Dyson V11 Origin Cordless Vacuum, Nickel/Blue
- Versatile and cordless for whole-home deep cleaning.
Shark NV752 Rotator Powered Lift-Away TruePet Upright Vacuum with HEPA Filter, Large Dust Cup Capacity, LED Headlights, Upholstery Tool, Perfect Pet Power Brush & Crevice Tool, Bordeaux
- 2-IN-1 POWERED LIFT-AWAY TECHNOLOGY: Allows you to lift the pod away to deep-clean hard-to-reach areas, like under furniture, while the powered brushroll keeps spinning.
O-Cedar EasyWring Microfiber Spin Mop, Bucket Floor Cleaning System, Red, Gray, Standard
- HANDS-FREE WRINGING: Our exclusive mop bucket design features a built-in wringer that allows for hands-free wringing while Splash Guard keeps water splash and spray inside the bucket when wringing or when transporting the bucket from room to room
Electric Spin Scrubber for Cleaning Bathroom: Cordless Power Shower Scrubber - Electric Cleaning Brush for Tile Tub
- Multi-Surface Efficiency: Experience a deep clean across various surfaces with our Electric Spin Scrubber. Perfect for tiles, windows, bathtubs, toilets, and kitchen sinks. Effortlessly tackle dirt and grime where you need it most.
AIDEA Microfiber Cleaning Cloths, 50PK, Microfiber Towels for Cars, Premium All Purpose Car Cloth, Dusting Cloth Cleaning Rags, Absorbent Towels for SUVs, House, Kitchen, Window, 12"×12"
- Super Absorbent: Experience the excellent quality of AIDEA all-purpose microfiber cleaning cloths; made from 87% polyester and 13% polyamide; offering exceptional absorbency and quickly wicking away water to keep you dry; ideal for swiftly and safely removing dirt, grime, and liquids
Have you ever wished you could create custom shapes and designs out of plastic with ease? Whether you’re a hobbyist looking to make unique crafts or a professional needing prototypes, vacuum forming can be your go-to technique.
Imagine transforming flat sheets of plastic into stunning three-dimensional objects in just a few simple steps. This article will guide you through the vacuum forming process, helping you understand the tools and techniques needed to achieve great results. By the end, you’ll be ready to tackle your own projects and bring your creative ideas to life.
Key Takeaways
- Understanding the Process: Vacuum forming is a simple yet effective method for transforming flat plastic sheets into intricate three-dimensional shapes.
- Essential Materials: Key materials for vacuum forming include acrylic, polycarbonate, PVC, HIPS, and PETG, each offering unique benefits for various applications.
- Necessary Tools: Utilize a vacuum forming machine, heat source, quality molds, and a vacuum pump to streamline the vacuum forming process.
- Step-by-Step Technique: The vacuum forming process involves preparing a mold, heating the plastic, forming it over the mold, cooling, and finishing the final product.
- Wide Applications: Vacuum forming is extensively used in packaging, prototyping, and model making, making it a versatile technique for both professionals and hobbyists.
- Safety First: Always prioritize safety by using heat-resistant gloves and goggles when working with heated materials and equipment.
Understanding Vacuum Forming
Vacuum forming is a straightforward technique that transforms flat plastic sheets into intricate shapes. It’s popular among hobbyists and professionals due to its ease of use and efficiency in creating custom designs.
What Is Vacuum Forming?
Vacuum forming involves molding plastic by heating it until soft and then shaping it over a mold using suction. This process creates three-dimensional objects with sharp details and smooth finishes. Common applications include packaging, prototypes, and creative projects.





How Does Vacuum Forming Work?
Vacuum forming follows a simple sequence of steps:
- Select Your Material: Choose a plastic sheet suitable for your project. Common materials include acrylic and polystyrene.
- Create the Mold: Build a mold from durable materials like wood or metal. Ensure the mold has smooth edges and the desired shape.
- Heat the Plastic: Use a heat source to warm the plastic sheet until it becomes pliable. Avoid overheating, as it can distort the material.
- Form the Plastic: Position the heated plastic sheet over the mold. Activate the vacuum to draw the plastic tightly against the mold’s surface.
- Cool and Remove: Allow the formed plastic to cool before removing it from the mold. This step ensures the shape holds.
- Finish the Product: Trim excess plastic and add any desired details or modifications.
Utilizing the right tools and following these steps leads to successful vacuum forming projects.
Materials Required for Vacuum Forming
To successfully vacuum form plastic, gather a few essential materials. The right choices enhance the ease and quality of your projects.
Types of Plastic Suitable for Vacuum Forming
- Acrylic (PMMA): Acrylic is lightweight and offers excellent clarity. Its durability and resistance to UV light make it ideal for outdoor applications.
- Polycarbonate: This plastic provides high impact resistance and heat stability. It’s suitable for applications needing strong, shatter-resistant designs.
- PVC: PVC is affordable and easy to work with. It’s commonly used for packaging and creating decorative items.
- HIPS (High-Impact Polystyrene): HIPS is flexible and has good dimensional stability. It’s popular in model-making and toy production.
- PETG: This material combines rigidity with impact resistance. PETG works well for displays and protective covers.
- Vacuum Forming Machine: A dedicated machine streamlines the entire process. Look for features that suit your project dimensions.
- Heat Source: A heat gun or oven works effectively to warm plastic sheets before forming. Ensure the source evenly distributes heat.
- Molds: Create molds from materials like wood, metal, or 3D prints. Make sure they’re smooth to achieve a polished finish.
- Vacuum Pump: A quality vacuum pump generates sufficient suction to form the clear plastic over the mold.
