Have you ever wondered what the lowest vacuum reading means and how it affects your work? Whether you’re troubleshooting a system or optimizing equipment, understanding vacuum readings can save you time and frustration.
Imagine you’re trying to diagnose a performance issue in a vacuum system. Knowing which reading represents the lowest vacuum can be the key to pinpointing the problem. This article will guide you through the essentials of vacuum measurements, helping you make sense of the numbers and improve your processes.
Key Takeaways
- Understanding Vacuum Readings: Vacuum readings indicate pressure levels in a vacuum system, where lower values signify a higher vacuum, crucial for diagnosing system performance.
- Importance of Accurate Measurements: Monitoring vacuum readings aids in diagnosing issues, optimizing performance, and preventing equipment damage, ensuring systems operate efficiently.
- Types of Vacuum Gauges: Mechanical gauges (Bourdon tube and diaphragm) offer simplicity, while electronic gauges (capacitive, piezoelectric, and thermocouple) provide higher accuracy and real-time monitoring.
- Factors Influencing Readings: Environmental conditions, such as temperature and humidity, and proper equipment calibration significantly affect the reliability of vacuum measurements.
- Identifying Lowest Vacuum Readings: Gather data, establish baselines, monitor trends, and use multiple gauges to accurately identify the lowest vacuum readings for effective troubleshooting and maintenance.
- Practical Applications: Low vacuum readings are critical in various industries, including manufacturing and scientific research, for maintaining optimal conditions and ensuring consistent results.
Understanding Vacuum Readings
Understanding vacuum readings aids in diagnosing system performance and optimizing equipment. Vacuum readings indicate pressure levels in a system, which can help identify issues that require attention.
Definition of Vacuum Readings
Vacuum readings measure the pressure in a vacuum system, usually expressed in units like millibar (mbar), inches of mercury (inHg), or pascals (Pa). A vacuum occurs when the pressure is lower than atmospheric pressure. The reading represents how effectively a system can remove air or gas. Lower values indicate a higher vacuum. For example, a reading of 29.9 inHg shows a near-perfect vacuum, while a reading of 14.7 inHg indicates atmospheric pressure.
Importance of Vacuum Measurements
Vacuum measurements play a critical role in evaluating system efficiency and performance. Accurate readings ensure systems operate within optimal pressure ranges. Here are some practical benefits:
- Diagnosing Issues: When a vacuum reading is lower than expected, it signals potential leaks or other problems.
- Optimizing Performance: Correct readings help adjust equipment settings for better efficiency.
- Preventing Damage: Monitoring vacuum levels can prevent equipment failure due to excessive pressure changes.
Using vacuum gauges can provide real-time data, allowing you to address problems promptly. Regularly checking these measurements allows for more controlled operations and extends equipment lifespan.
Types of Vacuum Gauges
Understanding different types of vacuum gauges helps you choose the right tool for measuring low vacuum readings. Two primary categories of vacuum gauges are mechanical gauges and electronic gauges.
Mechanical Gauges
Mechanical gauges operate based on physical properties, measuring pressure changes through mechanical movements. These gauges include Bourdon tube gauges and diaphragm gauges, which indicate vacuum levels through needle movement on a dial.
- Bourdon Tube Gauges: These gauges use a curved tube that straightens out when a vacuum forms, making the needle move to show the pressure reading.
- Diaphragm Gauges: These employ a flexible diaphragm that deforms under pressure changes, providing a measurement through a connected needle.
Mechanical gauges are generally simple to use, often requiring minimal calibration. However, lower-range readings can be less accurate than electronic gauges, particularly in high-precision applications.
Electronic Gauges
Electronic gauges utilize sensors to provide precise measurements of pressure and vacuum levels. They come in different forms, including capacitive, piezoelectric, and thermocouple gauges.
- Capacitive Gauges: These rely on a capacitor that changes capacitance with pressure fluctuations, displaying readings on a digital display.
- Piezoelectric Gauges: These use piezoelectric crystals, generating an electric charge when subjected to pressure changes, yielding accurate measurements.
- Thermocouple Gauges: These measure temperature changes in a controlled environment to ascertain vacuum levels, translating thermal data into pressure readings.
Electronic gauges generally offer higher accuracy and better responsiveness under varying conditions. They may include features like data logging and real-time monitoring, enhancing your understanding of vacuum levels in practical applications.
Factors Influencing Vacuum Readings
Understanding the factors influencing vacuum readings can enhance your ability to troubleshoot and optimize equipment performance effectively.
Environmental Conditions
Environmental conditions play a significant role in vacuum readings. Temperature variations can affect gas behavior and measurement accuracy. For example, higher temperatures may increase gas kinetic energy, leading to higher pressure readings. Humidity levels can introduce additional moisture into the system, affecting vacuum quality. Always monitor ambient conditions to ensure reliable vacuum measurement.
Equipment Calibration
Equipment calibration is crucial for accurate vacuum readings. Regular calibration helps maintain the precision of vacuum gauges. An uncalibrated gauge can provide misleading data, potentially leading to operational issues. You should check calibration against known standards at least once a year or before critical measurements. Use manufacturer guidelines for specific calibration procedures.
Analyzing Vacuum Readings
Understanding vacuum readings involves careful analysis to determine the efficiency of your system. This section focuses on how to compare readings and identify the lowest vacuum readings for optimal performance.
