Have you ever wondered what happens when a system reaches deep vacuum? Picture this: a sealed container where air is almost completely removed. It sounds simple, but the effects can be fascinating and complex. Understanding deep vacuum systems is crucial in various fields like manufacturing, science, and even space exploration.
Key Takeaways
- Definition of Deep Vacuum: Deep vacuum refers to a state of very low pressure, typically below 1 mTorr, essential for various scientific and industrial applications.
- Importance of Achieving Deep Vacuum: It prevents contamination, enhances chemical reaction performance, enables precision measurements, and simulates space conditions.
- Applications Across Fields: Deep vacuum systems are crucial in scientific research, semiconductor manufacturing, food preservation, and pharmaceutical production.
- Challenges in Maintenance: Regular maintenance is vital to ensure the integrity of deep vacuum systems, addressing issues like seal wear, component cleaning, and filter replacement.
- Measurement Accuracy: Precise instrument calibration is essential for reliable readings in deep vacuum environments, where standard sensors may not suffice.
- Benefits of Deep Vacuum Operation: Enhanced reaction rates, improved material properties, and better control over processes lead to higher efficiency and product quality.
Understanding Deep Vacuum Systems
Deep vacuum systems remove air to create an environment with very low pressure, essential for various applications in manufacturing, science, and space exploration.
Definition of Deep Vacuum
Deep vacuum refers to a state where the pressure in a sealed environment drops significantly below atmospheric pressure, typically measured in millitorrs (mTorr) or pascals (Pa). For reference, a standard atmospheric pressure is about 760 torr. In deep vacuum conditions, the pressure usually falls below 1 mTorr, meaning that only a tiny fraction of air molecules remains. Systems achieving this state include vacuum chambers, electron microscopes, and certain types of scientific instruments.
Importance of Achieving Deep Vacuum
Achieving deep vacuum is crucial for several reasons:
- Contamination Prevention: Low pressure reduces the presence of particulates and gases that can contaminate sensitive processes or experiments.
- Enhanced Performance: In chemical reactions, lower pressure can improve yields and stability of products.
- Precision Measurements: Instruments like mass spectrometers produce more accurate data when run in deep vacuum.
- Space Simulation: Testing equipment for space applications requires deep vacuum to mimic conditions found in outer space.
In practical terms, achieving deep vacuum often involves a combination of mechanical pumps and diffusion pumps that work together to remove air efficiently. Use gauges to monitor pressure levels and ensure consistent performance.
Applications of Deep Vacuum
Deep vacuum systems play a crucial role in various fields, contributing to advancements in scientific research and industrial processes.
Scientific Research
Deep vacuum environments enable precise experiments in scientific research. For example, in physics, researchers perform experiments on atomic interactions without the interference of air molecules. This clarity allows accurate observations and measurements. Laboratories use deep vacuum chambers in fields like material science and chemistry for activities such as:
- Surface Analysis: Techniques like Auger Electron Spectroscopy (AES) require deep vacuum to prevent contamination by atmospheric gases, ensuring accurate surface composition analysis.
- Chemical Reactions: Many chemical reactions occur more effectively under a vacuum, reducing byproducts and enhancing yield.
- Cryogenics: Deep vacuum systems help maintain low temperatures, crucial for studying materials at superconducting states.
Industrial Processes
Industries depend on deep vacuum for efficient manufacturing processes. Some common applications include:
- Semiconductor Manufacturing: Deep vacuum is essential during the deposition of thin films in semiconductor fabrication, enhancing layer quality and reducing defects.
- Food Preservation: In vacuum packaging, air removal prolongs shelf life by minimizing oxidation and microbial growth.
- Pharmaceutical Production: Deep vacuum aids in lyophilization, a process that removes moisture from drug formulations, ensuring stability and shelf life.
By harnessing the power of deep vacuum, both scientific research and industrial processes achieve superior results and maintain operational efficiency.
Challenges Faced in Deep Vacuum Systems
Deep vacuum systems present unique challenges that impact their efficiency and effectiveness. Two primary concerns are maintenance issues and measurement accuracy.
Maintenance Issues
Maintaining deep vacuum systems requires regular inspections and upkeep. Components wear down over time, and leaks can occur, which lead to compromised vacuum conditions. Routine maintenance tasks include:
- Inspecting Seals: Ensure all seals are intact and in good condition to prevent air ingress.
- Cleaning Components: Remove contaminants from pumps and other parts to maintain performance.
- Replacing Filters: Keep filters clean to avoid blockages that can affect vacuum pressure.
- Monitoring Pump Operations: Regularly check pump functionality to ensure optimal operation.
Ignoring maintenance can lead to costly downtime and inefficient processes. Utilizing a maintenance schedule helps in proactively addressing potential issues.
Measurement Accuracy
Measurement accuracy in deep vacuum systems is critical for reliable results. Instruments must provide precise readings to ensure effective operation. Challenges include:
- Calibration of Instruments: Regularly calibrate gauges and sensors to maintain accuracy. Incorrect readings can lead to major operational errors.