- Clamps and Frames: These hold plastic sheets securely during the heating and forming phases, preventing shifting.
- Safety Gear: Always wear heat-resistant gloves and safety goggles while handling heated materials and equipment.
With the right materials and tools, achieving great results in vacuum forming becomes straightforward. Prepare well, and your projects will shine.
The Vacuum Forming Process
The vacuum forming process involves several key steps that lead to the creation of precise plastic shapes. Understanding each step helps ensure successful outcomes.
Preparing the Template
You start with a mold or template, which can be made from wood, aluminum, or 3D-printed materials. Ensure the template has smooth surfaces and desired shapes. You might use a CNC machine for intricate designs. Apply a release agent to the mold to prevent the formed plastic from sticking.
Heating the Plastic
Select a suitable plastic sheet and place it in the heating area of the vacuum forming machine. Heat the plastic evenly until it becomes soft and pliable, typically at a temperature range of 250°F to 400°F, depending on the material type. Avoid overheating to prevent burning or warping.
Forming the Plastic
Once the plastic is heated, position the template beneath. Activate the vacuum pump to create suction, drawing the plastic tightly over the mold. The vacuum should eliminate air pockets to ensure complete contact. Hold the plastic in place for a few seconds to allow it to take shape.
Cooling and Finishing
After forming, allow the plastic to cool and harden, usually for a few minutes. Remove the formed part from the mold carefully. You may need to trim excess material or smooth edges using cutting tools or sanders. Finally, inspect the finished product for any defects, making any necessary adjustments before use.
Common Applications of Vacuum Forming
Vacuum forming offers a wide array of applications across several industries. This versatility makes it a popular choice for both commercial and personal projects.
Packaging Solutions
Vacuum forming plays a crucial role in packaging solutions. It creates custom trays, clamshells, and blisters that securely hold products. These packaging types ensure items remain protected during shipping and display. For example, electronics, food, and cosmetics often use vacuum-formed packaging for optimal presentation and safety.
Prototyping and Model Making
Prototyping and model making benefit significantly from vacuum forming. This technique allows you to quickly produce prototypes for testing designs. For instance, architectural models or automotive parts can be formed in a fraction of the time compared to traditional methods. Alongside speed, the cost-effectiveness enhances its appeal. Using this method, you can create detailed visuals, allowing for a better understanding of the final product before mass production.
Conclusion
Vacuum forming opens up a world of creativity and practicality for your projects. With just a few materials and some basic equipment you can produce stunning plastic shapes that meet your needs. Whether you’re crafting prototypes or designing packaging vacuum forming allows you to bring your ideas to life with ease.
Don’t forget to experiment and refine your technique as you go. Each project is a chance to learn and improve. So gather your supplies and start creating. You might be surprised at what you can achieve with a little practice and imagination. Happy vacuum forming!
Frequently Asked Questions
What is vacuum forming?
Vacuum forming is a manufacturing process that uses heat and vacuum pressure to shape plastic sheets into three-dimensional objects. It allows for the creation of lightweight, detailed designs suitable for various applications.
What materials are commonly used in vacuum forming?
Common materials for vacuum forming include acrylic, polycarbonate, PVC, HIPS, and PETG. Each material has unique properties that make it suitable for specific applications, such as packaging or prototyping.
How does the vacuum forming process work?
The vacuum forming process involves heating a plastic sheet until it’s pliable, placing it over a mold, and then using a vacuum to suck the sheet down onto the mold, allowing it to take shape as it cools.
What equipment do I need for vacuum forming?
Essential equipment for vacuum forming includes a vacuum forming machine, heat source, molds, vacuum pump, clamps, frames, and safety gear. These tools ensure the process runs smoothly and safely.
What are the applications of vacuum forming?
Vacuum forming is widely used in packaging for electronics, food, and cosmetics, as well as in prototyping and model making for architecture and automotive parts. It’s especially valued for its speed and cost-effectiveness.
Why is vacuum forming considered cost-effective?
Vacuum forming is cost-effective due to its ability to produce detailed components quickly and with minimal waste. It’s particularly advantageous for small to medium production runs before moving to mass production.
Can I make custom shapes with vacuum forming?
Yes, vacuum forming allows for creating custom shapes tailored to specific needs. By designing unique molds, you can achieve precise shapes and details in the final product.
Is vacuum forming suitable for beginners?
Yes, vacuum forming is beginner-friendly, provided you have the right equipment and guidance. With basic knowledge of the process and materials, beginners can produce high-quality products.
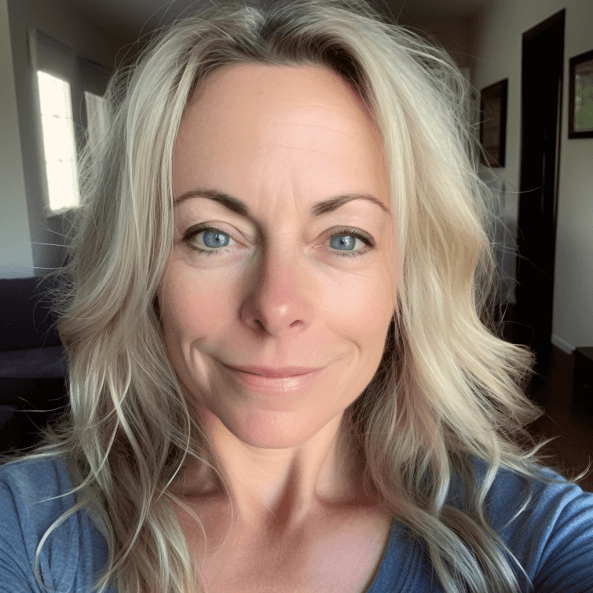