or defects. This inspection guarantees that any voids or spaces needing impregnation are clearly identified.
Step 2: Vacuum Application
Vacuum application creates a low-pressure environment that facilitates resin penetration. You place the prepared material in a vacuum chamber. As you lower the pressure, any existing air in the voids evacuates. This process draws the resin into the material, filling spaces that might otherwise remain void. Ensuring an optimal vacuum level is critical. Aim for about 29 inches of mercury (inHg) or lower to maximize the effectiveness of resin infiltration.
Step 3: Pressure Application
Pressure application forces the resin deep into the material’s structure. After vacuuming, you increase the chamber’s pressure, typically between 20 to 100 psi, depending on the material. This pressure pushes the resin into the previously evacuated voids. The combination of vacuum and pressure ensures complete saturation. After the process, allow sufficient curing time for the resin to harden, establishing a strong bond that enhances durability.
Through these steps, vacuum pressure impregnation effectively enhances the performance and longevity of various components across industries like aerospace and automotive.
Benefits of Vacuum Pressure Impregnation
Vacuum pressure impregnation (VPI) offers significant advantages for various industries by enhancing the performance and longevity of materials. Here are the main benefits:
Enhanced Material Durability
VPI fills voids and permeates porous materials with resin. This process strengthens the structure of components, reducing defects. For example, in the aerospace industry, VPI-treated parts exhibit improved resistance to fatigue and wear. The result is enhanced durability, which prolongs the life of components in demanding environments.
Improved Performance Characteristics
VPI enhances the performance of materials through better mechanical properties. Treatments can lead to increased tensile strength, improved thermal stability, and enhanced resistance to chemicals. For instance, automotive components that undergo VPI show better performance under high-stress conditions, leading to fewer failures during operation. With VPI, products can meet or exceed industry performance standards while ensuring reliability and efficiency.
Applications of Vacuum Pressure Impregnation
Vacuum pressure impregnation (VPI) plays a crucial role in various industries by enhancing material properties and ensuring product longevity.
Aerospace Industry
VPI is vital in the aerospace industry. High-performance components, such as turbine blades and structural parts, benefit greatly from VPI treatment. This process reduces microscopic gaps within materials, thus increasing their strength and fatigue resistance. For example, VPI-treated composites exhibit higher tensile strength, essential for components exposed to extreme conditions like high temperatures and pressures. Additionally, VPI improves thermal conductivity, which is critical for heat management in aerospace systems.
Automotive Industry
The automotive industry uses VPI to enhance the performance of engine components, such as cylinder heads and pump housings. By impregnating these components with resin, manufacturers increase their resistance to wear and corrosion. For instance, VPI-treated aluminum castings experience improved longevity and reduced failure rates, resulting in more reliable vehicles. Moreover, this process contributes to weight reduction, which is crucial for fuel efficiency and overall vehicle performance.
Conclusion
Vacuum pressure impregnation is a game-changer for various industries. By enhancing the durability and reliability of components you rely on every day it ensures better performance and longevity. Whether you’re in aerospace or automotive VPI can significantly reduce failure rates and improve efficiency.
As technology continues to evolve the benefits of VPI will likely expand even further. Embracing this innovative process could be the key to unlocking new levels of performance in your products. So if you’re looking to boost the reliability of your components consider the advantages that vacuum pressure impregnation brings to the table.
Frequently Asked Questions
What is vacuum pressure impregnation (VPI)?
VPI is a process that fills voids in materials with resin under vacuum and pressure conditions. This enhances the durability, reliability, and overall performance of components used in various industries.
How does the VPI process work?
The VPI process involves preparing materials, applying a vacuum to eliminate air, and then applying pressure to force resin into the voids. This results in improved structural integrity and other performance benefits.
What industries benefit from VPI?
Industries such as aerospace and automotive greatly benefit from VPI. Aerospace components, like turbine blades, see increased strength, while automotive parts, like cylinder heads, exhibit enhanced wear resistance.
How does VPI improve aerospace components?
VPI-treated aerospace components gain improved strength, fatigue resistance, and thermal conductivity, making them more reliable in high-stress environments and enhancing overall system performance.
In what ways does VPI enhance automotive parts?
In automotive applications, VPI increases the wear and corrosion resistance of engine components, like cylinder heads. This leads to better longevity, reduced failure rates, and improved fuel efficiency.
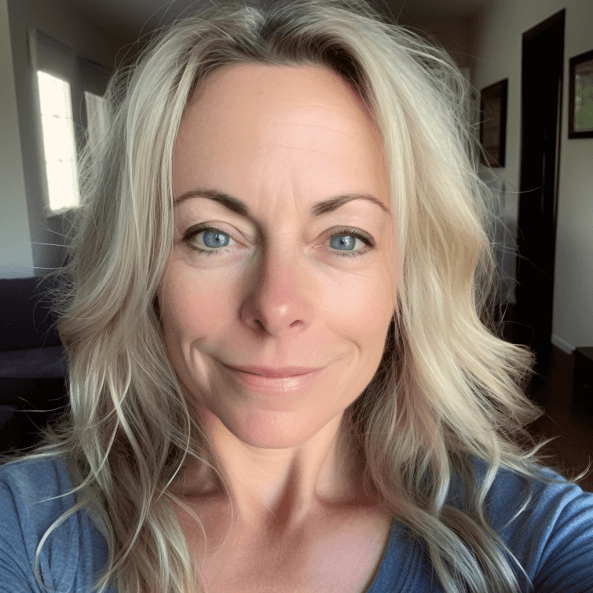