- Temperature Fluctuations: Temperature changes can affect pressure readings, leading to misinterpretations of vacuum levels.
- Low Pressure Sensitivity: Instruments must have sensitivity to low pressure levels, as standard sensors may not perform adequately in deep vacuum conditions.
Utilizing high-quality instruments designed for deep vacuum applications is essential. Analyzing measurements carefully ensures that experiments and processes yield accurate and reliable results.
Benefits of Operating in Deep Vacuum
Operating in a deep vacuum offers significant advantages across various industries. Low-pressure environments create unique conditions that enhance processes and improve outcomes.
Enhanced Reaction Rates
Deep vacuum systems facilitate faster and more efficient chemical reactions. In the absence of air, reactions proceed with fewer obstacles. For instance, in chemical synthesis, using a deep vacuum can accelerate reaction rates by preventing unwanted side reactions and allowing for precise control over reaction conditions. Benefits include:
- Reduced Contaminants: Lack of atmospheric gases minimizes contamination risk during reactions.
- Increased Yield: Higher reaction rates can lead to greater product yields, especially in pharmaceuticals and specialty chemicals.
- Controlled Environments: Precise control over temperature and pressure can optimize reaction conditions.
Improved Material Properties
Materials treated under deep vacuum conditions often exhibit superior properties compared to those processed in normal atmospheric pressure. Deep vacuum applications commonly enhance:
- Purity: Evaporation and deposition processes in a vacuum eliminate impurities from materials, resulting in higher quality products.
- Density and Strength: Materials processed in a vacuum may display improved density and strength due to the elimination of voids and defects typically found in conventionally produced materials.
- Electrical Conductivity: In semiconductor manufacturing, vacuum processing leads to improved electrical properties by reducing defects that affect functionality.
These benefits of deep vacuum operation enable you to achieve higher efficiency and quality in various applications, strengthening your competitive edge in the marketplace.
Conclusion
Understanding deep vacuum systems is key to unlocking their potential in various industries. By creating low-pressure environments you can significantly improve the quality and efficiency of your processes.
While challenges exist maintaining these systems and ensuring measurement accuracy you’ll find that the benefits greatly outweigh the drawbacks. Enhanced material properties and increased yield can give you a competitive edge.
Embracing deep vacuum technology means you’re not just keeping up with industry standards but pushing the boundaries of what’s possible. So whether you’re in manufacturing or exploring new frontiers in science remember that deep vacuum can transform your operations for the better.
Frequently Asked Questions
What are deep vacuum systems used for?
Deep vacuum systems are essential in industries like manufacturing, science, and space exploration. They create low-pressure environments that enable precise control over processes, leading to improved material properties and enhanced reaction rates.
Why is maintenance important for deep vacuum systems?
Maintenance is crucial for deep vacuum systems to ensure they operate efficiently and reliably. Regular upkeep helps prevent leaks and failures, maintains measurement accuracy, and prolongs the lifespan of the equipment, ultimately enhancing performance.
How do deep vacuum systems improve material quality?
Operating in deep vacuum conditions can enhance material properties such as purity, density, strength, and electrical conductivity. This leads to higher efficiency and quality in applications, increasing market competitiveness.
What challenges do deep vacuum systems face?
Deep vacuum systems face challenges like maintenance issues, the need for accurate measurements, and potential contamination risks. Addressing these challenges is vital for optimal performance and reliability in various applications.
How do deep vacuum systems benefit the manufacturing process?
Deep vacuum systems improve reaction rates and reduce contaminants during manufacturing. This results in higher yield and quality of products, making processes more efficient and cost-effective, ultimately benefiting the bottom line.
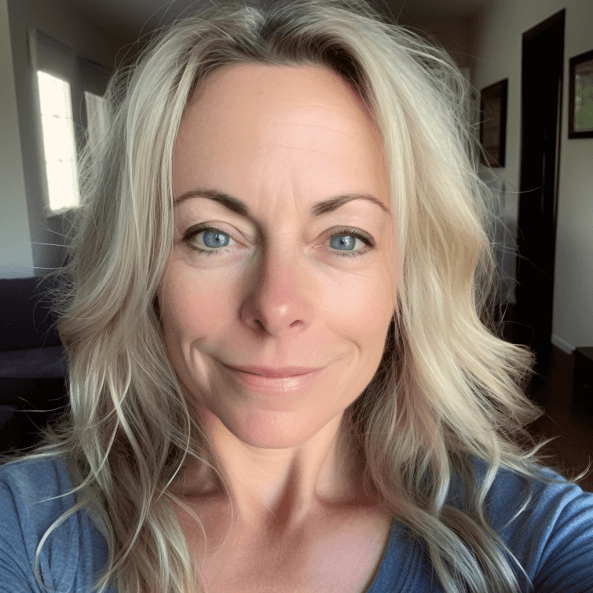