Comparing Different Readings
Comparing different vacuum readings allows you to assess equipment performance accurately. Record data from multiple gauges, noting both mechanical and electronic types. Evaluate these key comparisons:
- Absolute Pressure vs. Gauge Pressure: Remember, absolute pressure includes atmospheric pressure, while gauge pressure measures pressure relative to atmospheric conditions.
- Different Gauge Types: Compare readings from mechanical gauges like Bourdon tubes with electronic gauges like capacitive sensors. Mechanical gauges may provide a quick visual reference, but electronic gauges offer greater precision.
- Temperature Influence: Analyze how temperature variations impact the readings. Higher temperatures can lead to lower vacuum levels due to gas expansion.
Identifying the Lowest Vacuum Reading
Identifying the lowest vacuum reading is crucial for system diagnostics. Follow these steps to ensure accuracy:
- Gather Data: Collect vacuum readings over time, noting variations in readings during different operations.
- Establish Baselines: Set baseline readings under stable operating conditions. These values serve as a reference point for identifying abnormal drops.
- Monitor Trends: Track the lowest readings over time. Sudden drops may indicate issues such as leaks or equipment inefficiencies.
- Use Multiple Gauges: Verify the lowest readings by cross-referencing with different gauges. This step reduces chances of errors due to gauge malfunction.
By using these methods, you can accurately identify the lowest vacuum reading, leading to better equipment performance and maintenance.
Practical Applications of Low Vacuum Readings
Understanding low vacuum readings proves essential across various fields. These readings play a significant role in industrial applications and scientific research.
Industrial Uses
Low vacuum readings help maintain optimal performance in manufacturing and processing environments. In semiconductor fabrication, for instance, precise vacuum levels ensure defect-free products. Vacuum systems also support packaging processes by removing air to enhance shelf life. Operators can monitor readings using gauges, ensuring they meet specifications for safety and efficiency. Regular maintenance checks allow for quick identification of leaks or failures, reducing downtime and preventing costly production issues.
Scientific Research
Low vacuum readings are integral in scientific experimentation and analysis. In laboratories, researchers use vacuum systems to create controlled environments for sensitive experiments. For example, mass spectrometry instruments require specific vacuum levels to analyze chemical compositions accurately. Accurate measurements allow scientists to replicate experiments and validate results. Tracking low vacuum readings also aids in the preservation of samples by minimizing contamination. Utilizing calibration procedures and proper monitoring equipment enhances reliability in research outcomes.
Conclusion
Understanding which reading represents the lowest vacuum level is vital for your equipment’s performance. By familiarizing yourself with different types of vacuum gauges and their readings you can better troubleshoot issues and optimize processes. Remember that factors like temperature and environmental conditions can affect these readings.
Whether you’re in an industrial setting or conducting scientific research accurate vacuum measurements can make all the difference. Keeping your equipment calibrated and properly monitored ensures reliability and helps you achieve the best results. Embrace the knowledge of vacuum readings to enhance your work and prevent potential problems down the line.
Frequently Asked Questions
What do vacuum readings indicate?
Vacuum readings measure the pressure levels in a system. Lower values signify higher vacuum levels, helping identify issues in equipment performance.
Why are vacuum readings important in troubleshooting?
They help detect problems like leaks or inefficiencies within equipment, enabling timely maintenance and optimization for better performance.
What types of vacuum gauges are available?
Common types include mechanical gauges like Bourdon tubes and electronic gauges such as capacitive sensors, each offering different functionalities and accuracy levels.
What factors influence vacuum readings?
Factors include temperature variations and environmental conditions. Calibration against known standards is essential for accurate and reliable readings.
How are low vacuum readings applied in industry?
Low vacuum readings are vital for preventing production issues, maintaining optimal equipment performance, and ensuring reliable operational processes.
Why are vacuum measurements crucial in scientific research?
Accurate vacuum measurements are essential for creating controlled environments, conducting sensitive experiments, and preserving research samples effectively.
How can I ensure accurate vacuum readings?
Regular calibration of equipment against recognized standards, along with proper monitoring, is key to obtaining reliable vacuum measurements.
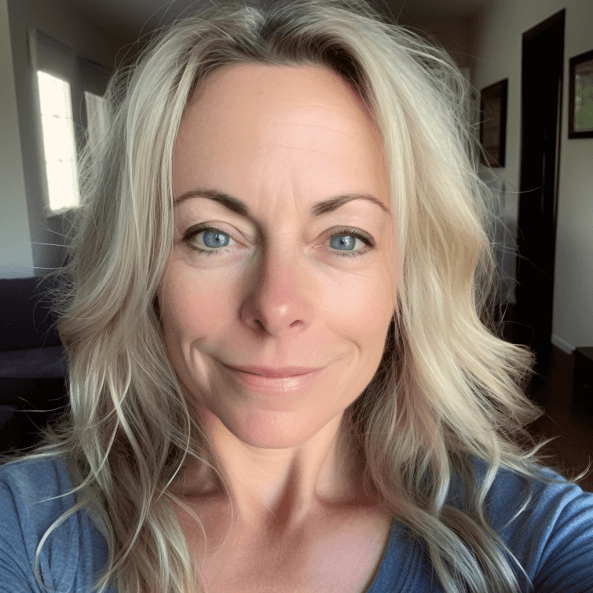